
For nearly a quarter of a century, Machine Sciences has been on the move. Since its start in 2001 by Founder & CEO Brian McCabe (who remains its majority owner), the company has grown more than 20% annually, changing locations as it expanded shop floor space, eventually settling in Tualatin, Oregon in 2020. The space is unique in that McCabe and his team partnered with a developer to determine how the building would be designed, maximizing shop layout and workflow. This forward-thinking approach mirrors Machine Science’s commitment to working with emerging technologies in satellites, rockets, drones, and advanced air mobility vehicles.
Planning the work space
Machine Science’s 72,00ft2 CNC machine shop houses a robust Fastems automation system and 34 CNC machines – 10 of which are 5-axis mills and 6 are lathes – and the shop’s laid out in six work cells.
According to McCabe, “The idea is there’s redundancy in equipment in each cell, so if one piece of equipment has a maintenance issue or is over-scheduled because of increased demand for a part, we have the same or comparable equipment next to it to which we can transfer the job.”
The lathe cell contains three mill/turns, two lathes with live tooling, and a Swiss screw machine. A vertical cell contains 11 machines (10 Haas mills and one FANUC Robodrill). Four DMG MORI DMU 50 machines are in the 5-axis prototyping cell.
“In the first three work cells our operator interfaces with the machine,” McCabe says. “The last three cells are all linear-pallet cells connecting multiple machines with automation.”
The final cell features three GROB 552’s – two standard and a 552T 2+1 turning center – with two more machines on order. “We designed this last cell along with Fastems to accommodate five matching machines,” McCabe adds. The first three machines operate 24/7 with two pre-installed pallet systems ready and waiting for the final two machines.
Often, machining centers are available with the manufacturer’s optional pallet loading stations. Machine Sciences’ needs were more complicated, requiring the team to look elsewhere for an automation solutions partner. “We had one cell system with two load stations and one with four,” says Process Engineer Chris Luis. “We found we really liked having the extra load stations and when the GROB cell system is fully up and running, it will have four load stations, 108 pallets, and five machines. This was the maximum that could be installed in the 110ft clear span of the building. We wanted to have four load stations so operators can keep the machines fed and parts moving through.”

Fastems designed a pallet changing system consisting of a single pallet for the GROBs resembling a lazy Susan with a pallet waiting at each machine. A robot replaces each pallet as it’s taken, significantly reducing machine waiting time.
“Another big draw for me as an operator who runs it all is having the data the Fastems system collects,” Luis adds. “I keep live tooling inventories for all the machines in the system. Even the tool holders appear on the screen, and it makes it easy for me to see where my empty tool holders are.”
Having tool holder inventory at hand and viewing the pallets and scheduling has been invaluable. The team can see when material stock is running low and plan for big jobs without keeping a large material inventory. The machines each contain 140 tools with an additional 200 tools in an external magazine on each machine.
Designing the work cell
Machine Sciences’ growth played a part in their decision to go with a Fastems modular pallet loading system. It provided the flexibility needed within the cell system. Early in planning, Luis suggested Fastems, and the company worked with distributor Machine Tools Northwest’s Vince Selway and Fastems’ International Sales Manager Robert Humphreys to determine which system was best. Ultimately, they decided on the modular Fastems Flexible Manufacturing System (FMS) comprising a rail-guided transportation vehicle, a setup station and material station, buffer storage, a control system, and integrated machine tools.
“A big thing for us was Fastems drew out the entire system and helped figure out exactly how many machines we could fit in the area planned for a 5-axis cell system, how we could fit all five GROB machines on the 18" steel reinforced concrete slabs poured with the original building foundation, and locating exactly where in the shop everything needed to go,” Luis explains. “We went through several iterations with Fastems lining up all the machines and Fastems equipment. We also had CAD drawings of our shop showing all the machines and including all our slab-lines.” Eventually, every individual machine foot of the cell system was aligned to ensure everything was falling on the concrete slabs and the machines weren’t too close to any slab seams. “Planning it out with the Fastems team really took the majority of the work of getting the cell system designed and planned out,” Luis recalls.

McCabe adds, “We were working in such a tight space that every edge mattered. We had to make sure we were going to get in and out with chip bins and whatnot. We had guys from Fastems mark on the floor exactly where components of the Fastems system would fit, down to the millimeter.”
One pressing need was fitting as many spindles into the space as possible. According to Humphreys, they eventually ended up with five machine locations with four load stations – in addition to the existing systems. They had to figure out how to build the cell without complicating the current setup. “The machines are landlocked after installation,” Humphreys recalls, “so we installed them back to front. Machines five, four, and three were installed and the open slots are currently open for machines one and two arriving soon. It was a tricky process, and it took a lot of patience to make sure everything fit. It’s quite a work of art.”
Luis and McCabe found the cell was the most important factor to consider when designing the space, and then everything else, from the type of machines to other equipment, was decided after the cell layout was finalized.
McCabe says, “Most shops will say ‘these are the machines we want, what cell can you provide for these machines?’ We asked, ‘this is the cell we want, what size machine and what else can we put in the cell to best use our space?’ Fastems was great at working on different iterations so we could make better use of the larger machines we needed the most.”

Success
The GROB cell helps Machine Sciences meet some of its biggest challenges, especially machining complex satellite and drone parts with very short lead times. One customer has asked that Machine Sciences be the sole provider for all the parts on their drone bill of materials – 111 complex parts that need spot drops on all of them.
“The Fastems cell helps us because we’ll just need to set the pallets and indicate it’s a high-production job,” Luis says.
They anticipate making 200 of these parts in different batches throughout the year. The pallets can be set up in storage according to the job specifications and Luis can upload the schedule to the Fastems Manufacturing Management Software (MMS) system according to customer deadlines. The entire job is then ready to go.
Luis says some orders have quadrupled over the years and the ability to set up and load multiple pallets, get the materials lined up on the machines, and schedule unattended production time has made a significant difference in meeting these new deadlines. The MMS software also helps keep things humming thanks to Machine Sciences’ investment in the Ultimate software package including a DNC program and tool magazine management along with dashboard and reporting software modules. Luis appreciates the ability to view data on spindle run time to measure machine performance and how much run time they can expect to get from a particular spindle. The software goes one step further, though, and shows how much time a particular job took to complete and which program was used, so he can estimate run time for more accurate scheduling.

“One feature I really like is when I’m looking at spindle run times, I can have the operators specify why a machine is taken offline when it’s taken out of automatic mode,” Luis says. “I can take a look at the notes and see it was switched from auto to manual mode for a new part setup and the spindle hours were still captured.”
Summing up
For a shop focused on precision manufacturing for space, aerospace, and military customers, the ability to meet changing specifications on short notice is paramount to keeping the machines running. The ability to provide accurate and traceable data during every step of the manufacturing process helps with the reporting required of an AS9100-certified and ITAR-compliant operation. By partnering with their automation supplier Fastems, Machine Sciences tailored their space and processes to their customers’ needs and, therefore, their own needs as well, starting from the smallest inch to the massive final space.
DMG MORI USA
https://us.dmgmori.com
FANUC America
https://www.fanucamerica.com
Fastems LLC
https://www.fastems.com
GROB Systems Inc.
https://www.grobgroup.com
Haas Automation Inc.
https://www.haascnc.com
Machine Sciences Corp.
https://www.machinesciences.com
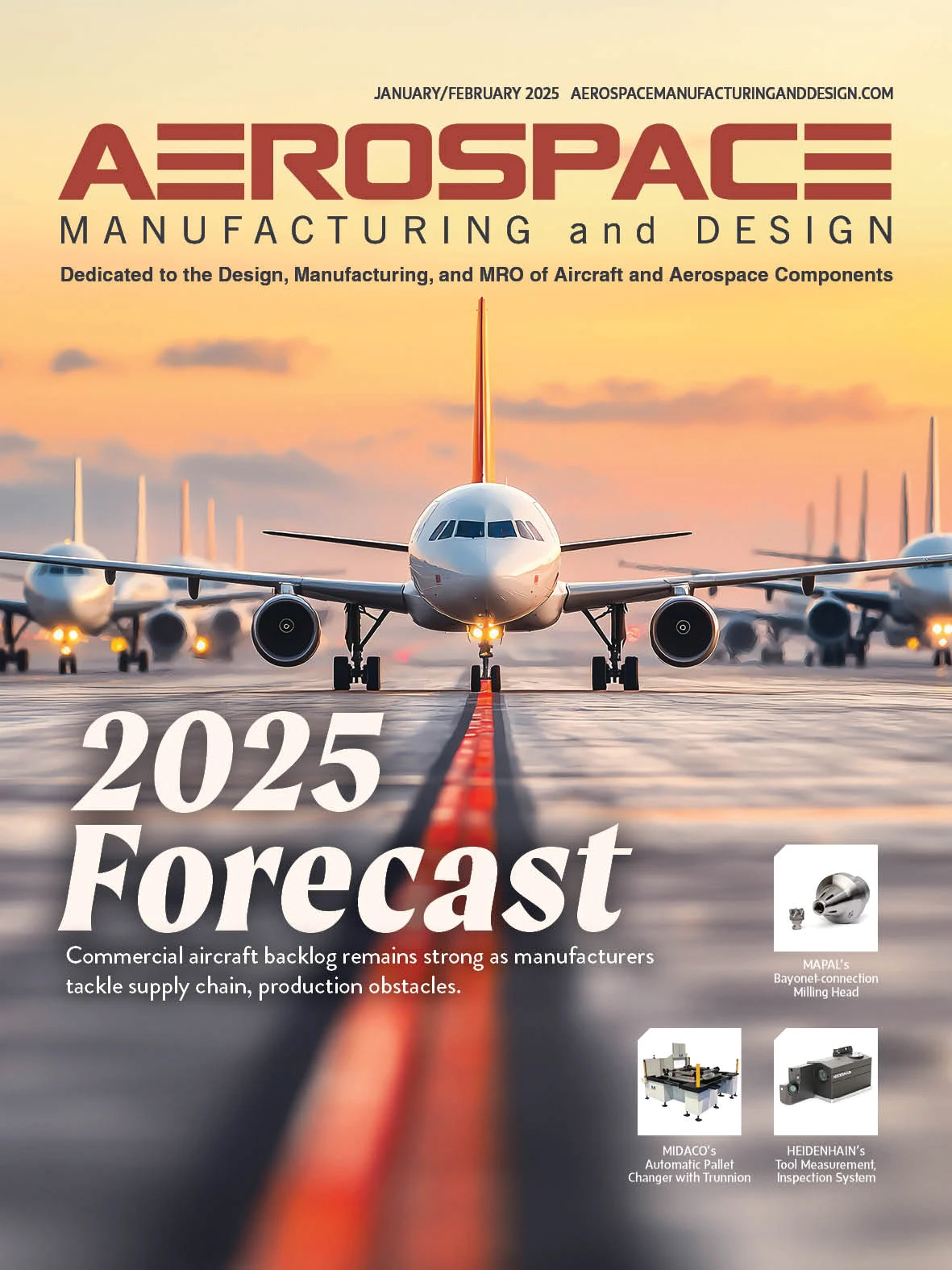
Explore the January/February 2025 Issue
Check out more from this issue and find your next story to read.
Latest from Aerospace Manufacturing and Design
- Fixtureworks introduces Stablelock Clamps
- Piasecki acquires Kaman's KARGO UAV program
- PI Americas’ long-travel XY piezo nanopositioners-scanners
- AAMI project call submission deadline extended to May 12
- Jergens launches cast iron tooling column additions
- Airbus to acquire assets relating to its aircraft production from Spirit AeroSystems
- FANUC America's Cobot and Go web tool
- Chicago Innovation Days 2025: Shaping the future of manufacturing