
During the past five decades, Nidec Drives’ UK manufacturing facilities have undergone significant expansion and transformation and a new solution was required to tackle a critical challenge.
Movement of raw materials from the warehouse to the module assembly plant was handled manually. Operators transported materials between buildings via forklifts and internally across three separate levels. This process was time-consuming and resource intensive. Given the complexity of interlinking different levels within the facility, a custom solution was essential.
“We conducted value stream mapping, and by taking an overview of production, preparation, and process, were able to formulate the plan for a conveyor and lift system which would move raw materials around the factory, where they needed to be, and when they needed to be,” says Jamie Evans, warehouse and distribution manager at Nidec Drives.
Identifying the right partner
Evans embarked on a mission to find the ideal vendor for implementing the latest advancements in automated warehouse solutions.
“We invested significant time in researching the right supplier to collaborate with us on achieving the optimal solution. Through extensive dialogue and interaction with Invar, they emerged as the clear frontrunner,” Evans says.
Invar are intralogistics engineering experts who provide turnkey automation solutions specific to individual clients and proposed a solution fully tailored to Nidec Drives’ needs and values.
Variable speed drives for conveyor system
One unique feature of Nidec Drives’ UK manufacturing site is that, where possible, the automated machinery in use – from component store cranes to production equipment – runs on the Control Techniques variable speed drives Nidec Drives manufactures. The new conveyor and lift system would be no exception.

By combining teamwork and top-quality components and incorporating Control Techniques variable speed drives, Invar successfully completed the project ahead of schedule and within budget.
Providing a sustainable solution
Invar’s solution involved implementing a tote transportation system comprising approximately 300m of Interroll-powered tote conveyor and three Nerak lifts, spread across three buildings. The conveyor system features two tiers for goods in/out and the main assembly area. Operators use screens at the infeed stations to select the tote’s destination.
In any building on the manufacturing site, the tote license plate number (LPN) is scanned, and the operator places the carton onto the powered conveyor, selecting the tote’s destination using the human machine interface (HMI) screen. The tote is then transported to the first lift and directed to the operator station. Once the operator has completed their tasks, the process of scanning the LPN, choosing the destination, and dispatching the materials is repeated. Additionally, in the store area of the facility, the lift allows for infeed or outfeed from both sides, depending on where the materials need to go next.

However, the true efficiency lies in the system’s ability to operate on demand, halting completely between tote loads. This energy and cost-saving feature significantly reduces unnecessary consumption of resources and is expected to achieve a return on investment (ROI) in less than a year.
Leveraging Control Techniques products
Integral to the efficient stop/start nature of this system are the Control Techniques drives. For this project, two types of drives were used: three Unidrives and 11 Digitax HD M750.
The Control Techniques Unidrive was selected for the lifts within the system. Unidrive offers exceptional control stability and bandwidth for all industrial motor types, with the M702 variant featuring onboard Ethernet and dual STO inputs.
Several option modules were fitted to the Unidrive. The SI-I/O Interface Module provided additional input and output connections. The SI-Universal Encoder Module, which ensures positional accuracy by connecting to a rotary encoder on the motor, was also added. This module checks if the encoder’s value matches that of a second encoder measuring position with a laser; if the values align, the programmable logic controller (PLC) allows the drive to run; if not, the system’s brakes are applied.
Nidec engineers also used the PTi210 Easy Motion Controller with no need for software development – it plugs into the drive and is connected through PowerTools Studio software for creation of quick, simple, repeatable routines which the Unidrives in the conveyor execute repeatedly. The PTi210 is compatible with both Unidrive and Digitax HD M750 drives.
For single-axis motion with complex controls such as the conveyor, the PTi210 and PowerTools software package is a cost-effective way to provide simple, fast, and effective motion control. Users of all skill levels can configure, program, select functions, and set up parameters, expediting configuration, management, and long-term maintenance of the conveyor.
Finally, the KI-keypad was installed, allowing users to adjust drive parameters while displaying key information such as current draw, RPM, or faults.

The Control Techniques Digitax HD M750 servo drive series complements the Unidrive range by maximizing servo performance in a compact package. Digitax HD M750 is optimized for high-dynamic applications, offering flexibility in standalone and modular configurations. This drive delivers full servo control, plus open-loop permanent magnet motor and induction motor control, across four functionality levels: EtherCAT, MCI machine control, Ethernet, and the flexible Base servo drive.
The Digitax HD M750 drives chosen in this project were used for controlling the drum motors along the powered roller conveyors, and on the conveyor belt’s incline and decline. This drive was selected for its compact size, while offering high power density, dual STO, and ability to communicate on the PROFINET network.
As a full machine control solution, the Unidrive works with three Leroy-Somer IMfinity 3-phase induction motors, one on each lift of the conveyor. Provided by Nidec ACIM, IMfinity motors reach premium efficiency up to IE4 to maximize energy savings, enhance performance, and optimize lift productivity. Design of the IMfinity range of Leroy-Somer motors ensures performance and reduced cost of maintenance. To work with the Unidrive, the IMfinity motors have winding protection as standard, thermal reserve for maintaining the rated torque over an extended speed range, and adaption of the metal support plate to reduce electromagnetic noise.
The application of various Nidec components within the Invar conveyor provides an efficient, modern, and functional conveyor and lift system.
Impact and future developments
Installation of the new conveyor and lift system was completed in just four months. Since implementation in April 2024, impact on productivity and staff morale has been significant. The team can now retrieve parts without physically moving and accessing bulk materials, production bottlenecks have been eliminated, and individual efficiencies have markedly increased.
“The conveyor is just the latest step in our ongoing efforts to enhance our manufacturing facilities,” Evans says. “We are always exploring the next steps we can take to improve efficiency and quality, and we look forward to further growth.”
“At Invar, we install a legacy for our clients,” says Sham Jama, project manager at Invar. “We work hard to meticulously maintain every element of our solution through custom maintenance, communication, and strong connections with our customers. This project ran so smoothly with the help of Jamie and his team, I believe this marks the beginning of a long and fruitful relationship.”

Looking ahead, Nidec Drives is considering the implementation of autonomous mobile robots (AMRs) at the UK manufacturing site. AMRs address many challenges in high-specification manufacturing by independently navigating their environment picking, sorting, and transporting components.
Nidec Drives will collaborate with Nidec Automation, which produces motors, motor control solutions, integrated drive solutions, and battery management systems for AMRs, to explore how these robots can further improve efficiency and quality at the Nidec Drives manufacturing site.
Invar
https://www.invargroup.com
Nidec Drives
https://acim.nidec.com/en-US/drives/control-techniques
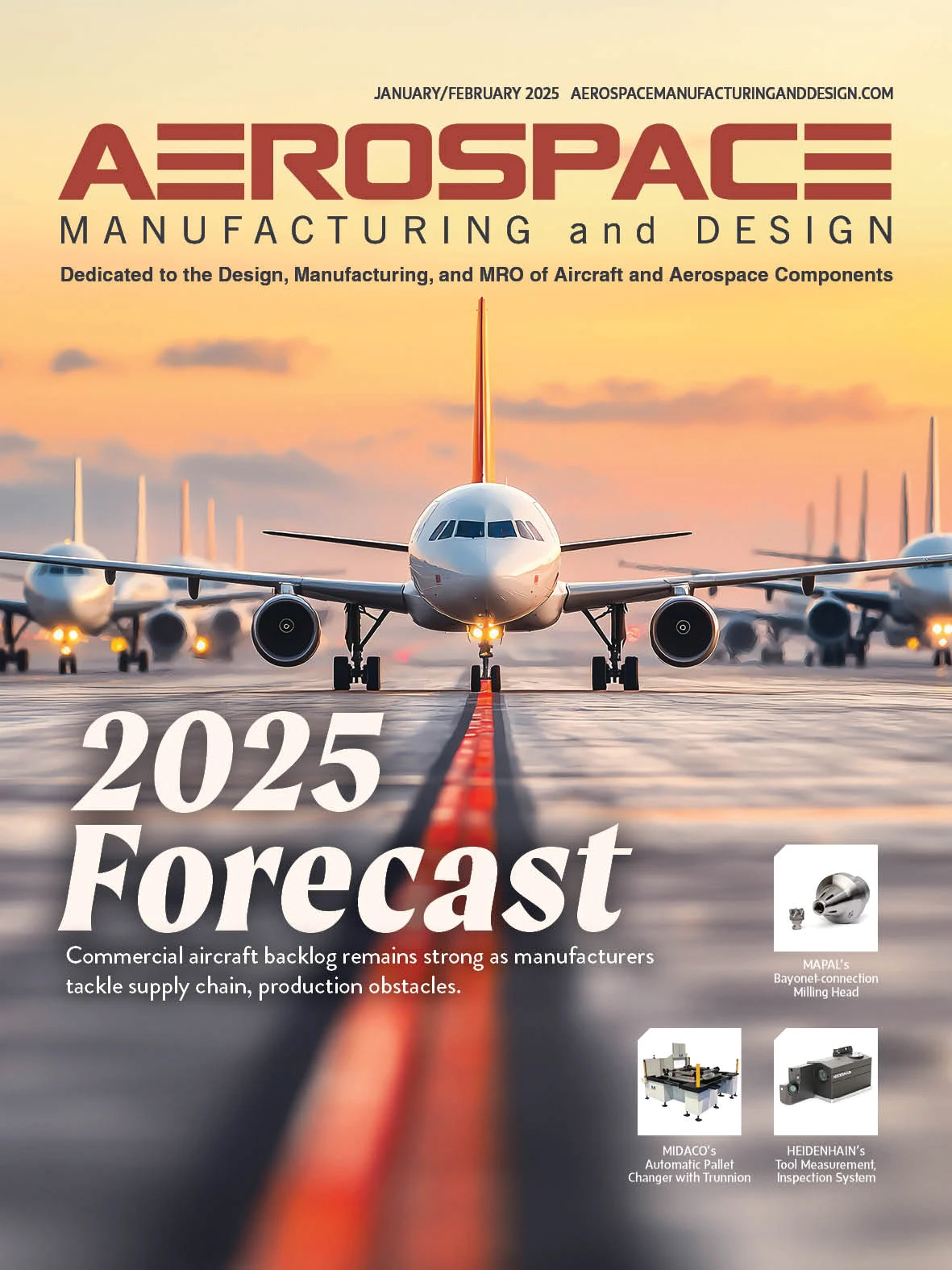
Explore the January/February 2025 Issue
Check out more from this issue and find your next story to read.
Latest from Aerospace Manufacturing and Design
- Lockheed Martin completes Orion for Artemis II
- Cylinder CMMs for complex symmetrical workpieces
- University of Oklahoma research fuels UAS development
- Motorized vision measuring system
- Everyone's talking tariffs
- Boom Supersonic to launch Symphony engine testing in Colorado
- Next-generation precision measurement solution
- #60 - Manufacturing Matters: What's ahead in manufacturing in 2025?