Boeing has invested in Digital Alloys Inc., a Burlington, Massachusetts-based company developing high-speed, multi-metal additive manufacturing (AM) systems that produce 3D-printed parts for aerospace and production applications.
Digital Alloys’ Joule Printing technology rapidly combines multiple metals into each part, enhancing thermal, electrical, magnetic, and mechanical properties. The process allows metals such as titanium and high-temperature alloys to be 3D-printed for parts that could be used on Boeing products.
“Our investment in Digital Alloys will help Boeing produce metal structural aerospace parts faster and at
3D-hybrid machining center
The automatic tool change solution for systematic 3D hybrid manufacturing is incorporated into the H12 double column machining center. The hybridized machine boasts X
The pairing provides machined internal features and complete processing in one work offset. Increased freedom of complexity, lower costs in material and processing time, and novel materials combine with additional capability, repair, and salvage of large parts. Repairing and filling worn surfaces with material stronger than the original, followed with final machining, can eliminate downtime and extra costs. http://www.3dhybridsolutions.com; http://www.takumiusa.com
3D printer for carbon-filled nylon
The Fortus 380mc Carbon Fiber Edition (CFE) additive manufacturing (AM) system is dedicated to carbon-fiber-filled Nylon 12, incorporating 35% chopped carbon fiber by weight and a high stiffness-to-weight ratio. Nylon 12CF is up to 4X stronger in the X- and Y-axis, and it will maintain its mechanical properties at a 40% higher temperature.
Parts don’t exhibit appreciable warpage or shrinkage and will hold
Parts are built in 0.010" (0.254mm) layer thickness. The system is also compatible with ASA thermoplastic, which can build in 0.010" or 0.005" (0.254mm or 0.127mm) layer thicknesses. The 3D printer’s build chamber offers water-soluble support material removal, eliminating the need for manual labor to remove supports for fine and intricate geometries. http://www.stratasys.com

3D filament system
The ZSE-3D twin screw extrusion system facilitates development and production of 3D filaments from a co-rotating or counter-rotating twin screw extruder. Direct extrusion of raw materials facilitates rapid product
Formulations can be modified on the fly for rapid sampling of filaments with different formulation percentages. A sample can be produced every 10 minutes. The system is rated for 425°C operation and can be configured for water-soluble and high-temperature engineering polymers. http://www.leistritz.com


Additive manufacturing demostrations available
Renishaw has opened an additive manufacturing demonstration center in Newbury Park, California. Working in collaboration with Ibex Engineering, the demonstration center is within Ibex’s headquarters and allows visitors to explore, interact with, and use Renishaw’s metal additive manufacturing (AM) systems.
The center can print high-precision titanium (Ti64Al4V) parts on Renishaw’s
Wet downdraft, heat treatment, support, machining, inspection, and part removal equipment work in concert with the AM system to ensure parts are printed to specifications.
Also available at the site is

CAD file viewer
K-Display View software multi-platform program for CAD file viewing is built on the universal CAD architecture of the Kubotek Kosmos 3D framework.
Available on Windows, Mac and Linux, and the iOS and Android mobile platforms, the software replaces the Kubotek Spectrum multi-CAD viewer software. It provides a streamlined user interface and faster operation.
No additional CAD software or Internet connection is required, enabling manufacturing, sales, support, and service departments read-only versions of files from commonly used CAD programs including SolidWorks, AutoCAD, PTC Creo, Siemens NX, CATIA V5/V4, and neutral formats such as IGES, STEP, Parasolid X_T, ACIS SAT, and STL. http://www.kubotek3D.com
AGS joins America Makes
AGS Additive Manufacturing has joined America Makes, the nation’s collaborative partner in additive manufacturing (AM) and 3D printing technology research, discovery, creation, and innovation.
“We look forward to collaborating with other leaders in the AM field,” says Kevin Goold, AGS 3D printing manager. “Being a third generation,
AGS Additive Manufacturing, based in Fort Worth, Texas, specializes in 3D printing metals such as steel, aluminum, titanium, cobalt chrome, and Inconel. http://www.aaaswis.com/AGS/index.html; https://www.americamakes.us/
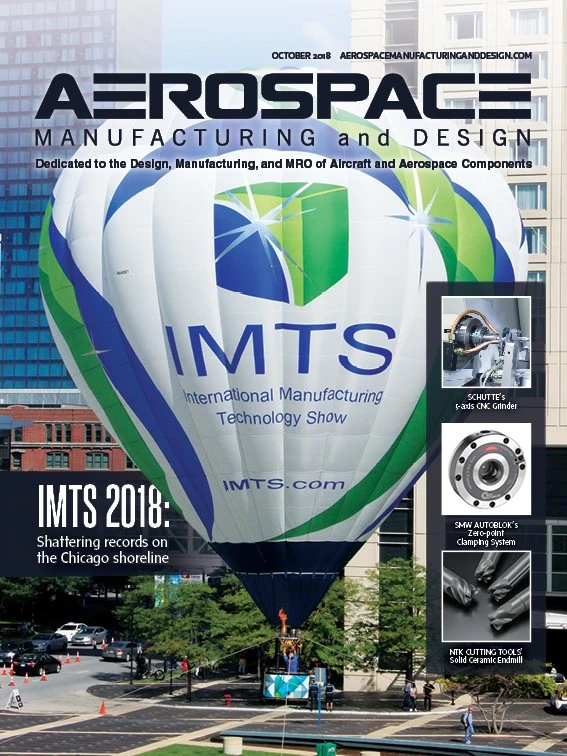
Explore the October 2018 Issue
Check out more from this issue and find your next story to read.
Latest from Aerospace Manufacturing and Design
- NASA offers free high school engineering program this summer
- Pemamak's PEMA Vision 3D software
- Aerospace Industry Outlook - Spring 2025, presented by Richard Aboulafia
- Panama’s National Air and Naval Service selects Embraer Super Tucano
- Model 5770 Linear Abraser
- #42 Lunch + Learn Podcast - Quell Corp
- RECARO Aircraft Seating showcases advanced comfort solutions at AIX 2025
- Mitutoyo America’s MiSTAR 575 Shop Floor CNC CMM