
High-purity ceramic aluminum oxide abrasive grains are manufactured using seeded-gel (SG) sintering technology that controls crystallite growth nucleation by introducing nano-particle (<100nm) alumina seeds. The process generates a heterogeneous structure of crystallites in the 100nm to 500nm range, creating an abrasive that can fracture at a controlled rate at the sub-micron level to constantly create thousands of new cutting points.

The exceptionally hard and durable grains, when used in precision grinding wheels, process difficult-to-grind steels and alloys. Developers further improved cutting ability by modifying the SG grain shape, replacing post-sinter crushing with a pre-sinter extrusion process. The result was a family of filamentary or needle shaped grains, designated as Norton Targa, with 5:1 and 8:1 aspect ratios (Fig. 1).
In addition to high toughness, they also have low packing density. Typical blocky grains have about 50% packing density whereas the extruded grain with an 8:1 aspect ratio has a packing density closer to 30%. Wheels made with this grain have very high permeability/porosity for coolant carrying. The high aspect ratio presents a shape factor comparable to a much larger blocky grain, which in turn creates a much larger chip and lower specific cutting energy. These factors make Targa grains suited to high stock removal rates when grinding many different materials. SG and Targa abrasives are normally blended in various percentages with other abrasives, such as fused aluminum oxide, to optimize grinding performance for different applications and materials. The higher the percentage of premium engineered abrasives, the more the wheel costs. A recent study conducted at Norton|Saint-Gobain’s Higgins Grinding Technology Center (HGTC) sought to understand how blending engineered abrasive grains impacts abrasive performance and grinding wheel wear.

Method
Figure 2 shows the test configuration.
- Test piece: 50.8mm x 203.2mm IN718
- Machine: 75kW spindle creep feed grinder with water soluble
coolant mixed to 10% - Wheel: 508mm x 203.2mm x 50.8mm
- Wheel speed: 22.86m/s
- Dressing: overhead diamond roll, 0.9 speed ratio, 1.016µm/rev plunge rate

A radial depth of dress greater than the radial depth of the grind removed worn areas of the wheel. Each wheel was tested at increasing material removal rate (MRR') until excessive wheel wear was experienced (Table 1, page 19). Two grinds were completed at each MRR' condition to confirm repeatability. A depth micrometer measured radial material removed from the part and a profilometer measured surface finish.
With each wheel test, engineers ground a Formica coupon and measured it with a profilometer to discern wheel wear.
Results
The 30% and 50% blended Targa wheels appear to have very similar grinding power at every MRR' condition tested (Fig. 3). On the other hand, the 100% Targa wheel appears to draw slightly higher power at every MRR' condition compared to the blended Targa wheels. The increase in grinding power is only about 6% to 8% and therefore does not pose a problem for most work materials. However, when grinding materials with low thermal diffusivity, even a slight increase in power could increase the probability of thermal damage or thermal cracking of the ground workpiece. Attention should therefore be paid to the specific power and cutting energy increase when grinding with the 100% engineered ceramic wheel.

Typically, as MRR' increases, the G-ratio decreases due to increase in wheel wear (Fig. 4). This phenomenon is also seen in the 30% and 50% blended Targa wheels. Neither blended Targa wheel was tested beyond 40(mm3/sec)/mm due to rapid wheel wear with G-ratio values approaching zero. The 100% Targa wheel had stable wheel wear and G-ratio with increasing MRR' up to 60(mm3/sec)/mm. This demonstrates the benefits of an all-engineered ceramic grinding wheel – higher MRR' and productivity without drastically increasing wheel wear.



During wheel dressing (Fig. 7), 100% Targa ceramic wheels draw the highest horsepower, followed by 50% and 30% blended ceramic Targa wheels, showing that Targa grains require higher forces to fracture during dressing. As the blend percentage of the premium ceramic grains increases in the grinding wheel, the life of the dress roll will decrease. Therefore, the overall cost of grinding will increase.
Summary


Material Removal Rate (MRR’)

Increasing the percentage of the engineered ceramic grains in grinding wheels increases productivity by ramping up stock removal rate and reducing cycle time, without an increase in wheel wear or worsening component surface quality/finish. However, higher blend percentages also increase specific cutting energy and dressing power/forces. So, pay attention to these two aspects to avoid thermal damage to burn-sensitive components, as well as the negative impact on the life of the dress roll used. Grinding with a full understanding of the impact of blending engineered abrasive grains lets operators make adjustments to improve overall grinding performance while minimizing cost increases.
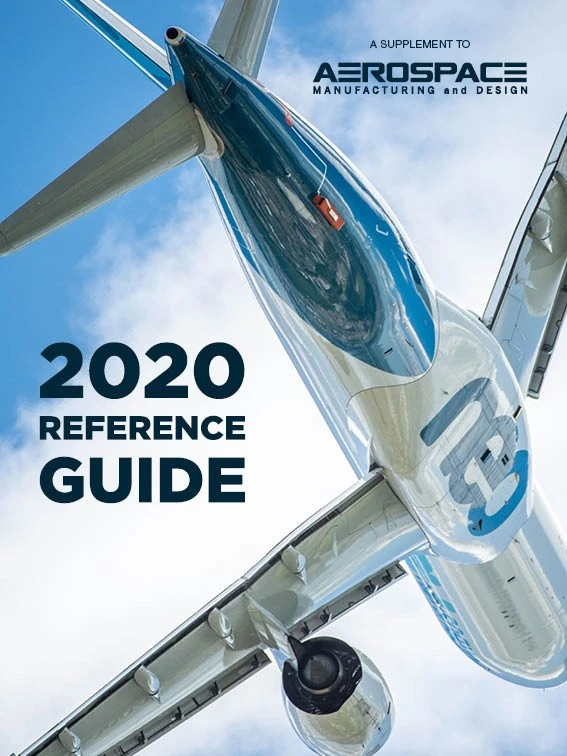
Explore the AMD Reference Guide 2020 Issue
Check out more from this issue and find your next story to read.
Latest from Aerospace Manufacturing and Design
- AIX shows aircraft interiors are a strategic priority for global airlines
- Machine Tool Builders Roundtable: Turn equipment into expertise
- No time to waste: How to machine MedTech parts more efficiently
- The 5 Best and Fastest Spindle Repair Services
- Mill smarter, not harder: How collaboration optimizes production
- Be proactive – stay ahead of tariffs and other economic and supply chain curveballs!
- Taiwan’s China Airlines orders Boeing 777X passenger, freighter jets
- Reamer re-tipping extends life of legacy tooling