BigRep delivered its 500th large-format industrial 3D printer – BigRep One – since the company was founded in 2014.
“This delivery is more than just a figure; it shows how much industrial customers value our products and the production freedom they create. We greatly appreciate this trust and will continue utilizing the full potential of additive manufacturing (AM) applications to the benefit of our customers, new and old,” says BigRep Managing Director Martin Back.
The announcement is the latest in a string of product and service launches such as the opening of a 3D printing service in Boston, Massachusetts, BigRep 3D Partlab, which will provide 3D-printed parts on demand. Other recent launches include the Studio G2 printer, and four engineering-grade filaments: PA6/66, PET-CF, PLX, and BVOH.
BigRep
https://bigrep.com

High volume, metal 3D printer
Built for high throughput and large-part production, the X1 160PRO metal 3D printer provides 800mm x 500mm x 400mm build dimensions, delivering 160L total build volume.
The open material system is capable of 3D printing six qualified metals, including stainless steels 316L, 304L, and 17-4PH, and some ceramics, into dense, reliable final parts using the triple advanced compaction technology (ACT) system.
With faster than 10,000cm³/hour print speeds, the X1 160PRO delivers quality parts at production speeds. The system features Industry 4.0 cloud connectivity and process-linking capabilities by Siemens MindSphere.

Advanced materials testing
3D Systems has completed comprehensive testing for its newest Figure 4 materials to comply with ASTM and ISO standards. Production-grade materials for its Figure 4 Platform save customers time, reduce costs, and speed time to first part.
Figure 4 materials designed for production applications include:
- Figure 4 PRO-BLK 10
- Figure 4 EGGSHELL-AMB 10
- Figure 4 HI TEMP 300-AMB
- Figure 4 FLEX-BLK 20
- Figure 4 RUBBER-BLK 10
- Figure 4 TOUGH-BLK 20
- Figure 4 MED-AMB 10
- Figure 4 MED-WHT 10
These materials improve first-time print yield, heat deflection, UV stability, durability, flexibility, and impact strength, while also enabling biocompatible and direct digital production workflows.
3D Systems
https://www.3dsystems.com
Dassault Systèmes, Xometry offer design environment part production
Dassault Systèmes and Xometry are partnering to provide customers with integrated ways to produce parts that accelerate concept to manufacturing. Solidworks and Catia users will have automatic, immediate access to Xometry price quotes on the MAKE Marketplace for manufacturing parts, without leaving their design environment.
Engineers can play a greater role in the design-to-manufacturing aspect of part production by focusing on the shape of a prototype and the cost to produce it. Users can view Xometry price quotes on their screen in the context of their design, and click to have it manufactured, while still getting instant or manual quotes from other MAKE Marketplace suppliers.
“We launched the MAKE Marketplace in 2018 to make it easy for customers to design and manufacture. Our partnership with Xometry takes this a step further,” says Sébastien Massart, head of corporate strategy, Dassault Systèmes. “Customers can order high-quality additive manufacturing or CNC machining parts in one click, reducing friction customers face going from design to manufacturing.”
Dassault Systèmes
https://www.3ds.com
Xometry
https://www.xometry.com
Get curated news on YOUR industry.
Enter your email to receive our newsletters.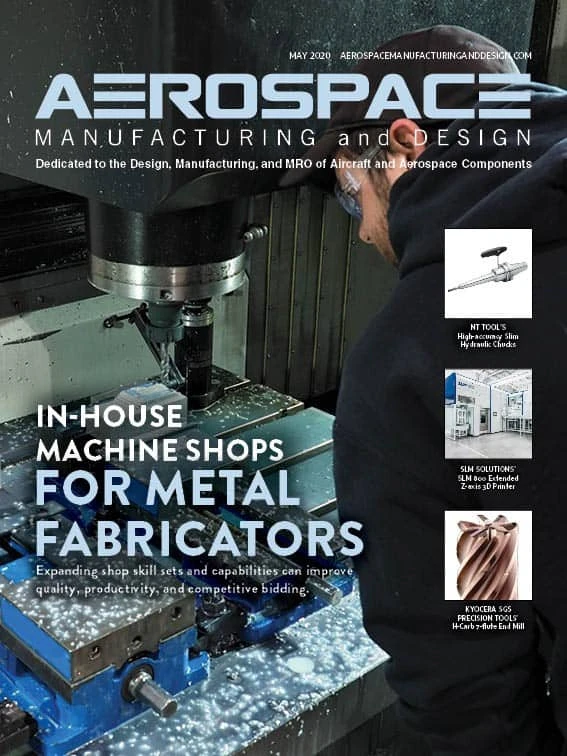
Explore the May 2020 Issue
Check out more from this issue and find your next story to read.
Latest from Aerospace Manufacturing and Design
- Ralliant to establish global headquarters in North Carolina
- Philatron MIL-DTL-3432 military cables
- Beyond Aero refines its hydrogen-electric light jet
- Americase's advanced protective solutions
- Social media - what are your thoughts
- GE Aerospace secures Air Force engine contract
- Thomson Industries' online sizing and selection tool
- #53 - Manufacturing Matters - 2024 Leaders in Manufacturing Roundtable