
Aerospace manufacturers must be aware of how technology is changing to be ready to adopt smart systems to compete at a national and global level. Smart factories gain clear visibility into process flows, and they are better able to manage the complexity of high-mix production.
Insights into how well work flows through operations allow business leaders to manage priorities if issues occur and they can make the necessary changes using process control.
What needs to happen to successfully install these systems and achieve a competitive advantage? James Crean, co-founder, president, and CTO of Crean Inc., says it’s about fully integrating three key aspects – people, processes, and technology.
“The technology is there, and it’s continuing to evolve very rapidly,” Crean says. “It’s critical to not just have a technology solution but a people solution and a process solution that goes along with that and is integrated. Technology is only one part of the equation.”

Keep the end in mind
When identifying how to adopt smart technologies, companies should develop a clear list of solid goals and objectives for specific projects.
“For business leaders who are implementing a smart factory, they need to understand that it takes an integrated approach with a cross functional team, and whether that includes outside experts or not, you’ve got to have the right folks on the team to begin with,” Crean says.
Smart factory transformation requires integrating people, processes, and technology at the same time. Crean says there can be a tendency to over-focus only on technology. To avoid this, companies need outstanding people, leading-edge technology, and modern, flexible process methods that deliver faster, establish competitive cost objectives, and target game-changing performance.
“The technology solution, in a lot of ways, is often the easiest part,” Crean adds. “But at the same time, it’s very easy to make mistakes in an ever-evolving technology space. Manufacturers must select the right technology and have a full understanding of what their goals are to ensure the technology is capable of achieving those goals.”
For example, Crean often helps clients with asset tracking. Many technology options track assets with radio frequency identification (RFID), Bluetooth low energy (BLE), ultra-wide band (UWB), magnetic loops, ultrasound, and cameras with machine learning.
Users must have the right expertise to make sure they select the right hardware tracking solution, and then they must choose the right software to deliver the data necessary for their environment. Every environment has its own factors that need to be considered.
Asset tracking helps organizations ensure the right things are in the right place at the right time, delivering data companies can use to significantly improve operational efficiency.
“You can also integrate the tracking and tracing of work in process with digital routers and digital work instructions,” Crean adds. “That can help you significantly improve productivity even more. And it can also ensure that you’re always delivering the right information to each operator as they work on a part or assembly. And, it also can help you with training and making sure the right operators are getting trained for the work they’re being asked to do.”
Process solution
With technology options chosen, company leaders must recognize that technology adjustments change the process itself. For instance, Crean works with clients who are looking to automate a manual inspection process. While they might expect that they’ll get a 10% or 20% improvement in productivity by automating their inspection process, there’s an assembly step that meters the rate of inspections at the same rate as production. Overall factory productivity won’t change even if managers record an increase in inspection productivity.
“You have to understand and analyze the process and have a solid capacity optimization analysis in hand for your process, as part of understanding how technology is going to improve your operation,” Crean says. “Otherwise, you’re wasting time, money, and resources.”
People
Successful people are at the heart of every successful business change or evolution, Crean explains. This includes corporate leaders and those at every level of their organization. Companies cannot successfully transform without skilled people who can focus on implementing that solution. People in the organization will evolve to use new tools and methods that the smart factory promises. Therefore, it’s important for technology solutions to be people centric, allowing workers to be brought into the solution as opposed to being left behind or viewed as victims of the solution.
Smart flow technology
Crean’s smart flow operating system integrates asset tracking and inventory management data to give users visibility into where everything is located to produce their product. It also gives insight into how to improve operations, delivering an essential level of control.
“We provide hands-on smart factory transformation consulting services, and we deliver an integrated, robust solution that’s tailored for the goals and objectives that our clients are trying to achieve,” Crean says. “We’ll use proven technology from a wide variety of technology providers throughout the world to help implement those solutions and ensure that they’re successful.”
Adapt to change
Focus should not only be on developing an optimized logistics operation. Demands will continue to shift as the industry moves forward, and there will be an increased need for customized products. Companies should be able to customize that product, produce it efficiently and effectively, and implement smart factory technologies that allow them to compete globally. This will position a company to be agile for the future as customers demand more customization.
“There’s a huge change that’s happening, and the future for business must include smart factory solutions in order for them to be able to compete.” Crean adds. “Are we ready for that change from my perspective? Despite a very clear uptick in interest by American manufacturers, they’re still far too many that have failed to recognize the competitive and national security imperative around retooling around these technologies.”
Pivoting is essential. Advanced tracking technology and the digital enterprise will allow companies to pivot quickly and keep their workers safe.
“Every successful technology transformation begins and ends with platform leadership, and a commitment at every level of the organization to be part of that integrated smart factory solution,” Crean says.
About the author: Michelle Jacobson is the assistant editor of AM&D. She can be reached at mjacobson@gie.net or 216.393.0323.
Integrated processes and systems
The ANCA Integrated Manufacturing System (AIMS) connects sequential processes in tool manufacturing, facilitating streamlined tool production and linking separate processes to each other and factory information technology (IT) systems.
AIMS offers functionality adaptable to each factory’s needs; from smaller scale, data-based options to the full AIMS setup across a series of machines. The server manages data flows between the elements of the AIMS system and established IT platforms, such as enterprise resource planning (ERP) systems. Users can choose from a suite of solutions to reduce production costs, resolve labor challenges, and integrate systems to improve product and process quality. AIMS transfers tools between operations with AutoFetch to fully automated tool measurement and process compensation using AutoComp, and managing data via the AutoSet hub.

Radar sensors
DesignCore RS-6843AOP and RS-6843AOPU mmWave miniature radar sensors can implement many different algorithms to measure, detect, and track in robotics and industrial applications. The production-intent sensors feature a 1" cube form factor, heat-spreading metal body, and mounting tabs. They may be used with a PC or embedded platform for field testing, sensing evaluation, algorithm development, and application demonstrations.
Features include the TI IWR6843AOP, a single-chip 60GHz industrial radar sensor integrating a built-in DSP, an MCU, radar accelerator, and antenna array. The IWR6843AOP RF front end integrates a PLL, three transmitters, four receivers, and a baseband ADC. It covers 60GHz with bandwidths up to 4GHz and features 12dBm transmit power and 15dB noise figure or better.
The RS-6843AOP features a header for connection to optional baseboards or hosts providing additional interfaces and functionality. The interface includes I2C, SPI, GPIO, and UART connections. The main interface of the RS-6843AOPU version is a USB-C connector which can act as a power supply input and enumerate two serial UARTS, one for console and the other for processed radar returns or other algorithm output.

Upgraded angle encoders
The ERA 4000 angle encoder series upgrades increase accuracy, ease of use, logistical flexibility, and are compatible with past models.
ERA 4000 angle encoders consist of a steel drum at various diameters with the 20µm, 40µm, or 80µm graduation on the outer diameter, and a scanning unit that reads the graduation. As an incremental system, reference marks are available as distance-coded or one per revolution.

Heidenhain Signal Processing (HSP) allows dynamic control of the LED, and the scanning unit learns of the signal quality coming back from the drum, then adjusts LED intensity on the next signal period. HSP operates in an analog way and increases the speed of the encoder system to 1MHz scanning, a 285% increase.
Two other upgrades to the scanning units are a status LED on the side of the scanning unit, providing unit status during mounting, and the addition of a smaller M12 connector which saves space and is more robust.
Get curated news on YOUR industry.
Enter your email to receive our newsletters.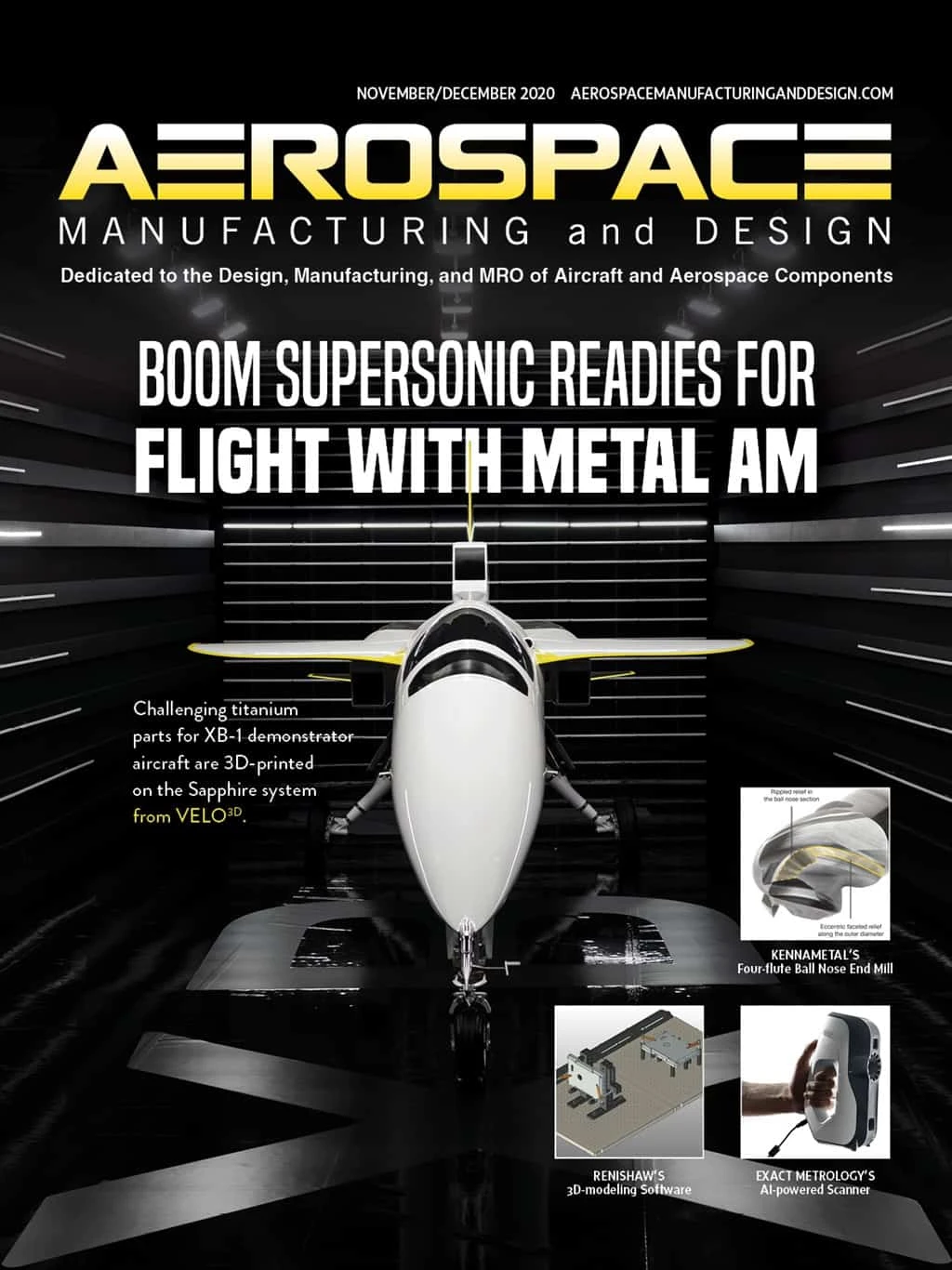
Explore the November December 2020 Issue
Check out more from this issue and find your next story to read.
Latest from Aerospace Manufacturing and Design
- High surface quality at high speed
- #57 - Manufacturing Matters - Agile & Robust Supply Chain Management with Lisa Anderson
- Take control of your manufacturing business despite supply chain turmoil
- Strengthening the defense maritime industrial base for national security, economic resilience
- Register now to learn solutions for high-temperature aerospace machining challenges
- Expertise on machining, joining offered in April’s Manufacturing Lunch + Learn
- NASA offers free high school engineering program this summer
- Pemamak's PEMA Vision 3D software