
“Baby Boomers with a significant knowledge base are retiring at the rate of 10,000 a day.”
No manufacturer can ignore the urgency of that figure.
The quote comes from manufacturing and supply chain expert and president of LMA Consulting Group Inc. Lisa Anderson. She has Boomer retirements topping her list of reasons for the widening skills gap.
Making matters worse is the gap in skilled trades such as CNC operators. Anderson bemoans the lack of focus on high school and community college career paths into manufacturing, citing industry leaders’ unwillingness to invest in solving the problem.
“Those that find a way to bridge this gap have a leg up on the competition,” she observes.
She advises partnerships to counter the skilled-jobs deficit. “Successful executives have set up programs with local community colleges, partnered with trade associations such as the Association for Supply Chain Management (APICS), [and others].”
Further evidence of the problem’s severity is revealed in the 2020 Ohio Manufacturing Survey, conducted by the Manufacturing Advocacy and Growth Network (MAGNET), a resource to help manufacturers grow and compete in Northeast Ohio.
The survey of more than 670 companies statewide represents more than 128,000 of the state’s 700,000 manufacturing workers. Almost 6 in 10 report the skilled worker shortage is hampering their growth, with more than 1 in 4 indicating they are challenged by current worker retirements. While manufacturers are concerned about finding and hiring skilled workers, only about one-third of companies are actively innovating the way they recruit and retain employees.
Hiring strategies continue to focus on traditional sources: 88% use employee referrals, 83% use job postings, 62% use staffing agencies, 44% work with high schools, and 37% work with community colleges.
To grow local manufacturing, MAGNET has developed an Early College, Early Career (ECEC) program to help high school students gain the high-demand skills that lead to successful careers. Local employers hire high school juniors and seniors for paid, on-site work for 1-to-2 days per week throughout a two-year period. Plant managers and technicians train students on skills such as CNC machining and welding. MAGNET mentors and guides students to develop critical thinking, teamwork, and a strong work ethic. Students receive training, hourly wages, manufacturing certifications, college credit, and skills that can lead to job offers and a career in manufacturing.
After students graduate from high school, the employer can offer them a job, which can include tuition reimbursement for a path to college. ECEC allows manufacturers to develop their own workforce and create a sustainable pipeline that helps them compete globally while boosting the region’s economy.
The MAGNET survey notes that Northeast Ohio currently has approximately 8,000 open manufacturing jobs, with those numbers predicted to exceed 10,000 in the next few years. The survey’s authors warn, “One thing is abundantly clear: Ohio cannot become a leader in advanced manufacturing unless we fix the talent gap.”
I will add that no state, nor our nation, can become a leader in advanced manufacturing until we fix the talent gap. – Eric
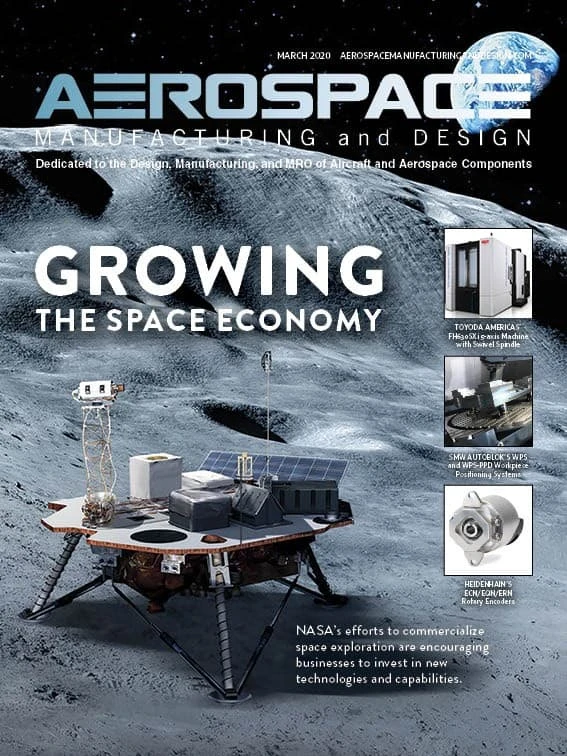
Explore the March 2020 Issue
Check out more from this issue and find your next story to read.
Latest from Aerospace Manufacturing and Design
- NASA-supported technology outfits Venus Aerospace hypersonic engine
- To the Smoothest Surfaces, Finishes, and Beyond | Okuma GA26W
- Extraordinary Starts Where Limits End | Okuma
- Satair, Champion Aerospace sign multi-year distribution agreement
- EMUGE-FRANKEN USA expands N. American solid carbide drill program
- AURA AERO unveils INTEGRAL R to the US market
- Creform Tite-Space AGV fleet
- Cyient Group, Deutsche Aircraft finalize multi-year contract