
The aerospace industry – known for its complex and state-of-the-art systems – still relies heavily on manual labor. Aerospace manufacturers are currently dealing with huge backlogs and need a solution that speeds up production, and many companies are looking to automation to solve this problem.
Traditionally, the industry has been conservative in its approach to automation because the scale and size of aircraft is a unique factor that must be accommodated. Large component sizes often result in operators and robots working simultaneously on a given part; large parts may also mean robots need to be mobile in order to travel to the aircraft part instead of the part traveling to the robot.
Additionally, relative to other industries, aerospace manufacturing is complex and low volume – meaning it has many different tasks to produce very few final products. Aircraft also use materials, such as composites, that are unique to the industry. While these may seem like daunting challenges to overcome, recent advancements address all of these, enabling automation to be even more feasible and practical for aircraft manufacturing.
Benefits of aerospace automation
Automation can increase efficiency since processes can run 24/7 with occasional outages for maintenance. Robots can work in tight spaces and can fit in hard-to-reach locations to further improve productivity. Automation also improves safety since operators no longer need to pick up heavy objects or perform repetitive motion or other potentially dangerous tasks.
In quality control, using robots reduces the potential for human error and allows early identification of potential issues, increasing the reproducibility of production and ensuring the final product does not vary.

Aerospace automation examples
Machine vision, robotics, and manufacturing intelligence are enabling automation of many aerospace processes.
Drilling – Aircraft have numerous holes that must be drilled, and robotics have long been used to improve hole making speed and accuracy. With vision technology, robots can drill holes at specified locations, allowing a job to be performed in a single pass.
Robotics can also apply sealants, paints, and other coatings, especially on large parts such as the fuselage that make manual application difficult.
Automation solutions are also used for cutting aircraft parts. For example, a fully automated workcell uses a robotic arm and state-of-the-art end of arm tooling (EOAT) to drill and cut material. By implementing the work cell, a customer significantly expanded production and achieved high precision and repeatability that reduced rework and product loss.
Transforming the industry
With evolving technologies, digitalization and Industry 4.0 are actively being deployed in aerospace, allowing manufacturers to reap the benefits and remain competitive in the future.
Although aerospace manufacturing is specialized and complex, smart manufacturing is simplifying things. For example, in robotics, some EOAT are Internet of Things (IoT) connected for real-time data collection and optimization. Additionally, scanners can identify the part material, and robots use this information to select the specified bolt size and apply the appropriate level of torque for the material.
Designers and manufacturers will continue to push the envelope on load capacities for robotic equipment and end effectors to effectively handle the largest aircraft components.
Smart technologies and sensors allow manufacturers to collect real-time information to determine operation status and react and adjust operations accordingly. These smart technologies extend into predictive maintenance programs where companies can monitor equipment to improve responsiveness and achieve fewer unplanned outages.
Innovations within artificial intelligence (AI) continue to be implemented, allowing automation solutions to perform increasingly complicated jobs in shorter periods of time.
The aerospace industry is ripe with automation possibilities that are expected to play an increasingly larger role in aircraft production as manufacturers are pushed to lower costs while maintaining quality to remain competitive.

Three-axes miniature gimbal mounts
The YPR60-60-60-01, YPR60-60-60-02 (brushless servo motor driven), and YPR60-60-60-03 (DC servo motor driven) are stacked, precision rotary stages with positional accuracies of 0.05°, repeatability of ±0.01°, and resolutions that depend on the stepper motor driver or servo motor and optical encoder.
Each axis is driven by a 180:1 worm gear and has a large range of travel. The top axis has a 60mm (2.362") diameter table and threaded holes for fixtures or tooling.
The maximum speed with stepper motors is 14°/sec. and 45°/sec. with servo motors. Each axis has a calibrated indicator to display the angle of rotation.
The knobs of stepper motors can be replaced with optional optical encoders for position verification. The YPR60-60-60-02 and YPR60-60-60-02 feature servo motors and optical quadrature encoders for precise closed-loop operation and greater speeds. The YPR60-60-60 (01, 02, and 03) stages are available as plug-and-play with a fully compatible multi- axis motion controller.

XTR controllers, couplers
The 750-8212/040-010 and 750-8213/040-010 XTR controllers have two configurable M12 Ethernet ports and an onboard SD card slot for additional data storage for program updates. The 750-8212/040-010 has one configurable RS232/485 port, while the 750-8213/040-010 comes equipped with one CANopen port.
Get curated news on YOUR industry.
Enter your email to receive our newsletters.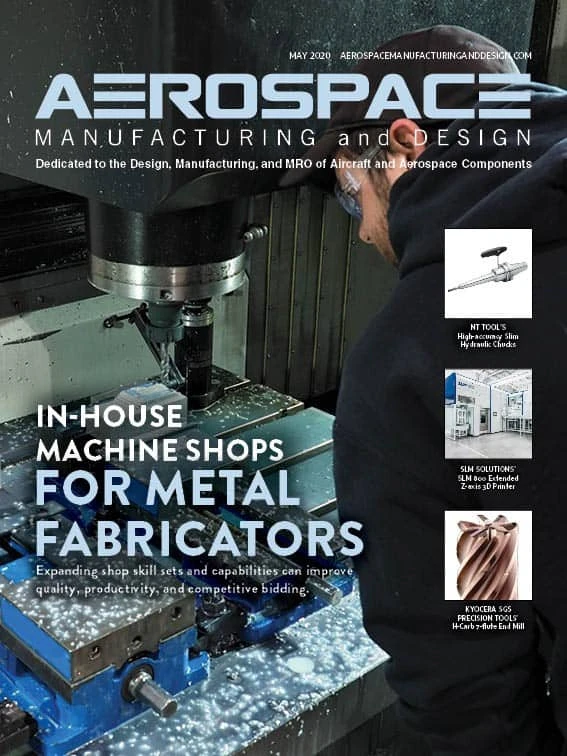
Explore the May 2020 Issue
Check out more from this issue and find your next story to read.
Latest from Aerospace Manufacturing and Design
- AIX shows aircraft interiors are a strategic priority for global airlines
- Machine Tool Builders Roundtable: Turn equipment into expertise
- No time to waste: How to machine MedTech parts more efficiently
- The 5 Best and Fastest Spindle Repair Services
- Mill smarter, not harder: How collaboration optimizes production
- Be proactive – stay ahead of tariffs and other economic and supply chain curveballs!
- Taiwan’s China Airlines orders Boeing 777X passenger, freighter jets
- Reamer re-tipping extends life of legacy tooling