
Another International Manufacturing Technology Show (IMTS) is in the books, and by official reckoning, the 2018 edition set records for attendance, exhibiting companies, number of exhibitor booths, and floor space occupied (see story beginning on page 34).
Additive manufacturing (AM) had expanded space, with a focus on metals in 3D printing, and the themes of Industry 4.0, automation, and digital manufacturing each had a spotlight.
What impressed me most, however, was how pervasive automation has become. It seemed to me that nearly every machine tool exhibitor in McCormick Place had at least one machining center or grinder with a robot above, beside, or within it. Co-bots (collaborative, worker-friendly, low-speed robotic arms that do not require a safety barrier) are gaining acceptance, too, and have potentially more applications around the shop than dedicated, high-speed models. Pallet-loaders, automated tool changers, bar-feeders, and other automation examples were also conspicuous.
Robotics are no longer an afterthought, machine manufacturers have embraced automation as a selling point to increase productivity – unattended manufacturing, improved process reliability, and to make better use of machine and machinists’ time – helping customers meet production ramp-ups.
Most of the machine tool builders note they are authorized automation integrators – reducing the steps needed to get a work cell running in your shop with name-brand robotics – and potentially circumventing third-party robotics integrators. One-party solutions seem to be growing in popularity, I think, because people are now accustomed to ordering from one, all-inclusive source online (Amazon). It’s easy to say the robotics trend will grow, since the number of robots sold in North America in 2017 surpassed all previous records, according to the Robotic Industries Association (RIA), and 2018 will likely exceed those numbers.
Connectivity was another theme present in just about every corner of the show. Machines from different manufacturers around the South exhibit hall were connected, their data streams displayed on a centralized dashboard to demonstrate seamless connectedness, with individual performance metrics immediately available.
While sharing information was a sub-theme, the problems with information sharing was also on many minds, as in: who owns the machine-generated data, how secure is it, and who will digest and analyze the torrent of data that will come not just from machine tools, but the tools themselves, the automation, and measurement devices?
There’s no space here to delve deeply into those answers, but here are a few considerations. At least one industry expert expects specifics on who will own machine data and process information to be part of future contracts throughout the supply chain. Data security is everyone’s responsibility, but shops without extensive information technology (IT) expertise may need outside help. Expect new businesses to spring up that specialize in analytics to manage and make sense of Industrial Internet of Things (IIoT) machine data as a service, similar to what GE Aviation and others are now offering for jet engine condition monitoring. – Eric
Get curated news on YOUR industry.
Enter your email to receive our newsletters.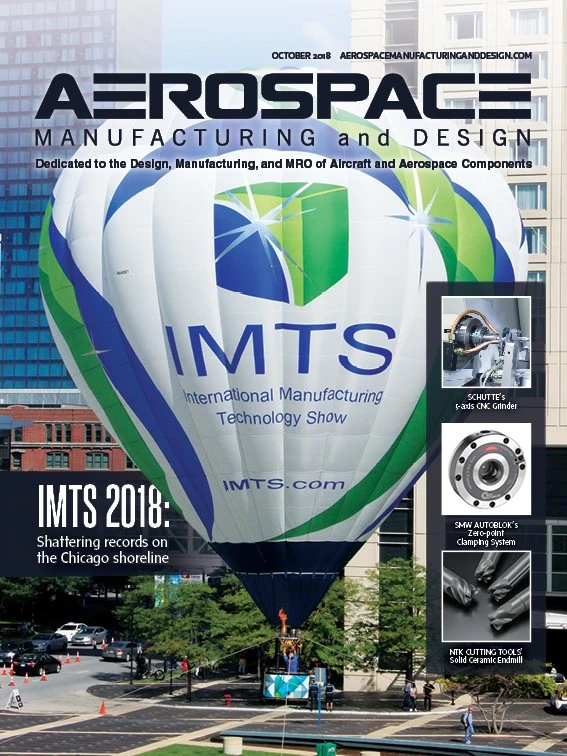
Explore the October 2018 Issue
Check out more from this issue and find your next story to read.
Latest from Aerospace Manufacturing and Design
- NASA offers free high school engineering program this summer
- Pemamak's PEMA Vision 3D software
- Aerospace Industry Outlook - Spring 2025, presented by Richard Aboulafia
- Panama’s National Air and Naval Service selects Embraer Super Tucano
- Model 5770 Linear Abraser
- #42 Lunch + Learn Podcast - Quell Corp
- RECARO Aircraft Seating showcases advanced comfort solutions at AIX 2025
- Mitutoyo America’s MiSTAR 575 Shop Floor CNC CMM