
Part 3 of 3: Part 1 of the Automation for Beginners series in the January-February issue of Aerospace Manufacturing and Design (AM&D) discussed robotics and end-of-arm tooling. Part 2, in the March issue of AM&D discussed material handling and automation in bringing parts into a cell and taking them away after processing, and how this can be the most important and difficult decision to make when designing an automated cell.
Turning centers traditionally have an electrically controlled hydraulic actuator located in the spindle to support different automatic workholding functions. Automatic workholding on a lathe can consist of a chuck, collet, expanding arbor, or be held between centers. It is important to note that when holding parts between centers, the automation/robot may need access to the control of the tailstock quill when loading and unloading.
Since this feature normally needs to be added to most milling machines, the first choice is the power system to control the workholding. The most popular workholding controls are hydraulic, pneumatic, and vacuum.

Hydraulic is a good all-around choice to securely hold most parts but can cost more than the alternatives.
Pneumatics are normally lighter duty and are typically considered when attempting to hold small or delicate parts.
Vacuum, although much less popular, is a good choice when doing thin plate work when it is not clamping on the outside of the blank. It has the ability to offer several different holding options on a single vacuum plate, allowing for little or no setup between several jobs.
Hydraulics
When considering hydraulics, the first question to evaluate is pressure. Typically, it makes sense to use the lowest pressure required. The answer to how much pressure to use lies with the type of hydraulic workholding you are choosing and the clamping pressures required.
There are several hydraulically actuated vises on the market that achieve full clamping pressure at less than 1,000psi. When using fixturing, small swing clamps regularly use pressures from 2,500psi up to 5,000psi to achieve the needed clamping forces.

The next question is the number of hydraulic valves required. Do you have one workholding position or two? In the case of a fixture, is it a single, double, or even triple motion fixture? Each motion of your fixture, or each workholding position, will require its own hydraulic valves.
Pneumatics
When considering pneumatics, traditionally the system will be based around the standard pressure range applied in most manufacturing facilities. An air regulator feeding the workholding valves is used to lower this standard air pressure as needed. Just as with hydraulics, it is important to determine the number of pneumatic valves required to operate the system.

One word of caution regarding pneumatic vices – there are several on the market claiming similar clamping forces as when using hydraulics, but what is not normally made clear is these vises achieve that force at higher than standard shop air pressure. If higher pressure is required, a separate higher-pressure air system is needed to achieve such clamp pressures.
Choices for automatic workholding on a milling machine include vises, chucks, collets, expanding arbors, vacuum plates, and custom fixtures.
Vacuum

When considering vacuum, the first choice is how to create the vacuum. Can a moderate-sized venturi style vacuum generator give you what you need or is a full-fledged separate vacuum pump required? The flow of the vacuum system is what becomes important. On a perfectly smooth part where there is a nice seal, once the vacuum is created, it typically doesn’t leak, so there is no loss of holding power. Many times the part is not perfectly flat or smooth and there is some loss. In this case, a larger pump may be used to overcome the leakage and maintain holding power. A vacuum pressure sensor should always be used to confirm there is full vacuum and in turn, full holding power is present during cutting.
Workholding design
The design of the workholding and how it holds the part in reference to how the automation will hold the part is critical. It is normally desirable for the workholding to hold as much of the part as possible, but some provision will also need to be made to allow the robot to grip the part. For example, when using a three-jaw chuck, a similar looking three-jaw gripper could be used in a slightly different orientation, which will usually allow both the workholding and the grippers to hold the part at the same time. However, when using something such as custom fixtures or swing clamps – which work by starting in a position away from the part, rotate 90° or 180° into position, and then clamp down on the part – allows the automation full access to place the part with no interference from the clamping. Vise jaws may need to be made with slots or notches to allow room for a gripper jaw.

Another design point is a method to automatically clean the fixture as the part is removed. This can include air and/or coolant nozzles directed in key locations that will clean the fixture during the load/unload process. Some users may consider using the robot to clean the workholding, with its ability to articulate around. While this is certainly possible and has been done, it is usually done as a last resort. When using the robot in this manner, you increase the door open time, which increases your takt time. Strategically positioned nozzles, that do the job automatically during the load/unload sequence, don’t add to the time and are a good first choice.
Methods Machine Tools Inc.
About the author: John Lucier is automation manager at Methods Machine Tools Inc. and can be reached at 978.443.5388 x5426 or jlucier@methodsmachine.com.
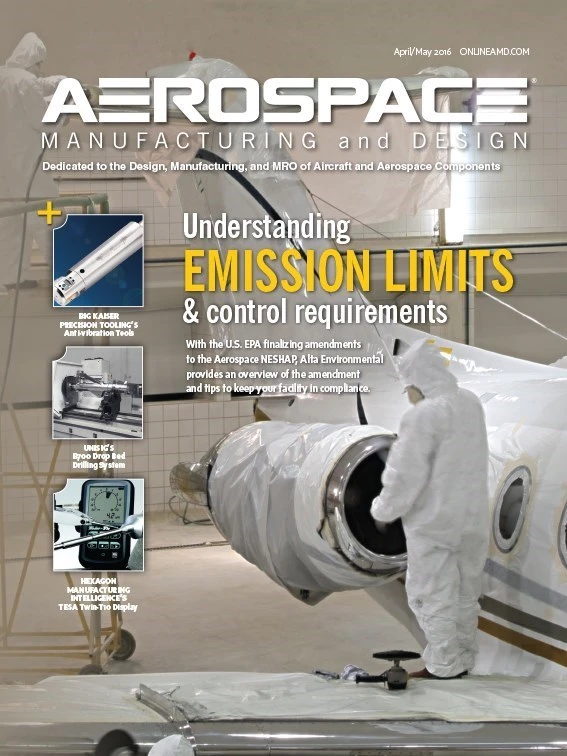
Explore the April May 2016 Issue
Check out more from this issue and find your next story to read.
Latest from Aerospace Manufacturing and Design
- Registration is open for April’s Manufacturing Lunch + Learn!
- Natilus begins search for new home to build world's most efficient commercial aircraft
- Aerospace Industry Outlook webinar is back by popular demand
- Automation Webinar with Visual Components
- PrecisionX Group expands manufacturing operations
- Creaform Metrology Suite expands capacities
- United Performance Metals acquires Fabrisonic
- OES’ 30mm vertical lift stage