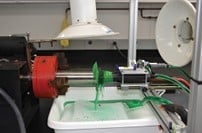
Customized automated solutions for plating titanium offer customers a consistent, repeatable means of enhancing titanium alloys for use in mission-critical components.
Despite its high strength and light weight, titanium’s poor resistance to abrasive or adhesive wear makes it unsuitable for many uses, for example, aircraft landing gear. This can be overcome by plating the titanium, which improves lubricity, corrosion resistance, conductivity, heat reflection, and emissivity. Unfortunately, titanium is difficult to plate because an oxide film forms once it’s exposed to oxygen. Existing plating techniques are highly corrosive, potentially poisonous, or short-lived in their effectiveness.
Extensive experiments with Ti-6Al-4V and Ti 6-6-2, two widely used titanium alloys, helped perfect more efficient plating. The resulting process includes surface pre-treatments of mechanical finishing, followed by an etch, activation, and a thin nickel layer. The approach offers selective plating’s benefits with enhanced component quality.
Automated plating systems avoid oxidization by making the electrolyte solution flow over the component continuously. Automation combines selective plating’s ease and convenience, and introduces benefits in quality, repeatability, traceability, data logging, productivity, and user safety.
The automated system uses a portable TechnoPlate – a programmable power pack that allows repairs to be plated in situ and stores the volts, amperage, and ampere hours, reducing human error.
The titanium plating is offered as a contract service on-site at a customer’s premises or at a job shop.
SIFCO ASC
More information on automating titanium plating: https://www.sifcoasc.com/automated-plating-systems
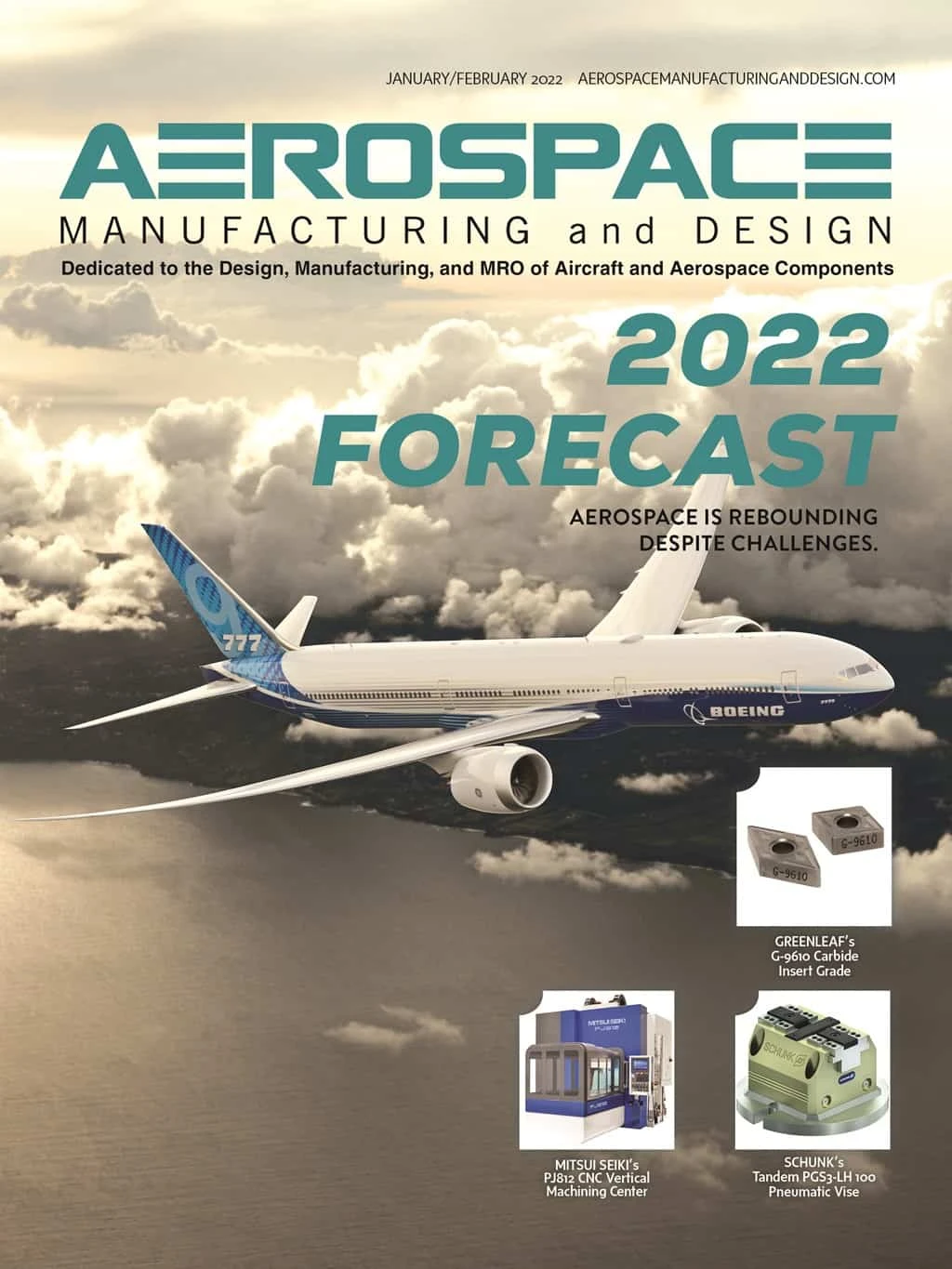
Explore the January February 2022 Issue
Check out more from this issue and find your next story to read.
Latest from Aerospace Manufacturing and Design
- Safran Defense & Space opens US defense HQ
- Two miniature absolute encoders join US Digital’s lineup
- Lockheed Martin completes Orion for Artemis II
- Cylinder CMMs for complex symmetrical workpieces
- University of Oklahoma research fuels UAS development
- Motorized vision measuring system
- Everyone's talking tariffs
- Boom Supersonic to launch Symphony engine testing in Colorado