
Very few companies have survived two World Wars, the evolution of mass transportation, and the mind-bending technology revolution of the past 30 years. With aviation in its DNA, Hartzell Propeller Inc. has produced high quality aircraft propellers in Piqua, Ohio, for nearly 100 years. There are generations of flyers loyal to the brand. In 1920, “Built on Honor” was added to the product label and remains on every Hartzell propeller today. Their longevity can be attributed to the relentless, competitive spirit and trail-blazing mentality of the Hartzell family founders and those following in their footsteps.
“Done in One” is Hartzell’s philosophy. At first glance, the company’s shop floor reveals meticulous attention to detail and organization, and a closer look reveals a factory lifestyle built upon automation and a quest to eke out manufacturing process efficiencies. Producing parts right the first time – in-spec, on-time, and scrap free – is Job One.
Growing with automation
Hartzell manufactures more than 3,000 propellers per year, which is 10,000 to 12,000 propeller blades. However, blades are only one facet of the business. More than 100 different parts go into a propeller system, and 85% of those components are produced in-house. Technology and cellular manufacturing have enabled the company to grow its brand footprint globally, substantially expanding the number of parts produced internally.
Collaboration with leading technology providers has resulted in an astonishing amount of customization not found anywhere else in the world. Hartzell’s operations department works with a top “robot whisperer,” an expert who programs and integrates robots into the automation cells. The company’s role in advanced manufacturing is more than applying technology, it’s in inventing new processes to boost efficiency and productivity. Others in the industrial sector have taken notice of Hartzell’s best-in-class facility, as the company has given more than 70 tours to visiting manufacturers.
“We don’t use technology to outsource a job for a robot or to automate our way out of manpower. We use technology, robotics, and automation to integrate ourselves into a work cell to bring more products in-house that we can make at a lower cost, on-time, with better quality than our competitors,” states J.J. Frigge, executive vice president at Hartzell Propeller.

Adding metrology to automation
Automation with metrology completes Hartzell’s total concept of a cellular manufacturing environment – raw material is delivered to a cell, travels through different operations on a variety of machines until it is a finished part, and part-in-progress is checked by a coordinate measurement machine (CMM) after every operation. Each component is consistently verified throughout the production process, and the final inspection occurs on the CMM within the cell as the component is ready to go to stock. Hartzell is certainly no stranger to metrology with 19 CMMs from Hexagon Manufacturing Intelligence, North Kingstown, Rhode Island, in use throughout the factory.
WATCH NOW – Hartzell Propeller Inc. executives talk about the company and its use of advanced technology – CMMs, robotics, automation – which allow them to manufacture high-quality products in the U.S. See how metrology automation really plays a large role in their quality production.
For its newest automated work cell, Hartzell selected a 7.10.7 SF from Hexagon Manufacturing Intelligence as they needed a CMM with a work envelope large enough to check two parts at the same time. The measurement system also provided a robotic interface to integrate into Hartzell’s automated system. The cell is used to manufacture different runs of parts such as composite blade shanks, slip ring bases, and pre-load plates for aluminum blades. The CMM is holding tolerances of ±0.00015", and supporting the cell’s overall tolerance at ±0.00250".
The 7.10.7 SF is a shop floor CMM that was designed for demanding environments such as manufacturing cells. In the cell’s footprint, the CMM runs inspection routines next to a robot, a CNC mill, and additional machines. The system incorporates built-in vibration resistance, advanced thermal compensation, and covered guideways to allow accurate measurements while surrounded by constant production activities.
Run a part, check a part
The integration of CMM technology in the past five years has been a game-changer for quality, enabling Hartzell to “run a part, check a part.” This operational principle has eliminated large group scrap incidents. With real time data fine-tuning speeds and feeds on the machine, on-the-fly adjustments for dulling tools or variations in raw materials can be made to hold a part within tolerance. This approach also streamlines the process flow through the shop, allowing employees to efficiently build individual parts and families without waiting on pieces farther down the assembly line.

“Behavioral scientists will tell you that 100% inspection by humans is only about 78% effective. It is true. People get tired, get distracted, or are performing several tasks at once. With CMMs, there is no interference from human beings once it is programmed properly. So we get good data once, and we can trust it,” says Ralph Schieltz, senior quality engineer. “And with automation, an operator is free to run two or three machines instead of performing manual inspection.”
Automated operations
Typically, rolling carts are loaded with raw materials and delivered to the cell. For a pre-load part, Hartzell uses a robot equipped with a camera to check the orientation of the part, rotate it to the proper angle, and feed it into a CNC machine. The part is machined on the main spindle, then passed on to the sub-spindle for more machining. The robot unloads the part from the CNC, washes and dries it in a separate unit, and places it on the CMM for inspection. After measurement, the robot retrieves the part, transports it to a marking station for pen stamping with a part and revision number, and places it on the cart where it was originally picked up.
Three parts can be running simultaneously. The first part coming out of the cellular production is critical due to the parts following behind it. The CMM will halt the cell if it detects a bad part. Hartzell uses advanced software to chart part-by-part, dimension-by-dimension, coming off the CMM. The cell is monitored 24/7 and feeds real-time data so the operations staff can always tell if a cell is running.
“Automation takes out the human factor, the human intervention that could cause machine wrecks, bad parts, or bad offset changes,” states Todd Bair, Hartzell manufacturing services. “And part quality is inherently better with automation due to repeatability. Because there is no lifting of heavy parts, as that is work is conducted by robots, ergonomics and safety is better for our workers.”
Cells in progress
Hartzell’s newest manufacturing cells have the ability to run lights out, 24/7. A notification program sends a text alert to the operation staff if any part comes out of tolerance, if a machine is adjusting on its own to hold tolerance on the next part, or if a machine needs approval to shut down or continue running. The company’s newest cell has been running part-time and unmanned for about four months and will be fully operational this year.

“It has been really exciting to see the metrology piece evolve so quickly and completely through our shop. We have been on a 20-year-plus journey around productivity,” Frigge reflects. “During that time, we have increased our efficiency and production rates by more than 25%. The CMM technology has been the pivotal piece from a game-changer viewpoint, enabling us to make a part in a cell on a 7-axis CNC machine and perform inspection right in the cell. We have real-time data telling us if we are in spec or not, and whether we have a high quality part coming off the machine – one at a time.”
Done in one
“Hartzell has flipped the equation on companies who are outsourcing to China. Done-in-one means making a part where it is most efficient. We are putting the right parts in the right cells with the right equipment, while optimizing our cost structure and machine times. Automation is our roadmap to bringing more parts in-house and increasing manufacturing capacity, so we continue to grow steadily as a company,” Frigge concludes.
Hexagon Manufacturing Intelligence
Hartzell Propeller Inc.
Get curated news on YOUR industry.
Enter your email to receive our newsletters.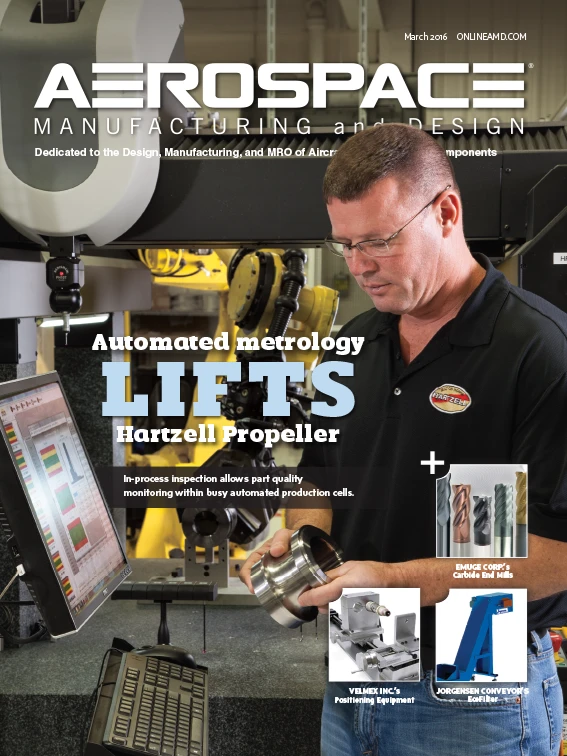
Explore the March 2016 Issue
Check out more from this issue and find your next story to read.
Latest from Aerospace Manufacturing and Design
- Heart Aerospace relocates to Los Angeles
- Fixtureworks introduces Stablelock Clamps
- Piasecki acquires Kaman's KARGO UAV program
- PI Americas’ long-travel XY piezo nanopositioners-scanners
- AAMI project call submission deadline extended to May 12
- Jergens launches cast iron tooling column additions
- Airbus to acquire assets relating to its aircraft production from Spirit AeroSystems
- FANUC America's Cobot and Go web tool