
With aerospace markets slowly returning to full-capacity production, job and machine shops now must prepare for short-, medium-, or high-volume production of multi-size fasteners and fittings. They need machines that integrate with their current production, offering added flexibility for fast tooling and workholding changeovers.
How are job/machine shops preparing?
Andrew Lilly (AL): Visit some aerospace machine shops and you’ll see floors full of machines 50+ years old. Our solution can replace multiple machines in a much smaller package.
Troy Kattenhorn (TK): Often, only a handful of operators can run those legacy machines. Our equipment, with the latest CNC controls, allows new operators or higher-level operators to run those machines.
Why is workholding and tooling changeover flexibility so important?
AL: Some machines can only do one job. That’s not a lot of flexibility, so you need many of them to do many different jobs. Our MW35 machine offers that flexibility.
TK: It’s fully enclosed, safe, clean, keeps the oil mist down, and it’s fully electric. There are no hydraulics or mechanical cams, belts, or pulleys. A customer can make offset changes mid cycle. It reduces setup time from 4 to 8 hours down to 20 to 30 minutes. Some customers like to use a three-jaw chuck, while others like a collet chuck, and we can use either.
What’s turnkey, integrated automation and why is it important?
AL: Our new feed system can accommodate a wide range of part sizes, giving customers a machine that can tackle multiple families of parts on one machine. We can do that with very short cycle times and very little changeover.
TK: Our turnkeys make us a one-stop solution. We take care of the complete package, seamless integration, with little risk. With active automation monitoring, the machine and the robotics monitor each other’s movements so they know exactly where each one is at all times.
What Muratec machines are for aerospace markets?
TK: All of our machines have strong potential in aerospace sectors.
AL: The MW35 is enhanced with a pick & place loader that automates part feeding, allowing an operator to quickly load a batch of raw fastener material to keep the machine running continuously. Typically, adding automation is going to make your footprint much larger because it sits beside or in front of the existing machine but our loader fits within the MW35’s footprint.
With speed-to-market so important today, how does Muratec help customers?
TK: Because we do all our own automation in house, we’re not reliant on third-party supply chain issues. We have multiple MW35 machines in stock, ready for integration and shipment.
AL: The machine’s simplicity allows multiple operators to learn it quickly. With intuitive controls, it’s designed for a single operator to control multiple machines.
For more information: https://www.muratec-usa.com/machinery/turning/twin-spindle-machines/mw35/
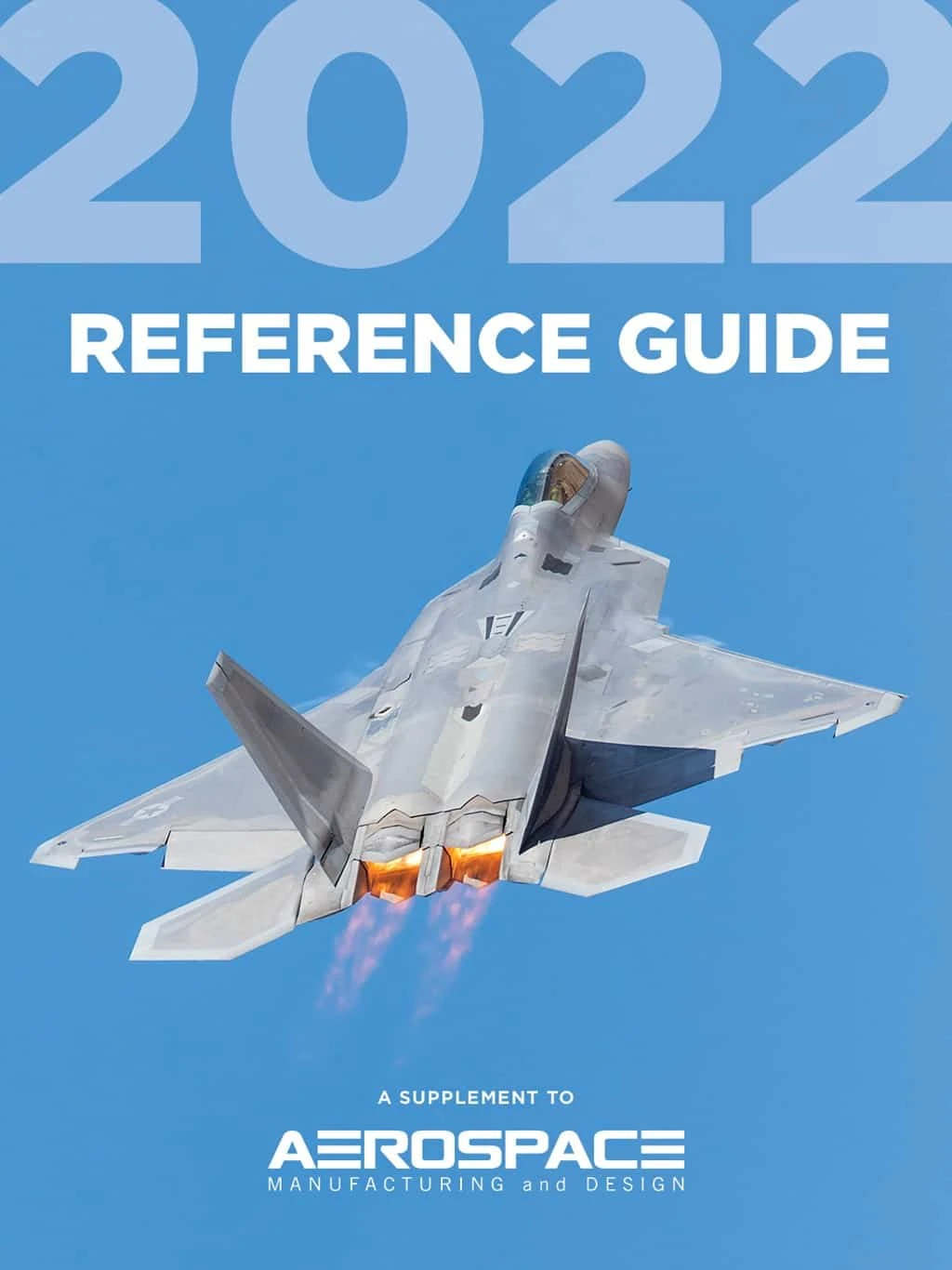
Explore the AMD Reference Guide 2022 Issue
Check out more from this issue and find your next story to read.
Latest from Aerospace Manufacturing and Design
- AAMI project call submission deadline extended to May 12
- Jergens launches cast iron tooling column additions
- Airbus to acquire assets relating to its aircraft production from Spirit AeroSystems
- FANUC America's Cobot and Go web tool
- Chicago Innovation Days 2025: Shaping the future of manufacturing
- High-density DC/DC converters for mission-critical applications
- #59 - Manufacturing Matters: Additive manufacturing trends, innovations
- ACE at 150: A legacy of innovation and industry leadership