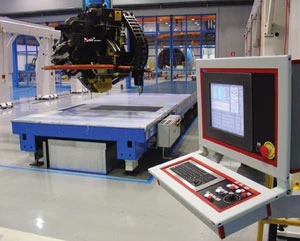
Make room, metalworking. The automated composites processing revolution continues maturing as a core manufacturing technology. What started out decades ago as a cut and place handwork process can now be automated to create nearly any component shape. Advanced mechanical design and sophisticated, yet user-friendly multi-axis CNC controls enable cost-effective volume production of high-precision components offering performance gains and problem solving solutions. Composites provide answers to weight and fuel savings, superior dynamic performance, greater space utilization, corrosion issues, reduced maintenance and longer operating life, and time- and labor-saving monolithic alternatives to complex part assemblies. These powerful drivers fuel the revolution.
Last year delivered a record year in composite machinery bookings and early 2008 results are continuing the rising trend line. Sports applications (golf, tennis, skiing, and fishing) long dominated in material usage, but are being surpassed by the composites usage in aircraft construction. The availability of pc-based, production-proven automated production systems are starting to expand in other industry sectors, including energy, automotive and construction.
Over recent years composites became the dominant material for new commercial airliners, matching the earlier transition of military aircraft to composite construction. Boeing's new 787 Dreamliner, already in build, is 50% composites by weight and 80% by volume with industry's first composite airframe - fuselage and wings. Airbus raises the bar to 52% composite construction for its competitor design, the A350XWB, scheduled to start fleet delivery in 2012.
While performance and stealth advantages drove the initial adoption of composites for military aircraft, the conversion with commercial airliners is being driven by manufacturability, maintainability, efficiency and comfort advantages. The old way of assembling an aircraft from thousands of aluminum parts and millions of rivets is being replaced by the joining of large, prefabricated composite fuselage, wing and tail structures. Structures can be produced by automated, CNC lay-up machines, rather than joined piece-by-piece by armies of assemblers - the number of components that need to be engineered, manufactured, ordered, tracked, handled, stocked, etc. decreases exponentially. On the performance side, composites make aircraft lighter, more efficient to operate, and less prone to fatigue, while enabling selective engineering of performance characteristics. Boeing says the 787's composite construction offers almost 20% weight savings over an aluminum structure for higher speed, greater range and fuel efficiency, while reducing wall thickness for greater interior cabin space.
Bookings for the two composite airliners demand a rapid ramp-up in composite production capacity that is radically remaking the aircraft manufacturing infrastructure and alliances. Tier One manufacturing partners in the U.S., Italy, and Japan are fabricating large, monolithic airframe components that are shipped to Boeing's Everett, WA, plant for assembly and joining. On the military side of the industry, Turkey joined the advanced composites club, ordering a VIPER Fiber Placement Systems (FPS) from MAG Cincinnati for Joint Strike Fighter construction. Last year also marked another migration of automated composites systems to Tier 2 suppliers, with the purchase by Los Angeles, CA-based HITCO of both a VIPER FPS for automated fabrication of highly contoured and enclosed structures and a CHARGER tape-layer system for production of more linear, less contoured components. To meet the industry's volume and geographic growth, makers of composite materials are rapidly adding capacity and new locations.
Just to meet bookings for the 787 and A350, aerospace composites capacity needs to increase by several magnitudes over the next five to 10 years. Beyond those two massive programs, regional jet design should follow the composite model. Business jets have already begun the conversion to composites, led by Hawker Beechcraft with the eight-passenger Premier I and larger Hawker 4000, each with fuselages fabricated on Cincinnati VIPER FPS systems. Helicopters use composite construction for rotor blades, but composite airframe structures would give weight savings and load improvements. Offering exciting growth potential is very light jets - small, affordable (under $1 million) aircraft suitable for personal jets or jet taxis. All of this growth is reliant on low risk manufacturing partners, production-proven equipment in a variety of platforms, and applications support.

The Viper FPS system combines the advantages of tape laying and filament winding with advanced computer control and software.
Less predictable is the pace of composites adoption in other industries. However, the availability of proven composites production systems and manufacturing technologies, vetted by the aerospace industry, reduces the risks, complications, and transition costs for other industries. The power generation/wind energy market is a prime application of composites for huge turbine blades. However, rising oil costs and fuel efficiency standards are driving vehicle designers to seek significant weight savings, which composites can provide. Large components such as hoods and firewalls can yield impressive weight reductions. Fuel cell vehicles, which change the design/manufacturing paradigm, are opening opportunities for composites - anywhere from the fuel cell structure to a rigid, high-strength, lightweight chassis platform.
While converting parts and components from metal to composite provides incremental weight savings, the big pay-off can come in rethinking vehicle design around composites. This can make possible part reduction and manufacturability advantages, savings on the huge capital costs for stamping presses and dies, and enable shorter model runs and fast-changeover flexible production. Large vehicles seem especially suited to monolithic composite construction methods. Reducing platform weight for military vehicles could allow greater armoring with less degrading of vehicle responsiveness. In space systems, where every ounce of payload is critical, certain components for satellite vehicles, for example, are being converted to composites.
One Source.
As a supplier of automated composites lamination systems, MAG Cincinnati has supplied more than 50% of all existing composites machines worldwide. Work with companies as they entered into automated lay-up - Boeing, Airbus, Hawker Beechcraft, Bell Helicopter, and more, now considered leaders in this field - has lead to current engagements with several companies that are planning ahead for the next wave of composite structures and components.

Charger Series Tape Layers offer low rail gantry platforms and new generation contour tape heads.
Offering a range of automated composites machines and processing systems as well as applications expertise, enables users to achieve vital standardization in manufacturing operations and state-of-art precision and production efficiencies for whatever the required part shape. Also, as a manufacturer of machine tools, MAG Cincinnati can offer advice on the integration of and/or transition between machining and composites equipment. Finally, addressing the industry needs to bring higher efficiencies and levels of automation to composites manufacturing, product development is being accelerated - allowing users to more closely tailor equipment to part shapes and sizes - where each composite lamination system is specifically engineered for best-in-class processing.

Explore the May June 2008 Issue
Check out more from this issue and find your next story to read.
Latest from Aerospace Manufacturing and Design
- 2024 Favorites: #5 Article – Solving workforce issues with digital transformation
- 2024 Favorites: #5 News – GE Aerospace is investing in manufacturing
- 2024 Favorites: #6 Article – Mastering complex precision machined parts
- 2024 Favorites: #6 News – Boeing to acquire Spirit AeroSystems in $8.3B deal
- Season's greetings
- 2024 Favorites: #7 Article – Deep drawing aerospace components
- 2024 Favorites: #7 News – GKN Aerospace completes sale of St. Louis facility to Boeing
- 2024 Favorites: #8 Article – Beyond uptime