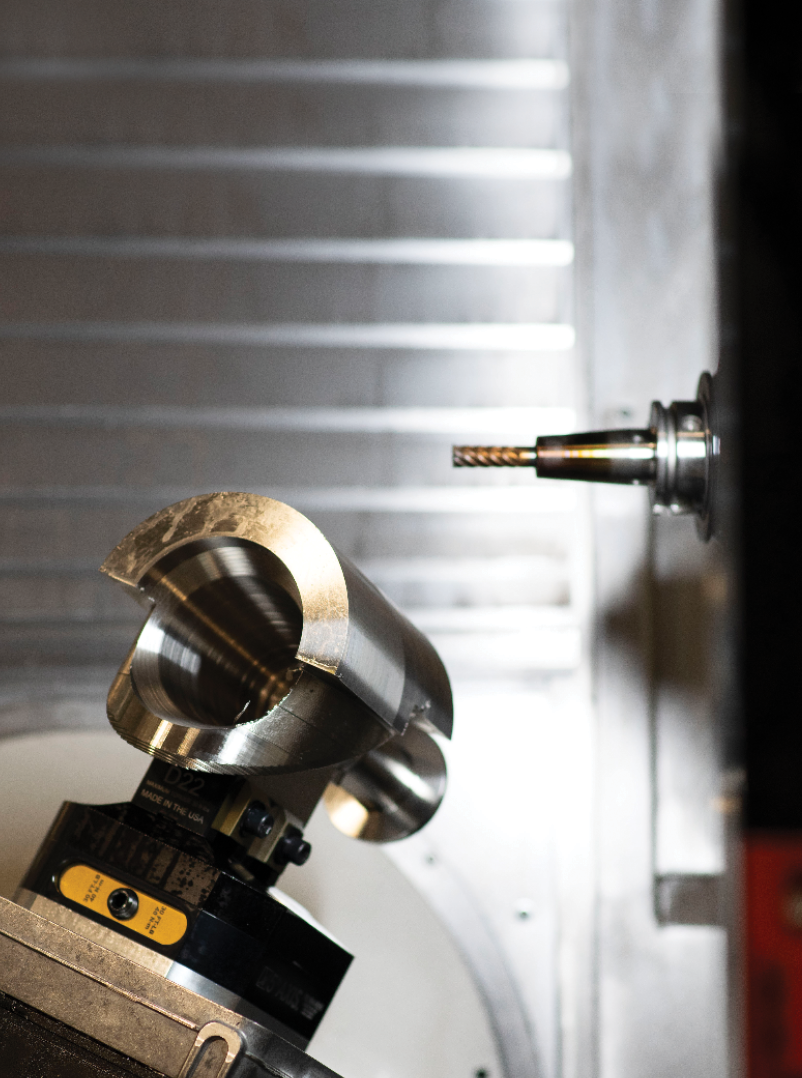
A young, entrepreneurial company offering advanced manufacturing services now confidently makes large aerospace parts running unattended operations after installing two GROB G350 5-axis universal machining centers, integrated with a custom automation cell. The machines produce larger parts than was previously possible, and the automation and additional process reliability frees time for additional production hours.
Rennscot MFG has another key foundational element providing them with unique perspective and benefits. “We like to highlight our youthfulness – both the age of the company and our employees,” says Tommy Gentilucci, VP of Operations and Rennscot MFG co-founder. “David and I are in our late 20s, and we find that helps us in adopting new technologies and strategies,” Gentilucci explains. He also believes the youth factor helps attract younger talent in an industry facing labor and recruiting challenges.
Embracing manufacturing challenges
An innovator not afraid to adopt new technologies, the biggest challenge Rennscot MFG encounters is constantly evolving projects having a range of different requirements. Gentilucci says, “As a new company, we’re building our customer base and most project work is new, so we need machine tools that are efficient, easy to work with, and capable of machining difficult features accurately the first time, as well as quickly meeting tight delivery timelines.”
In 2022, Rennscot MFG began considering new automated machining options as well as a solution to provide high process reliability in long cycle time parts, including overnight runs. Gentilucci adds, “We wanted to confidently machine large parts in one setup, without interruption.” Gentilucci and Bamforth gained a general awareness and understanding of GROB capabilities and liked the value they saw, so they reached out to a representative to learn more about GROB’s technology. By the beginning of 2023, Rennscot MFG procured two GROB G350 5-axis universal machining centers together with an automation cell. Bamforth says, “We always knew we’d end up with GROB someday – the dynamic nature of these machines combined with their rigidity and reliability were ideal to support the kind of work we are doing and plan to do.”
The high-precision, versatile G350 has a compact design providing high visibility-optimized work area access. Three linear and two rotary axes provide operators with 5-axis simultaneous machining and interpolation, with a swivel range of 230° in the A-axis and infinite rotation in the B-axis. The unique arrangement of the three linear axes minimizes the distance between the guides and the machining point (TCP), providing exceptional rigidity. Also, a unique spindle tunnel concept provides access to the workpiece and upside-down machining in a collision-free environment, ensuring the longest possible Z-travel path and optimum chip evacuation.
Tool changes occur outside the work area, which eliminates chip interference. Additionally, a tool brush cleans the tool shank prior to the tool being inserted into the spindle and a coolant flushing system pushes chips out of the work area and through a conveyor. Featuring a 117-tool holding capacity and an HSK-A63 tool interface, the GROB G350s at Rennscot MFG have Heidenhain iTNC 640 controls.
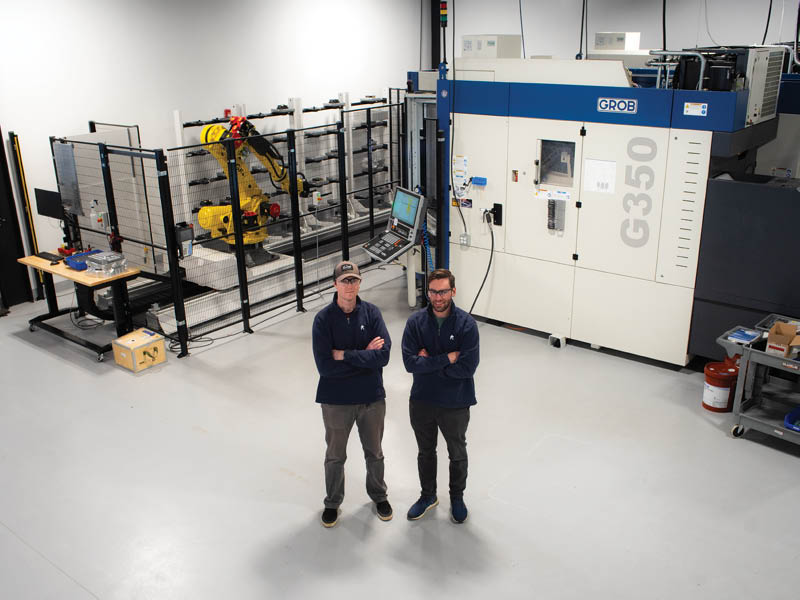
Service and support
The pre-install experience with GROB was better than any other Rennscot MFG has experienced. “GROB provided thorough documentation that set us up for success on delivery day,” Bamforth says. “The install procedure was seamless thanks to the machine being shipped, picked, and installed essentially pre-assembled – something that isn’t the case with other machines in the same tier which can be comprised of many different sub-assemblies that can take days to assemble and align.”
Automation boosts productivity
The multi-axis GROB machines are eliminating secondary machining operations for Rennscot MFG, and the automation capabilities are key. Gentilucci says, “For optimal productivity, we currently only operate one shift during the day and rely on our machines, automation systems, and programming/machining strategies to enable unattended runtime through the night and weekends.”
Rennscot MFG reports the GROB machines are helping them optimize process reliability in long runs including those going overnight. “Chip evacuation thanks to the horizontal spindle configuration, great coolant filtration due to the well-integrated paper band filter, and other small features give us the confidence to leave these machines unattended for 24+ hours at a time,” Gentilucci notes. “The efficient chip evacuation the GROB machines offer isn’t available with our other machines. If we were trying to run some of the larger parts on any other machine than GROB, we’d need to stop production just to clean up chips.” Also, the custom 40-pallet automation cell has increased productivity up to 50%, enabling much longer unattended part runs.
Automotive to aerospace parts production
The first application to test the new GROB machines and automation setup produced automotive transmission bellhousings. These components had several challenges ranging from their large raw stock size at approximately 20" x 20" x 10" to a finished design that needed to be optimized for a forging process featuring minimal perpendicular surfaces and tight tolerances. For example, some bores on the bellhousing have a total tolerance band of 10μm in diameter.
The GROB machines performed exceptionally well due to the spindle’s tunnel configuration, enabling the longest tool (which was roughly 9" long) to be held without any concerns of interference during tool changes. Also, the horizontal machine configuration provided exceptional process reliability especially with the significant amount of material that had to be removed. For its part, the integrated automation cell allowed Rennscot MFG to schedule the roughing operation to run for more than 10 hours, throughout nights and weekends. The cell also made it much easier for the manufacturing engineers to move parts in and out of the machine.
After this success, Rennscot MFG was confident they could use the automated GROB solution for aerospace parts manufacturing, a growing market for the company. Gentilucci says, “We were tasked with manufacturing a handful of large, aluminum flexure rings for a satellite application. These parts were large at just over 24" diameter, and featured a series of complicated, thin features in 36 different orientations.”
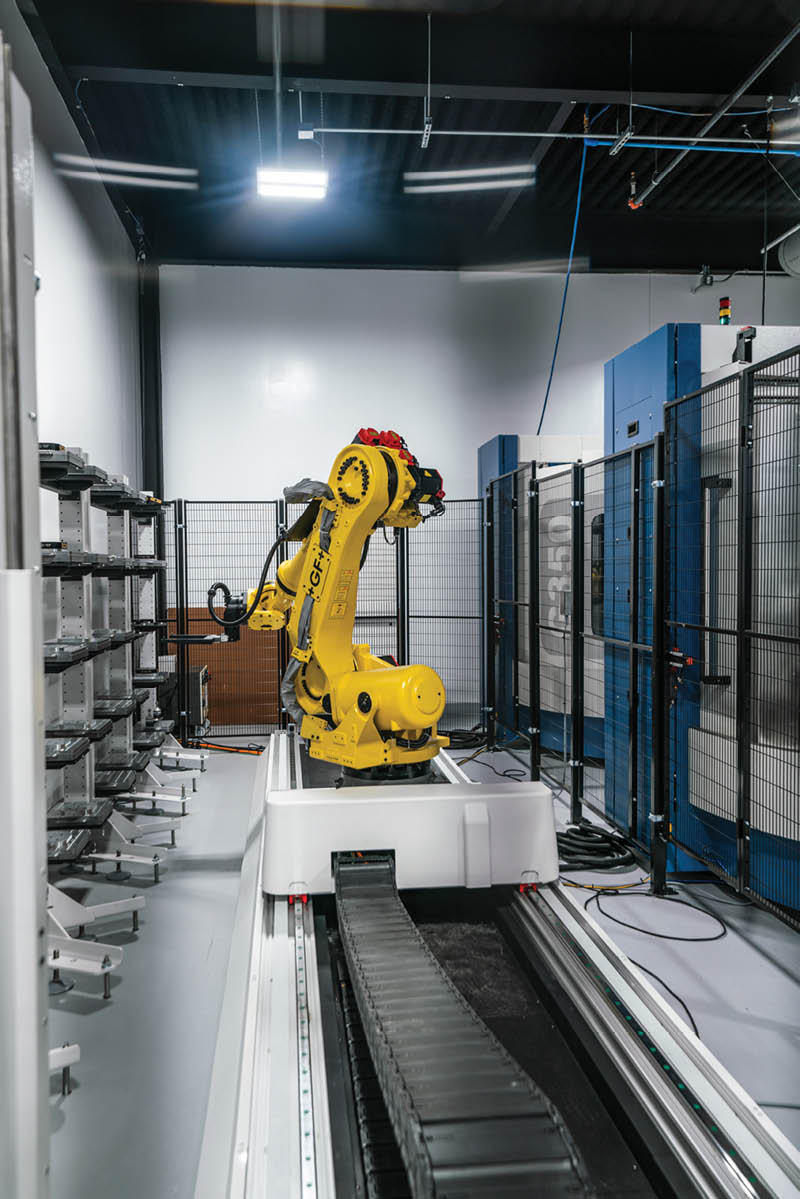
The GROBs were the only machines in Rennscot MFG’s shop large enough to handle these parts. The multi-axis machining capabilities were also a requirement for this job because many of the external features required continuous surfacing with a ball mill.
With the satellite part application success, Rennscot MFG took on manufacturing a series of spacecraft reaction control system nozzles. The stainless-steel parts are relatively large at more than 10" in length. Most of the part’s dimensional characteristics are controlled by a complex 3D profile of a surface callout, inspected with a laser scan. The rigidity and dynamics of the GROB machines facilitate ideal final milling operations on these parts, primarily comprised of simultaneous ball mill toolpaths. The automation cell allowed the roughing toolpaths to be run overnight, freeing up time during the day for monitoring more critical machining operations.
3D and beyond
In addition to those applications, Rennscot MFG expects the GROB machines to be key for post-machining additively manufactured parts. “We currently offer metal 3D printing in house and the post-machining of these parts typically comes with new challenges in the form of weird geometries, thin walls, and tight tolerances,” Gentilucci says. Advanced probing routines are also necessary to ensure proper part alignment and location.
Rennscot MFG also anticipates the rigid, fast, and reliable GROB machines will become the go-to for larger aluminum structural components requiring tremendous material removal. Gentilucci concludes, “We’re hoping to continue learning about different ways the GROB machines can make our jobs easier for taking on new projects, especially for aerospace. The Heidenhain control on the GROB machines offers great motion control for the complicated parts we are seeing increasing demand for.”
GROB Systems Inc.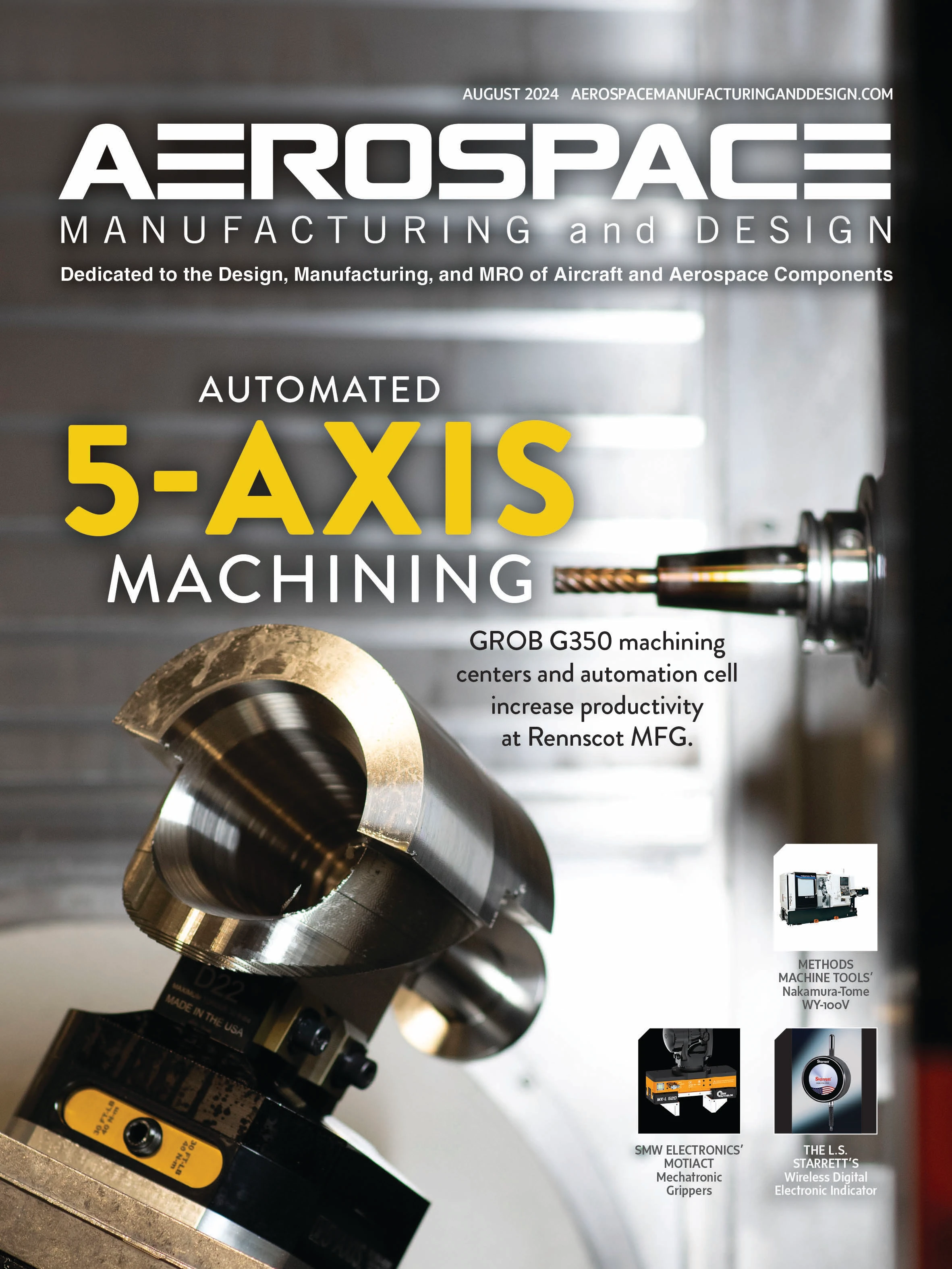
Explore the August 2024 Issue
Check out more from this issue and find your next story to read.
Latest from Aerospace Manufacturing and Design
- The Partner Companies acquires Precision Eforming
- Hall Effect angle sensors
- July is for learning – so drop in for this month’s second Manufacturing Lunch + Learn
- Essential strategies to protect your data
- NASA selects instruments for Artemis lunar terrain vehicle
- Twin-cutter boring head
- Bell awarded funding for X-plane build phase of SPRINT program
- Shaft coupling clamps