![]() |
For many years, all types of aircraft component manufacturers used vacuum furnaces. In the early 1970s, major engine manufacturers realized the advantages of vacuum processing and began equipping their plants with furnaces for the heat-treating and brazing of engine components. Not long after, airline engine repair facilities followed suit. Eventually, airframe manufacturers also jumped on this trend to cleanly heat treat raw materials and braze finished products.
Components currently being vacuum processed range from simple parts, to large aircraft body sections and landing gear assemblies. Often, these larger parts require a specially designed furnace to accommodate their large size and unique heat treating requirements.
Today, the trend for airframe manufacturers is the increased use of composite materials and titanium alloys. Compared to an aluminum structure, these composites provide a greater reduction in maintenance due to fatigue. When loading and environmental factors are analyzed, low maintenance, high strength titanium trumps aluminum again.
Due to the benefits of titanium, it now represents approximately 15% of the total airframe in the new Boeing 787 Dreamliner. For example, the majority of the heat treatable titanium in the Boeing 787 is in its landing gear and structural fittings (Ti5553), floor structure (Ti-6Al-4v), extrusions (Ti-6Al-4V), and nacelles (Ti-6Al-4V).
Although Ti-6Al-4V has been the most used alloy of the industry, Ti5553 (Ti5Al-5V-5Mo-3Cr0) is also being used on key flight-critical parts in the 787 aircraft. When compared to Ti-6Al-4V, Ti5553 exhibits excellent hardenability characteristics while combining superior strength with high fracture toughness and excellent high cycle fatigue behavior. This is why Ti5553 forgings are used in loaded locations such as flap tracks, pylon, side body chords, and landing gear applications.
![]() |
Specifications Needed
Striving to help advance the use of these titanium alloys in the aerospace industry, through successful heat treating and processing, is Solar Atmosphere. Without the proper methodology, attaining specific critical metallurgical properties is not possible, parts become faulty and costs rise. Unfortunately, a universal specification that covers all necessary aspects of the process and the desired end results does not yet exist. Only various specifications covering wrought mill products (AMS4928Q), titanium parts (AMS2901B), and other in-house procedures (BAC5613) are currently in place. There is definitely need for the industry to quickly produce an acceptable specification for vacuum heat treating.
For example, Ti-6Al-4v involves a solution treatment followed by fast cooling – usually water quenching. However, this often results in excessive distortion, which is unacceptable to the aeronautical engineer. This challenge has resulted in the expanded use of the newer alloy – Ti5553, which can be control-cooled with minimal distortion allowing for design to near net shapes. The BASCA (beta anneal slow cool age) heat treatment of Ti5553 allows for much better ultimate properties and controlled distortion.
Suggested Specifications
Recommendations by engineers at Solar Atmosphere are to address the following issues in any future titanium processing specification:
- Description of the proper cooling rate required for a particular material or part – Whether it is with water, oil, or inert gas, rates must be established to achieve necessary properties and minimize distortion
- Outline more recently proposed preparation techniques and newly developed processing cycles – Current titanium specifications assume subsequent thermal processing will produce an oxygen rich layer of alpha case, however, this case can be greatly minimized using vacuum technology
- State maximum allowable PPM levels of hydrogen to eliminate possible embrittlement and risk of failure of the material – Severe problems can arise when titanium alloys come into contact with hydrogen rich environments, usually occurring during manufacturing and processing of the material, especially at higher temperatures; Deep vacuum processing along with elevated temperatures depletes this hydrogen down to single digit parts per million levels
- Acknowledge that graphite can be used for fixturing in vacuum processing – Graphite fixtures enable the engineer to design to nearer net-shaped components
- Ensure the values of both the work and the control thermocouples are recorded and reported – Current specifications do not clearly define and differentiate between them
Future Success
It is projected that the world fleet of aircraft will double by the year 2029. Airframes will certainly increase in their use of composites and titanium. Current Boeing/Airbus usage of titanium is 60 million pounds per year, with a projected increase to 100 million pounds by 2012. In order to properly meet the increasing need to thermally-process this material, it is essential that metallurgists from all aspects of the aircraft industry sit down to successfully create a universal specification for titanium vacuum processing. This collaborative achievement will not only enhance the use of these materials, worldwide, but will also increase the quality and safety level in the military and the commercial aerospace industry.
Solar Atmospheres Hermitage, PA
solaratm.com
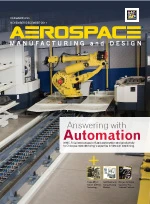
Explore the November December 2011 Issue
Check out more from this issue and find your next story to read.
Latest from Aerospace Manufacturing and Design
- Beyond Aero refines its hydrogen-electric light jet
- Americase's advanced protective solutions
- Social media - what are your thoughts
- GE Aerospace secures Air Force engine contract
- Thomson Industries' online sizing and selection tool
- #53 - Manufacturing Matters - 2024 Leaders in Manufacturing Roundtable
- Join us for insights on one of the hottest topics in manufacturing!
- You can still register for March’s Manufacturing Lunch + Learn!