The crème de la crème of the titanium-processing industry encounters enormous challenges when it comes to the optimal serial processing of this delicate material. Increasing implementation of titanium in the aerospace industry is due to the advantages gleaned from its stability and relatively low weight. Supporting titanium structural parts used in conjunction with modern composite materials are how everything from wide-body jets and spacecraft to dynamic fighter jets will be built in the future. In terms of turbines, blades made out of titanium, which can also combine with composite materials, are currently at the forefront of technology.
Material is User-Friendly, Production-Unfriendly
It is a well-known fact that titanium is a very tough material to machine, since its toughness and low thermal conductivity are incredibly tough on the cutting edge of the tools. Cold forming makes titanium harder, with the tensile strength tripling and the breaking elongation reduced by up to 90%. When the strain is too high, this leads to cutting edges breaking away.
Nowadays, the properties of the end-use application are being optimized, with a prime example being the Ti5553, or triple-five three titanium alloy. It is low-weight, high-strength, and has a good resistance to corrosion – all welcome properties as far as today's aerospace industry is concerned. This Ti5553 material does not make life simpler, however – it actually increases the problems. Ti6Al4V is a classic alpha-beta alloy for the aerospace industry with a balanced micro-structure (alpha = hexagonal micro-structure, beta = body-centered cubic structure). Ti5553 on the other hand has a higher beta proportion, meaning that it is a near-beta alloy. This is responsible for the above-mentioned increased heat resistance, while also making it tougher to machine. At the temperatures that occur during the cutting process, Ti5553 still has a resistance of c. 900N/mm². The tendency to stick on the edge increases by the beta parts.
The precision and cost-effective machining of titanium puts a real strain on both the processes and the machines. Ever since the early 1960s, Starrag customers have been producing titanium parts for the aerospace industry on their machines. StarragHeckert's in-house specialists have acquired vast amounts of expertise in the machining of titanium and similarly tough materials throughout previous decades. The company carries a reputation as a leading provider of machine tools for processing titanium and more, due in no small part to the expert advice, which they provide in terms of the following areas.
Milling Strategy
Precision and cost-effective production requires the right decisions to be made in terms of milling strategy. The use of virtual machining provides advantages for both the experts and the users: not only does it enable significant time savings in programming; it also reduces complex test-runs on the machine to a minimum.
Combining virtual machining with CAM-programmed RCS 7 software for turbine blades provides the ideal basis for the optimum machining of flow-optimized blades.
Setting out a milling strategy in advance also plays a significant role in the machining of titanium structural parts. Massive blanks of this material require efficient milling into delicate, high-quality prefabricated parts, which have a mere 10% of their original weight when completed. As well as cost-effective rough machining, the right strategy for finishing and smoothing is crucial in terms of a top-quality result.
Tools and Coolants
Knowing how to carry out tricky machining on special stiff tools enables significant improvements in productivity for milling turbine blades, blisks, and impellers. In addition, working in conjunction with reputable producers of ultra-modern tools and coolants enables process-optimization. Working with Starragheckert, customers benefit from the latest in cutting-edge products and global expertise.
![]() |
STC – Stable Machining Centers
StarragHeckert delivers knowledge when it comes to the simultaneous 5-axis machining of tough materials, which carries over into its machining centers. These modern centers fulfill requirements in terms of:
- Process stability
- Finish quality
- Precision
- User-friendliness
- Reliability
In addition, the available machining centers are perfectly adapted for simultaneous 3D machining with, for example, a Ti5553 titanium workpieces. Users note that it is the stable design of the machine, which also cuts down on vibrations, that delivers productive machining and extended tool lives.
To keep pace with increasing demands, the machine has a welded version of a solid, closed gate column. Due to the joint locations of the welded construction, the damping behavior is similar to that in a cast design, with steel exhibiting 25% greater stiffness. The self-locking drives of the rotary axes, which are insensitive to disturbance variables, are worm gears with the highest levels of damping and torsional stiffness, and they also enable difficult cutting processes to be carried out, simultaneously by 5-axis machining, even under heavy loads.
This and other features enable the cost-effective titanium-machining, even with high process forces and extended tool lives.
The robust and precise rotatable single-axis head makes it possible to process bulky and massive workpieces in one machining, with the result being a reduction in set-up times and effort and a shorter process time.
The compact milling head – with a reduced distance between the A-axis and the spindle nose, as well as the dimensions of the actual milling head – mean that there is high running accuracy and little compensating movement on the A-axis. This design offers very good accessibility of the workpiece at a wide variety of angles with short tools and a short flux on the rotary axis and the machine structure. This delivers ideal conditions for maximum machining and precision components.
Particular attention to the generation of heat is also important. The symmetrical machine concept, additional cooling that is room-dependent, intelligent controlling of the working spindle, and cooling of machine components reduces the thermal influence to a minimum, enabling the required precision achievement even for workpieces that require more than 100 hours of machining.
STC to the BTP
Specifically designed for machining large titanium structural parts for the aerospace industry is the StarragHeckert Profiler BTP 5000. Noted for its stable construction and high levels of precision, the BTP complements the top end of the STC range already on the market.
Designed for the complete machining of structural parts made of titanium or other tough materials, i.e. for rough machining with a high chip rate, and for 5-axis simultaneous end processing, is the BTP, or Big Titanium Profiler.
The concept and the dimensioning of the machine structure form the basis of the high dynamic and static stiffness of the machine. A central element of the equipment is the robust, high-precision swivel head, where the construction principles build on the single-axis swivel-head of the StarragHeckert STC range. With a maximum torque of 1,000Nm, and a spindle speed of up to 8,000rpm, the single-axis swivel-head provides optimum coverage of the wide spectrum of technological demands. All of the options for modern and automated machining – such as workpiece and tool measurement, tool encoding, monitoring systems, and other useful functions – are also available where necessary. The machine rounds off by the high-performance StarragHeckert SAM graphical diagnostic system.
Benefits
When it comes to titanium processing, StarragHeckert can count on decades of experience and innovate, energy-efficient machining centers. The effort required in setting up machinery and for stretching and re-setting workpieces reduces to a minimum due in part to simultaneous complete 5-axis machining.
The compact rigid design of the milling head enables cost-effective, simultaneous, 5-axis machining with very good accessibilty to the workpiece. In addition, generously-dimensioned machining centers, with optimum damping, provide uses with excellent finish quality and precision.
![]() |
StarragHeckert Hebron, KY
starragheckert.com
Get curated news on YOUR industry.
Enter your email to receive our newsletters.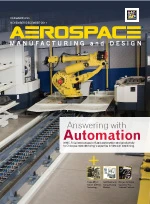
Explore the November December 2011 Issue
Check out more from this issue and find your next story to read.
Latest from Aerospace Manufacturing and Design
- Beyond Aero refines its hydrogen-electric light jet
- Americase's advanced protective solutions
- Social media - what are your thoughts
- GE Aerospace secures Air Force engine contract
- Thomson Industries' online sizing and selection tool
- #53 - Manufacturing Matters - 2024 Leaders in Manufacturing Roundtable
- Join us for insights on one of the hottest topics in manufacturing!
- You can still register for March’s Manufacturing Lunch + Learn!