Mazak Exporting Kentucky-Built Machines
A range of machine models – designed and manufactured at Mazak's Florence, KY plant – are being exported to Brazil, Europe, and several Asian countries.
Mazak Corp. is currently exporting the Kentucky-built Quick Turn Smart. Exports to Europe will begin with the Quick Turn Nexus 450-II MY multi-tasking machines and the ORBITEC 20 machining centers.
The decision to export machines from Kentucky comes as a natural progression for Mazak Corp., reflecting the company's continued growth in the North American market, the ongoing commitment to the highest quality standards, and incorporation of new product designs from the United States.
"Exporting Kentucky-designed and built machines reaffirms the fact that the United States remains a very competitive manufacturing environment for advanced technology products," says Brian Papke, president, Mazak Corp. "In fact, we see the exporting of Kentucky-built machines as a catalyst that lays the groundwork for future expansion of our North American manufacturing operations."
mazakusa.com
New Facility Opens for Hyundai-Wia
Hyundai-Wia Machine America Corporation (HWMA) officials announce the grand opening of its state-of-the-art corporate headquarters and technical center. The 88,000ft² facility in the Borough of Carlstadt, NJ, features more than 21,500ft² of office space along with a 66,500ft² showroom and warehouse. The facility reflects Hyundai-Wia's commitment to the North and South American marketplaces, continuing its rapid growth in the machine tool industry.
According to HWMA's President, Ki Ho Park, "In past years we were concerned that the lingering manufacturing downturn, economic fluctuations, or the fuel shortage would negatively affect our development plans. However, our new headquarters reflects our dynamic expansion and our steadfast commitment to, and support of, existing and new customers."
hyundai-wiamachine.com

MAG's low-flow cryogenic titanium machining process received approval from the U.S. government for its use in production of the Lockheed Martin F-35 Lightning II stealth fighter. According to Lockheed Martin representatives, when broadly applied, this technology could improve affordability and efficiency in the production of the F-35, which is approximately 25% titanium.
Cryogenic titanium machining increases cutting-tool life up to a factor of 10, while doubling the material-removal rate compared to conventional machining methods in certain applications. Development of the multi-patented process, using liquid nitrogen (-321°F), was over a period of years by the team of Creare Inc., H.M. Dunn Co., and MAG-IAS, working with Lockheed Martin, the U.S. Navy Small Business Innovation Research (SBIR) Program Office, and the F-35 Joint Program Office (JPO). Funding was through SBIR program awards.
According to Mike Packer, vice president of manufacturing strategy and technical integration, Lockheed Martin Aeronautics, "This is a prime example of an SBIR-developed technology transitioning from the research and development phase to a system that can enhance affordability for near-term military projects like the F-35."
mag-ias.com;
lockheedmartin.com;
hmdunn.com
Get curated news on YOUR industry.
Enter your email to receive our newsletters.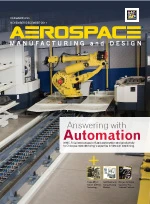
Explore the November December 2011 Issue
Check out more from this issue and find your next story to read.
Latest from Aerospace Manufacturing and Design
- Beyond Aero refines its hydrogen-electric light jet
- Americase's advanced protective solutions
- Social media - what are your thoughts
- GE Aerospace secures Air Force engine contract
- Thomson Industries' online sizing and selection tool
- #53 - Manufacturing Matters - 2024 Leaders in Manufacturing Roundtable
- Join us for insights on one of the hottest topics in manufacturing!
- You can still register for March’s Manufacturing Lunch + Learn!