![]() |
Aerospace systems are among the most complex systems ever devised by man. Finding technical contradictions at every turn is common. Strength, weight, thrust, and drag compete for priority, presenting designers with a never-ending network of optimization problems. Evidence of this complexity can be found in the dimensioning and tolerancing of the thousands of individual parts that make up such systems. Geometric dimensioning and tolerancing (GD&T) is a vital technique to manage design complexity. New analysis tools are coming on-line, enabling manufacturers to take full advantage of the benefits of GD&T for process improvement and yield enhancement.
Created nor Destroyed
As the producers of computer aided design (CAD) software have implemented GD&T functionality and designers have increased their proficiency with GD&T, part dimensioning and tolerancing has become simpler. The total number of dimensions and tolerances has decreased to the minimum required to assure part functionality. A single profile tolerance callout referenced to a CAD surface can replace an entire table of dimensions. Therefore, the complexity of part designs seems to be going down. At the same time, the analytical power required to assess GD&T conformance with the new design requirements is going up. Therefore, manufacturers need analytical power comparable to the computational power embodied in the CAD system.
Do Not Interpret
Every GD&T feature control frame (FCF) defines an explicit tolerance zone. There is no room or need with GD&T for interpretation. The rules governing the evaluation of parts with respect to these tolerance zones are clearly defined in the ASME Y14.5 standard. Yet, the many measurement software packages available to verify part dimensions designed per the Y14.5 standard do not universally apply the standard in their analyses.
Everyone is an Expert
The processing power of today's computing platforms allows complex numerical operations such as the non-linear optimization techniques required to implement and execute the Y.14 GD&T rule base. Some independent evaluation packages, such as Kotem's SmartProfile, have embedded the Y14.5 rule base in the core of their GD&T analysis engine. With a simple CAD-like user interface, supporting easy definition of the part's GD&T requirements layered over this rule base, synchronization of the design and analysis with GD&T is now possible. While the user's task has been simplified, the complexity has not been eliminated; it is simply transferred into the behind-the-scenes operations within the SmartProfile software. By using the SmartProfile software, users gain instant empowerment from decades of GD&T expertise. Now, everyone can be an expert in GD&T.
GD&T Analysis
The example in Figure 1 shows the cross section of a generic attachment detail that forms the mechanical interface between an individual blade and a hub in one stage of a turbine engine.
Some regions of this attachment detail are more critical than others. The tolerancing scheme reflects the relative criticality of the different regions. For example, material-to-material mating surfaces carry relatively tight profile tolerances, while relief or clearance regions carry somewhat looser tolerances.
Note that none of the profile tolerance FCFs refers to datum. This indicates that a simultaneous requirement applies to each feature toleranced in this fashion. No interpretation is needed to assess conformance with the design requirement. This is as it should be, since the parts are assumed rigid bodies. The mating parts can only adopt one orientation with respect to each other. There will either be clearance or interference as determined by this orientation. Therefore, it is crucial that all regions of the overall profile meet their design requirements – that is, conform to their respective tolerance zones – simultaneously.
It Looks so Simple
The profile FCFs are deceptively simple in their appearance. What could be simpler that not having to establish any datum at all? In reality, the analysis is actually quite complex. No datum means no constraints when fitting the actual part data to the profile tolerance zones. Therefore we must find one orientation of the part such that all nine segments of the profile meet their different requirements simultaneously. Almost without exception, the CMM software used to measure such parts cannot properly evaluate these complex tolerance requirements. What is needed is an easy way to deal with this complexity.
Model Based Definition
CAD systems have enabled designers to communicate design requirements to downstream users in manufacturing and inspection by passing CAD models directly to machine tools and inspection systems. Both proprietary CAD system formats, and standardized formats such as IGES and STEP are commonly used, with STEP gradually supplanting IGES as the format of choice. Likewise, the ability to import complete CAD models into the GD&T analysis software enables comprehensive analysis of design intent.
Input the GD&T Requirements
The majority of parts in production today do not have tolerances embedded in their CAD files as actual GD&T objects. The symbols may appear on the computer screen or drawing, but they are stored as annotations (i.e. essentially as comments) rather than as attributes of the features they control. The CAD files typically do not convey the association between features and these tolerance annotations. Therefore, the user must assist in the process by associating feature control frames with features in the analysis software.
SmartProfile software guides the user through the GD&T input process by allowing direct editing of the FCF on the computer screen. Syntactic and semantic checking is done automatically in the background, with highlighting of incomplete items. The user only needs to match the FCF on the SmartProfile screen to the FCF on the drawing. Once the tolerances of interest are defined, the finished project is saved for replay at any time.
Points are Points
The process of evaluating parts for conformance to design requirements can be divided into two major operations: data acquisition and data evaluation. It is possible to use virtually any data acquisition device to collect data for analysis by the SmartProfile software, including multi-sensor measuring machines, video measuring machines, touch probe and scanning coordinate measuring machines (CMMs), laser and CT scanners. Regardless of the type of measurement system, what is important is that the uncertainty of the acquired point data be acceptable in the context of the tolerances under evaluation.
SmartProfile software uses a data import wizard to simplify the reading of data from simple ASCII based .txt or .csv files – formats completely independent of the data source. A key advantage with this approach is the opportunity for normalization of GD&T evaluation across an entire enterprise, including supply chains, regardless of the measuring methods acquiring the data points. Control of the data acquisition devices are by the supplied software, while, performance of the evaluation is with a common GD&T evaluation engine.
Evaluation
With one Click, points automatically associate with their respective features, and then the rule base goes into action. Each FCF triggers an evaluation of a specific design requirement. The complex simultaneous requirement relationships are recognized and evaluated as groups of requirements by the GD&T core, with the results of the evaluations added to each FCF.
In figure 2, we see that the GD&T core has optimized the results such that 86.1% (of the 0.05mm profile tolerances) have been consumed. Looking at the directions of the extreme deviations, circled in red, it is easy to see that shifting the data in any direction will increase the percentage of tolerance consumed. This presentation of the data is vitally important to avoiding costly errors. Using simple evaluation techniques, such as the sum of the squares will likely show this part to be non-conforming when in actuality it is good. Likewise, if evaluation of the individual profile tolerances are independent, rather than simultaneous with fitting, it is likely a non-conforming part would be considered conforming.
Visualization is the Key
The ASME Y14.5.1-1994 prescribes that two actual values be reported for each Profile FCF. However, to gain a complete understanding of the condition of the part and process, it is better to have access to graphical reports such as whisker plots that show the relationship between the actual part surface and the profile tolerance zones (Figure 2). This visual evaluation tool is not new. Mylar overlays have been used on optical comparators for more than 50 years to provide similar information. Of course, today the visual representation is dynamic, 3D, and in full color. For 3D GD&T evaluation and visualization, the Y14.41-2003 standard provides a definition for the display of GD&T in the 3D viewing environment. Figure 3 shows an example of 3D FCFs in the CAD model display.
Everyone gets the Picture
Rapid communication across multi-national companies, including supply chains, is critical in today's competitive environment. The results from SmartProfile GD&T evaluation is savable in a lightweight format that is viewable anywhere with its free viewer. This active viewer can allow everyone up and down the supply chain to see and understand the results in a common format.
Where to from Here?
The emerging STEP AP203e2 standard defines a unification of product (including GD&T) and process (manufacturing and inspection) in one common format. As users deploy STEP AP203e2 and take advantage of this expanded capability, GD&T analysis software will take advantage of the enriched information, automatically considering process parameters as part of the rule base that drives the GD&T evaluation. Knowing, for example, that a blade attachment detail is produced by a broaching operation, as opposed to a creepfeed grinding operation, may lead to alternate analysis paths and opportunities for process improvement.
While considerable knowledge about design, manufacturing, and measurement is always necessary in aerospace components manufacturing, it is possible for global manufacturers to align the benefits of GD&T design with GD&T inspection up and down the supply chain – with the right software.
Quality Vision International Inc. Rochester, NY
qvii.com
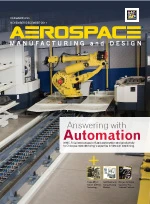
Explore the November December 2011 Issue
Check out more from this issue and find your next story to read.
Latest from Aerospace Manufacturing and Design
- Revitalizing the Defense Maritime Industrial Base with Blue Forge Alliance
- Safran Defense & Space opens US defense HQ
- Two miniature absolute encoders join US Digital’s lineup
- Lockheed Martin completes Orion for Artemis II
- Cylinder CMMs for complex symmetrical workpieces
- University of Oklahoma research fuels UAS development
- Motorized vision measuring system
- Everyone's talking tariffs