![]() |
There have been advancements in materials and processes pertaining to cast urethane manufacturing during the last five years, making it an even more useful way to provide production parts rather than merely prototypes. One of the more versatile methods, cast urethane manufacturing, enables components to be as small as 1" square and as large as 5ft2.
Every shop producing cast urethane parts has its own twists to an age-old, multi-step method to process urethane polymers that can yield strong and stable components. Because of the availability of materials that now meet many customer production requirements, cast urethane parts, as a production manufacturing solution, are seeing rapid adoption.
About 60% of Solid Concept's work is with developed products that are actually in use and not part of a development process, which is a big change from just five years ago. That is how many materials and processes have advanced in this field.
Technology and material advancements have added a lot to the cast urethane process during the last few years, which have only increased the importance of taking a closer look at it as a manufacturing method.
Cast Urethane Process The cast urethane process begins with a model produced through an additive manufacturing technology (polyjet or stereolithography) or with CNC machining. Use of the model as a master pattern then produces a silicone rubber mold. Suppliers, such as Solid Concepts use platinum-based silicone as it better holds tolerances, replicates surfaces, and extends mold life. The high-grade silicone material pours over the pattern, has time to cure, and is followed by removal of the pattern. Curing times may vary, but are usually 24 hours or more per pour. Cast urethane technology incorporates reactive liquid chemicals, called pre-polymers and curatives, which require mixing under very specific conditions. Once the chemicals begin to react with one another, they form polymer chains long enough to produce a liquid-to-solid transition. This gel time dictates the time that processors have to cast the material into the rubber molds. Mixing in of color, with the polymer, produces cast-in color parts. Once cast, the part solidifies and goes through a series of controlled steps involving heat and pressure that enhances cross-linking, developing optimum mechanical properties. This post-curing process is a crucial phase, and can significantly affect the physical properties of the part. The completed part will remain in the mold from minutes to hours before extraction. |
First, speed to market has become an increasingly important aspect of many businesses, including medical, aerospace, and automotive. For example, producing urethane skins that meet all engineering requirements occurs while the customer is waiting for steel or aluminum tool manufacturing. This means that products can be in the market faster than ever before. Focusing on creating production parts earlier, for faster revenue generation, is one of the reasons cast urethane production has grown recently.
If a customer's design is still in the finalization process, cast urethane production – with its shorter mold life and rapid turnaround times – provides a perfect way to work through iterations that best suit rapidly changing customer/market demands. Much like the automotive industry, which often manufactures upgrades of models with minor design changes year after year, other manufacturers, such as those in the aerospace industry, can also benefit from the use of urethanes.
One of Solid Concept's customers uses urethanes in situations where they are unable to project sales of their products for an extended period, and therefore are not willing to make significant capital investments in offshore production tooling. Urethanes allow them to produce parts quarter by quarter, especially in uncertain economic times.
Other applications, more commonly associated with cast urethane manufacturing, are during a product development cycle where the parts produced act as cosmetic/functional engineering models, marketing units, and assembly line development units. All of this can occur while longer lead-time production tooling is in production off shore.
The key is customer-driven urethane production, which has evolved sufficiently at Solid Concepts by using more process control in the application of vacuum, heat, pressure, and time.
Couple that expertise with urethane materials co-developed in-house to yield enhanced mechanical and physical properties, and you can see the evolution. The materials include advanced formula polymers that result in castings that are extremely accurate, strong, stable, and which meet customer requirements for flammability UL 94 VO, impacts test, and more.
Another reason to use cast urethane parts is very practical. If a customer is not going into large-scale production, there may be no reason to produce production tooling at all. The cast urethane process is able to produce several hundred components per year from a single mold. This might be a great solution where customer units sell at a rate in the hundreds of units and not thousands. This short-run situation often makes committing to hard tooling too expensive to consider.
For products that go through yearly redesigns, cast urethane provides the perfect solution, because using the cast urethane process means that such changes can quickly incorporate so that the next product is in the market before a competitor produces a similar product. There are also companies who make their profits from selling consumables, and the cost of the cast urethane stand may not be important in the overall sales scheme.
Cast urethane processing for prototype and production parts is a growing business, primarily in the aerospace and medical industries, but is also developing in automotive and business machines. Anywhere there is a need for skins to cover the external parts, such as panels for aircraft and automotive, cast urethane may be the most economical method of production.
Solid Concepts Inc. Valencia, CA
SolidConcepts.com
Get curated news on YOUR industry.
Enter your email to receive our newsletters.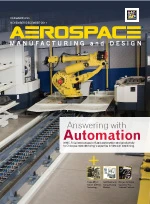
Explore the November December 2011 Issue
Check out more from this issue and find your next story to read.
Latest from Aerospace Manufacturing and Design
- Beyond Aero refines its hydrogen-electric light jet
- Americase's advanced protective solutions
- Social media - what are your thoughts
- GE Aerospace secures Air Force engine contract
- Thomson Industries' online sizing and selection tool
- #53 - Manufacturing Matters - 2024 Leaders in Manufacturing Roundtable
- Join us for insights on one of the hottest topics in manufacturing!
- You can still register for March’s Manufacturing Lunch + Learn!