Sometimes really skilled CNC coders are so good at what they do that they resist adopting CAM software long after others, of lesser abilities, have made the change. That is exactly what happened to Joey Jones, president, Aerotech Machining Inc., a job shop specializing in multi-axis machining of high-end components for the aerospace industry.
"We were primarily a conversational and G-code programming shop. In other words, we wrote out our programs longhand. One day, about 10 years ago, I ran into an apparently simple programming issue that had me stumped. It involved engraving some longhand text – the word open – along a curvature. I was working on this for what seemed like hours and getting nowhere.
"A friend of mine had recently left his manufacturing job in Savannah to work at CAD/CAM Solutions, Atlanta's Reseller for Mastercam (CAD/CAM software from CNC Software Inc., Tolland, CT). I contacted him and he volunteered to write the program and send it to me. Ten minutes later, he not only sent me a program but it was already posted to go to my machine. I bought my first seat of Mastercam that afternoon."
Jones dipped his toes into the CAM waters cautiously at first by purchasing very basic software, Mastercam Mill Level 2. After a short time, he was in all the way with Mastercam Turning, Mill Level 3, Solids, Multi-Axis, and Design. Programming the company's waterjet cutting system is also with Mastercam. Today, Aerotech has multiple seats and there are six users of Mastercam. These capabilities allow the company to aggressively pursue and win attractive aerospace projects, particularly those in which advanced multi-axis manufacturing capabilities are a necessity.
Monolithic Machining
Jones says one of the things driving the demand for multi-axis machining is the increased use of components made from monolithic materials. "In the world of aerospace, everybody is getting away from fabricated assemblies and going to these big monolithic machine structures with no rivets and no epoxies," he explains. "It is nothing for us to put a 1,000 lb piece of material on a machine tool and have a single material part weighing from 40 lb to 50 lb when we are done.
"These structures can be very complex," Jones continues. "You have walls tilted at 10° and you have walls that swarf around from one to the other. You have to have full simultaneous 5-axis motion to be able to manufacture them. You cannot hard code 5-axis. There is just too much going on. Your brain does not think that way."
One option for reducing the complexity of programming 5-axis equipment is to divide and conquer using the 3+2 and 4+1 techniques. For example with the 3+2 option, operations are first performed in three axes, then the other two axes are brought in to finish up what was missed by the first three. From a programming point of view, far fewer movements require accounting for simultaneously, and code generation is far simpler because it is being written in only two or three axes.
"This type of programming is not an option for the types of aerospace parts that we see every day. All five axes have to move at once to accurately recreate these designs. Simplifying the programming and managing all the complexity of five axes of simultaneous motion is where Mastercam excels for us."
Fail-Safe 5-Axis
Although Aerotech has a full complement of machining capabilities – from 2-axis turning to 5-axis milling – one of the most active growth areas for the business by far has been 5-axis milling with trunnion-based Mazak Variaxis and Integrex systems. When the company took delivery of its first 5-axis system, Jones put in a call to Steve, his reseller representative at CAD/CAM Solutions.
"Steve got in his car in Atlanta and drove to Savannah. He came in the next morning and he used Mastercam's post-processor development tools to build a post for me from the ground up on my shop floor. The next day we were making parts," Jones says.
Since that first 5-axis installation, he has identified many tools within Mastercam that improve 5-axis programming and machining productivity while reducing the risks of tool damage and scrap.
Tools That Improve
In and Out of CATIA: There are six brands of CAD software typically used by Aerotech's customers, and Mastercam imports them all quickly and cleanly. Aerospace work most frequently comes in as CATIA files, and verification of the result is on a CMM and compared to the original CATIA model. However, Jones feels that this design and analysis software is too cumbersome to be of use for developing manufacturing processes. Too many machines would be idle waiting for creation of the next program. Mastercam has an approved and licensed translator that allows the model to seamless import into Mastercam where creation of the 5-axis toolpaths occurs. As soon as a CATIA model comes into the shop, programmers import it into Mastercam.
Productive Roughing: For monolithic parts, gross material removal occupies a high percentage of the machining time. For 3-axis roughing work, Aerotech typically uses the Surface Rough Pocket toolpath.
Jones says, "It is very, very simple. If you have a solid model, just window the model, give it a bounding box, select Surface Rough Pocket, and get out of the way. It removes massive amounts of material in a hurry."
Jones continues, "A part we did recently weighed about 200 lb going into the machine and only 15 lb to 20 lb coming out. Roughing was with Surface Rough Pocket and it required just one operation that only took a couple minutes of programming time. Then we came in and put 5-axis motion on the walls because they were slanted."
For 5-axis roughing, Jones typically uses the Curve 5-axis toolpath.
"It too is very simple," he says. "You have floor lines and vertical lines. You chain them and let the machine do the rest."
![]() |
Reducing Interferences: Aerospace work is relatively high risk because the complexity of the 5-axis machining process has a greater potential for interferences (i.e. crashes) that could damage tooling, equipment, or expensive parts.
"We make a titanium part that starts with a block of material that is 1.5" x 4.0" x 16.0", costing about $700. When you scrap one of those, you have painted your company red," Jones states.
So Aerotech's Mastercam programmers work very carefully, looking for mistakes as they go. After every section, the programmers typically check for interference problems with Mastercam's Backplot feature, a computer simulation tool that identifies problems as fine as those involving the shape and size of a specific cutter body.
"Some of Aerotech's 5-axis parts have as many as 80 operations," Jones states. "We do not want to try to fix a problem started in operation 47 that compounded itself with other problems all the way up to operation 78. That would take days. So we clean as we go and get to the machine a lot faster."
As a rule, Aerotech programmers use the Mastercam toolpaths as written, without further modification. However, once Backplot identifies interference, the software gives programmers the ability to quickly jump into problem areas and make fine adjustments to clean them up as needed.
More 5-Axis CNCs
Jones' company has come a long way in 10 years, moving from hand coding to automated 5-axis programming and computer simulation of manufacturing processes. Jones admits he still spends an hour a week experimenting with the latest toolpaths in Mastercam in order to find ones that will allow him to compete more effectively in an arena that calls for high productivity and exceptional attention to detail.
These efforts must be working because the company has added eight more CNC systems within the past couple years. The newest multi-axis machine, which just arrived, has 200" of travel with rapid traverse at better than 4,800ipm. It will produce very large monolithic parts that allow no margin for error. Managing the complexity of 5-axes will be more important than ever.
Mastercam Tolland, CT
mastercam.com
Aerotech Bloomingdale, GA
aerotechmachining.com
Mazak USA Florence, KY
mazakusa.com
Get curated news on YOUR industry.
Enter your email to receive our newsletters.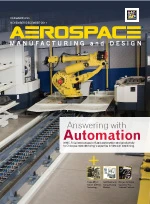
Explore the November December 2011 Issue
Check out more from this issue and find your next story to read.
Latest from Aerospace Manufacturing and Design
- Beyond Aero refines its hydrogen-electric light jet
- Americase's advanced protective solutions
- Social media - what are your thoughts
- GE Aerospace secures Air Force engine contract
- Thomson Industries' online sizing and selection tool
- #53 - Manufacturing Matters - 2024 Leaders in Manufacturing Roundtable
- Join us for insights on one of the hottest topics in manufacturing!
- You can still register for March’s Manufacturing Lunch + Learn!