![]() |
According to the Air Transport Association's 2010 economic report, "When America Flies it Works," operating revenues for U.S. airlines fell by approximately 17% in the wake of the 2009 global recession – considered the worst since the 1930s. These ripples were felt globally. According to the International Air Transport Association, European airlines were also hit by the economic downturn, seeing a 15% drop in revenue. While global profits have slowly started to bounce back, fuel prices hit near-record highs at times. In order to remain competitive and increase margins, airlines have been forced to scale back on expansion plans, including the purchase of new planes and equipment.
All of this has placed the burden on regular fleet maintenance to ensure the integrity of vital aircraft systems and their components. One incident involving a tear in the fuselage of a passenger airline – prompting the Federal Aviation Administration (FAA) to order an examination of older 737s for signs of metal fatigue – underscores the simple fact that age is catching up with many planes in the existing fleet.
So what can be done to address the issue of aging aircraft and parts? Rather than necessitate costly aircraft and systems replacements, recent advances in materials science now allow OEMs and fleet operators to use enhanced systems components made from durable polymer materials, such as polyimides. These high-performance parts help fortify aircraft systems, providing longer life and reduced maintenance for airlines, which increases the bottom line.
As with any complex system made up of numerous components, the parts truly make the whole. Peak performance is important, and this is especially true in aircraft systems. Parts such as bushings, bearings, thrust washers, and sealing rings found in auxiliary power units (APUs), de-icing systems, cabin air-conditioning systems, actuators, jet engines, and landing gear systems are vital to the overall performance and safety of the aircraft. Machined parts made from high-tech materials, such as polyimides, fortify existing systems by providing a unique combination of performance properties, including low weight, durability, and thermal insulation. In addition to using high-performance polyimides, working closely with materials suppliers to manage the engineering process, from powder-to-parts, helps ensure the overall quality and long life of systems components.
Lightweight Choice
As fuel costs continue to fluctuate, the importance of lightweight components in aircraft systems grows. There are several choices when it comes to materials, including metals, ceramics, and carbon graphite. Lighter weight materials, such as polyimides, are an effective choice to decrease costs for structural parts in aerospace applications without sacrificing quality or safety. High performance polyimide parts help reduce the weight of various aircraft systems and, in turn, the overall weight of the aircraft. This all adds up to a decrease in the total amount of fuel consumed, giving an OEM the competitive edge by allowing them to provide fleet owners with significant cost savings over time.
Durability in the Sky
Another area of primary concern to OEMs and fleet operators is the overall durability of aircraft systems. Long-lasting parts that provide optimal performance throughout their lifecycle are worth their proverbial weight in gold. High temperature performance is an important aspect of durability in challenging aerospace applications. Various parts of a jet engine, for example, can generate 315°C (600°F) heat, making the integrity and performance of its components absolutely vital. Polyimide parts can withstand continuous use up to 315°C (600°F) and intermittent use up to 482°C (900°F), and exhibit extremely high dimensional stability at elevated temperatures. This means that even at high temperatures, they do not melt and they keep their shape. Testing shows that parts fortified with high-temperature polyimides have less that 0.04% variation from its original dimensions after cycling from 22.77°C (73°F) to 260°C (500°F) during a two-day period. In addition, polyimide parts are able to withstand thermal shocks very well. Thermal shock is a technical term for cracking under rapid temperature change. Materials such as ceramic can exhibit low thermal conductivity, making them more susceptible to thermal shocks. Polyimides exhibit high thermal conductivity, adding to the overall dimensional stability of the material.
Ultra-durable polyimide parts provide longer life at higher loads and speeds due in part to self-lubricating properties. They do not require industrial lubricants to keep them running efficiently, reducing expenses, as well as time and labor. Self-lubricating grades of polyimides do not melt when exposed to high load or high speed applications. Superior strength and rigidity, combined with self-lubricating properties, provide long, maintenance-free service for critical applications in aerospace systems.
In addition, even at elevated temperatures, polyimides are resistant to chemicals, fuels, and aerospace lubricants. Polyimide parts do not corrode when they come into contact with these various mixtures. This is important when you consider the range of industrial chemicals used in the operation of an aircraft and its various systems, including ethanol, toluene, JP-4 jet fuel, skydrol, and hydraulic fluid.
Finally, polyimides exhibit excellent wear resistance. This means that parts made from polyimides do not easily wear down as they are put to use, maintaining clearance between systems and their components. What you do not want are parts to erode, resulting in rattle and shake as various parts and components bump and scrape one another. This is not good for the parts, or for the overall performance of any aircraft systems. Less wear equals longer lifecycle and better performance with reduced maintenance.
![]() |
Added Protection
Polyimides exhibit excellent thermal insulation properties. This can be important when you consider the complex inner workings of an aircraft. For example, in a de-icing system, metal tubing routes hot air from the jet engines to the wings. Polyimide components around and against the metal tubing prevents migration of heat further into the wing structure to other sensitive systems and devices. The polyimide isolates the hot metal tube, ensuring that heat does not transfer to other areas of the wing.
Just as important as choosing the right material, exercising process control can provide an added level of quality assurance. In order to ensure the performance and increased lifecycle of aerospace finished parts, OEMs should look to work as closely as possible with their materials suppliers, taking a more active role in the development of aircraft systems components from powder-to-parts. Consultation with available materials science experts and engineers can help ensure exact material and part design specification, while extensive product testing can ensure performance.
In these challenging economic times, OEMs and airlines must do whatever they can to operate as cost-effectively as possible without sacrificing performance. High performance parts for key systems are a very important step in the right direction. Working closely with materials science experts to co-engineer parts to exact specifications can help ensure that parts made with high-grade polyimides – such as Meldin 7000 – are able to provide a combination of performance properties. Lower weight polyimide parts mean lighter systems aboard planes that use less fuel over time, while durable parts that can withstand challenging aerospace environments mean longer lifecycle, reduced maintenance, and fewer replacement parts. In the end, OEMs and fleet owners are left with quality parts that truly do make the whole, decreasing operating costs and driving revenues across the board.
Saint-Gobain Performance Plastics Bristol, RI
plastics.saint-gobain.com
Get curated news on YOUR industry.
Enter your email to receive our newsletters.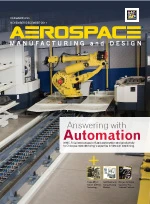
Explore the November December 2011 Issue
Check out more from this issue and find your next story to read.
Latest from Aerospace Manufacturing and Design
- Beyond Aero refines its hydrogen-electric light jet
- Americase's advanced protective solutions
- Social media - what are your thoughts
- GE Aerospace secures Air Force engine contract
- Thomson Industries' online sizing and selection tool
- #53 - Manufacturing Matters - 2024 Leaders in Manufacturing Roundtable
- Join us for insights on one of the hottest topics in manufacturing!
- You can still register for March’s Manufacturing Lunch + Learn!