Return Ball Nut Technology
Conventional ball nut designs recirculate the balls through some external mechanism – tubes, inserts, or end deflectors. The Drake internal return ball nut uses the track of the nut to recirculate the balls – no tubes, inserts, or deflectors are used. Drake's design recirculates the balls internally, simplifing the structure of the nut, therefore, making the ball nut less costly to produce.
With conventional ball nut designs, aligning the finished thread with the return system requires complicated machining and fixturing. With the Drake internal return ball nut – you simply find the roughed thread in the hardened blank, then finish grind the advance and return features in one finish grind operation. Drake engineers have developed special grinding processes and machines for licensees, and all machines are shipped pre-programmed to machine and then grind all features of the internal return ball nut. Drake internal return ball nuts are inherently safe and easy to assemble, with no holes through the walls and no loose parts, as well as being lighter and offering a small ball nut diameter for a given ballscrew.
Drake Manufacturing Services Co. Warren, OH
drakemfg.com
Truing, Dressing
The FC-250EX is a semi-automatic diamond and CBN wheel truing and dressing machine with full enclosure to provide dust control and improved operator safety. The FC-250EX is designed for truing and dressing of flats, angles, and radii on diamond and CBN single wheels, and multiple wheel packs. It features PLC-controlled, automated dressing cycles with servo-driven dressing wheel infeed, power swing, and oscillation.
Use of the FC-250EX allows for increased efficiency and accuracy by profiling, modifying profiles, and truing wheels offline of the production grinding machinery. The machine is simple to operate, quick, accurate, and cost effective, and features a wheel diameter capacity up to 14" standard – with options for larger wheels.
The heavy duty one piece cast iron base provides extra rigidity while minimizing vibration. Standard features include ExVision, a computer-driven vision system with a software program specifically designed for the FC-250EX and its various applications; an automatic power zoom; and a 2-axis DRO for measurement.
Rush Machinery Inc. Rushville, NY
rushmachinery.com
PSPs work for high-temp, MRO repairs
Pre-sintered preforms (PSPs) produced at the Wesgo Metals manufacturing site in Hayward, CA, are ideal for high temperature applications in the aircraft maintenance, repair and overhaul (MRO) industry. MTC's newest PSP dimensional capabilities include significantly larger and thinner sheets. PSPs are a sintered metallurgy product composed of a customized blend of brazing and superalloy powders. They are available in various shapes and compositions and can be used for crack repair and dimensional restoration of aero-engine components such as turbine blades and vanes.
For customized applications, MTC offers PSPs in various compositions and shapes, with plate thickness ranging from 0.010" (0.3mm) to 0.060" (1.5mm). An innovative new process has recently extended the range of thicknesses available to 0.200" (5mm). The preforms are cut from the sintered plate, tack welded to a component, and vacuum brazed. PSPs are also available in pastes and paints, which are ideal for difficult-to-reach areas.
Many OEMs and repair facilities depend on PSPs to rebuild the contours of turbine blades and vanes. MTC's PSPs provide selective build-up of the part, saving time, enhancing cost-effectiveness, and avoiding the distortion associated with welding. With turbine temperatures reaching up to 1,300°C and the presence of hot corrosive gases, aero-engine components face extensive wear. Rather than purchase expensive, new components, PSPs provide an effective, reliable solution for repairing cracks and reestablishing worn areas in components, thereby saving considerable time and money while extending their life up to three times. Unlike traditional brazing pastes and green tapes that require multiple re-brazing cycles and present the added problem of uncontrollable shrinkage, the porosity of MTC's preforms is less than 2%, which helps eliminate shrinkage and subsequent distortion. In addition, there is minimal post-braze grinding or machining needed with PSP components.
Morgan Technical Ceramics Fairfield, NJ
morgantechnicalceramics.com
Get curated news on YOUR industry.
Enter your email to receive our newsletters.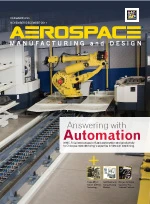
Explore the November December 2011 Issue
Check out more from this issue and find your next story to read.
Latest from Aerospace Manufacturing and Design
- Beyond Aero refines its hydrogen-electric light jet
- Americase's advanced protective solutions
- Social media - what are your thoughts
- GE Aerospace secures Air Force engine contract
- Thomson Industries' online sizing and selection tool
- #53 - Manufacturing Matters - 2024 Leaders in Manufacturing Roundtable
- Join us for insights on one of the hottest topics in manufacturing!
- You can still register for March’s Manufacturing Lunch + Learn!