Nine commercial aircraft are on the frontier of aviation safety, carrying sensors that monitor their structural health along with their routine maintenance. These flight tests on regular routes are part of a Federal Aviation Administration (FAA) certification process that will make the sensors widely available to U.S. airlines.
Dennis Roach, a senior scientist in Sandia National Laboratories’ Transportation, Safeguards & Surety Program, says, “Our activities are proving that the sensors work on particular applications and that it is safe and reliable to use these sensor systems for routine aircraft maintenance.”
Delta Air Lines Inc. and a foreign aircraft manufacturer have partnered with Sandia researchers in two separate programs to install about 100 sensors on their commercial aircraft. These teams worked together to provide the installation procedures for technicians and now oversee monitoring of the in-flight tests.
The flight tests complement laboratory performance testing at Sandia to provide the critical step in a decade-long journey to enhance airline safety through a more comprehensive program of structural health monitoring. Structural health monitoring (SHM) uses nondestructive inspection principles and built-in sensors that automatically and remotely assess an aircraft’s structural condition in real time and signal the need for maintenance.
Two SHM systems
The current SHM program is testing two sensors: comparative vacuum monitoring (CVM) sensors manufactured by Structural Monitoring Systems and piezoelectric sensor arrays produced by Acellent Technologies Inc.
CVM sensors improve crack detection by monitoring galleries, or 0.025" channels laser-etched into the Teflon sensor. CVM sensors, mounted in areas of the aircraft known to experience fatigue, are bonded to the surface of the structure with an adhesive that seals out the atmosphere, creating a vacuum inside the gallery. When a tiny crack intersects the gallery, the pressure changes, the sensor records it and alerts inspectors before the crack becomes a safety issue.
Piezoelectric sensors (PZT) are strategically distributed in polyimide films – Acellent’s SMART Layers – that adhere to an airplane’s surface to monitor specific regions for damage. The PZT sensors communicate with one another by transmitting and receiving ultrasonic surface waves called Lamb waves. This creates a mini-communications network. Damage to the aircraft disrupts or changes the signal patterns from the baseline communication signals. Software measures and analyzes any changes and sends an alert to the inspector.
Both of these onboard sensors must meet the same performance and reliability standards as those required for current maintenance inspections. The readouts provide inspectors with a pass/fail decision so the results can’t be misinterpreted.
Researchers hope SHM eventually will permit the real-time condition of the aircraft to dictate maintenance.
“The ultimate goal is to monitor it in-flight and have it tell you ‘I need some attention, I’ve got a problem here.’ So you do condition-based maintenance rather than time-based maintenance,” Roach says.
Sandia also is researching wide-area monitoring using piezoelectric and fiber-optic strain sensors for composite materials in aircraft. Impacts don’t always show dents in composite materials, so SHM techniques are needed to find structural damage within what appears to be a smooth, undamaged surface.
Sandia National Laboratories
www.sandia.gov
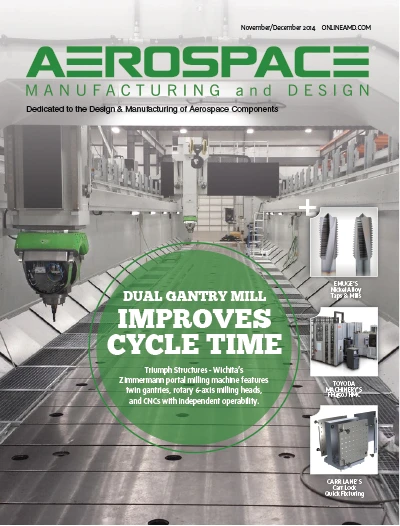
Explore the November December 2014 Issue
Check out more from this issue and find your next story to read.
Latest from Aerospace Manufacturing and Design
- Heart Aerospace relocates to Los Angeles
- Fixtureworks introduces Stablelock Clamps
- Piasecki acquires Kaman's KARGO UAV program
- PI Americas’ long-travel XY piezo nanopositioners-scanners
- AAMI project call submission deadline extended to May 12
- Jergens launches cast iron tooling column additions
- Airbus to acquire assets relating to its aircraft production from Spirit AeroSystems
- FANUC America's Cobot and Go web tool