Manufacturers employ turning, milling, and drilling operations to machine features on workpieces. However, those processes can produce burrs and undesirable sharp edges at feature borders. These edge conditions may result in material breakage when the part is in use, can structurally weaken it, and may pose a danger for those handling it. These consequences are what many end users consider as reasons to reject parts from suppliers.
Manufacturers traditionally remove burrs and sharp edges using hand grinders and other manual processes. Such methods are slow and require removing the part from the machine tool and re-fixturing it for deburring or chamfering operations. Moreover, even when performed by skilled craftsmen, these operations lack the necessary process consistency when going from part to part.
An alternative to manual deburring is mechanized edge profiling (MEP), which eliminates unacceptable edge conditions by applying an engineered tool using the same equipment that machined the part features.
The MEP process enables the final edge condition to be exactly defined and programmed through the machine’s CAM system, resulting in maximum repeatability. Overall part production time is reduced because the part does not have to be removed from the machine and re-fixtured, and tolerance stacking and other inconsistencies that occur from setup to setup are eliminated.
In response to this trend, today’s cutting-tool makers continue to develop tools that enhance the benefits of the MEP process.
Prime candidates for MEP
Considering the rigorous demands for part accuracy and consistency, jet aircraft components are prime candidates for MEP.
For example, aircraft turbine engine components are categorized as non-rotating and rotating. For MEP of non-rotating engine parts, such as drums and casings, edge profiling usually consists of standard chamfer and break-edge tooling, applied on the equipment that machined the part.
For critical rotating parts, such as fan and compressor discs, aerospace companies have higher standards and demand complete elimination of surface imperfections. Edge conditions typically must undergo lab approval and certification. To deburr these parts, toolmakers have developed high-accuracy, fully repeatable, custom MEP tooling.
MEP tool development
Standard deburring and profiling tools, such as those applied on non-rotating parts, include coated solid-carbide chamfering end mills with 45° and 60° cutting edges, as well as tools that use indexable inserts to produce 45° and 60° chamfers.
For the most critical applications, toolmakers provide tools custom-engineered to profile edges and remove burrs specifically at the entry or exit of a hole. Some tools combine those capabilities and can remove both entry and exit side burrs.
These custom tools often feature complex cutting geometries. The most sophisticated have edge designs that produce a chamfer with an edge radius preceded by lead-in and lead-out angles engineered to prevent formation of secondary burrs.
MEP in action 303 stainless Radius vs. chamfer TiAl-4V |
Specialized tool development goes beyond the cutting edges. For profiling burrs and edges at a hole entry, or top surface of a component, research shows that the combination of a right-hand cut with a right-hand helix is most effective because it removes the cut material from the part. Alternatively, for exit burrs on the bottom surface of a part, a right-hand cut combined with a left-hand helix works best, again because that configuration moves chips away from the component.
Other application analyses indicate that MEP tools engineered for removing burrs at the top or entry of a hole provide longer tool life than tools intended for removing burrs at the bottom or exit end of a through-hole. That is because a deburring tool designed to reach through a part to access the hole exit will be longer and smaller in diameter than one that is intended to do its work from just one side of the hole. A longer and smaller-diameter tool is prone to instability and vibration, both of which can chip or break a carbide tool. As a result, most shops opt to use separate tools to deburr the entry and exit edges of a hole rather than a single tool that can do both.
Longer, smaller-diameter tools also require more care with regard to choosing cutting parameters. A short, sturdy tool can run faster without vibration or other problems. Part geometry and features make a difference as well. When cutting conditions are stable and cuts are smooth and uninterrupted, more aggressive cutting parameters can be applied. On the other hand, part features such as access holes that interrupt MEP cutting paths force the use of more conservative parameters to minimize tool wear and prevent premature failure.
Part of the ongoing development of MEP tooling combines machining of a feature with deburring. For instance, the MEP cutting edge would be located at the top of the end mill so it could simultaneously machine the diameter of the hole and deburr the entry edges.
Material challenges
Many aerospace materials present additional machining challenges removing burrs and chamfering their sharp edges. Nickel-base alloys used in engine components, for example, are tough and are poor conductors of heat. The cutting tool absorbs the heat generated by cutting, which accelerates tool wear.
Accordingly, when determining the metallurgy and geometry of a tool, toolmakers have to strike a balance between edge sharpness and strength. A hard carbide substrate material may resist thermal and abrasive wear well, but it will lack the impact resistance of a substrate that features additions of cobalt or other alloying material to increase toughness. In the same way, a dead-sharp cutting edge may be more prone to breakage as compared with one that has a hone or other edge-rounding preparation. Toolmakers also fine-tune rake and helix angles as well as tool coatings to achieve the best results with specific workpiece materials.
Tool size
For processing large holes and edges, toolmakers can design tools of any size for which suppliers can provide a large enough blank. However, there are limits on the small side of the spectrum. Currently, the smallest radius that can be ground is about 0.2mm, with proportionately smaller lead-in and lead-out angles.
Custom MEP tools have specific radii, chamfers, angles, and combinations of those features. The tools commonly have square cutting edges. However, ball-nose and lollipop-style tools are also available to profile features of a component whose contours restrict access of a square-edged MEP tool. Applied on a 5-axis machine, these tools can scan the line of a complex part profile and create a radius on long, contoured edges.
MEP in operation
To maximize accuracy and consistency – and save the time spent moving a part from machine to machine – manufacturers usually perform MEP within the part-feature machining operation.
Typically, deburring occurs after all machining operations are completed. The CAM program directs the MEP tools to deburr all the holes and break sharp edges in sequence. Some MEP tools can be used to deburr a variety of holes, and some profiling tools can be applied on three or four different features, such as the bottom of a hole or the bottom of a scallop contour.
To ensure that the proper amount of edge profiling takes place in the correct location, the hole or feature involved must be defined or measured before the MEP operation begins. When part tolerances are tight, the part surface location is well defined and in-process measurement may be unnecessary. However, when tolerances are generous, measurement is necessary after initial machining to determine the location of the edge or feature requiring profiling.
To ensure that it will profile the part correctly, the tool itself must be measured and located. Because the tool radii are so small – and for practical purposes, unmeasurable – the tool length is specified in the CAM program. The operator can confirm the tool length away from the machine with a presetter or on the machine via a laser or touch probe. Feed rates are calculated relative to the measured dimensions of the part features and the tool. The most sophisticated custom deburring tools are 100% measured by their manufacturer to a tolerance of 40µm on the tool profile, including runout.
Deburring or chamfering should be considered finishing passes, with the primary focus on quality. Productivity is always important, but especially in the case of expensive aerospace components, pushing the tool to maximize output can have negative – and expensive – repercussions. Consistency, reliability, and elimination of scrap parts are paramount.
Conclusion
Parts with out-of-specification sharp edges and burrs are more and more frequently becoming expensive scrap. Manufacturers need a method to deburr components and profile part edges that is consistent, documentable, and cost efficient. MEP fills that need because it replaces manual operations that, no matter how skillfully performed, can be inconsistent from part to part and incur labor, setup, and part handling expenses. Some end users have already banned manual deburring because it cannot be documented and certified.
The most efficient and cost-effective MEP represents a combination of engineering development and application expertise. Toolmakers that offer a complete solution will help streamline the manufacturing process and produce new levels of quality and productivity.
Seco Tools
www.secotools.com/us
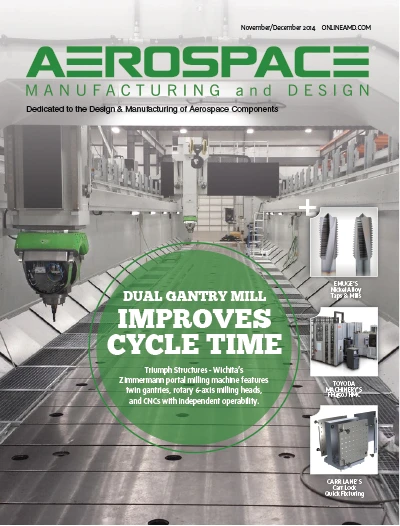
Explore the November December 2014 Issue
Check out more from this issue and find your next story to read.
Latest from Aerospace Manufacturing and Design
- Safran Defense & Space opens US defense HQ
- Two miniature absolute encoders join US Digital’s lineup
- Lockheed Martin completes Orion for Artemis II
- Cylinder CMMs for complex symmetrical workpieces
- University of Oklahoma research fuels UAS development
- Motorized vision measuring system
- Everyone's talking tariffs
- Boom Supersonic to launch Symphony engine testing in Colorado