Taking a cue from automotive manufacturers, the new world of aerospace competitive dynamics includes efforts to aggressively reduce costs by squeezing the supply base for price reductions. Increasingly, aerospace manufacturers (OEMs) are pressuring suppliers to deliver improved quality, increased production, and enhanced service – all at lower prices.
The supply-base strategy supports the growing trend among aerospace OEMs to maintain or grow market share, improve the fuel economy of their product offerings, and deliver competitively-priced planes. This strategy is designed to achieve both improved OEM profitability and long-term viability.
Evidence of this trend can be found in the roll out of Boeing’s Partnering for Success program in 2013. Boeing’s program includes a goal to reduce supply-base costs by at least 15%. Failure to comply with the proposed partner agreement may result in a supplier’s addition to the no-fly list, a reference to the supplier’s exclusion from future bid lists.
Airbus and other aircraft manufactures are pushing the supply base for reduced prices and other supply-cost saving initiatives, too. Additional macro supply-based initiatives include developing mega Tier 1 suppliers which will provide large assemblies and design-sharing or development capabilities. These mega suppliers could consolidate the aerospace suppliers underneath them as Tier 2 or Tier 3 suppliers. Among other benefits to the OEMs, reduced SG&A costs, freight savings, and economies of scale for suppliers will result in greater cost saving potential to be passed on to the customer.
All in, it is a transformational shift in the aerospace supply industry.
But what if the OEM’s push too hard or, as some pundits fear, force supplier failures? Not to worry. The aerospace OEMs have other devices in their tool box to manage extraordinary supplier circumstances. And, they don’t have to look beyond the automotive industry as the prime example of how those distressed supplier management tools work.
Learning from other industries
The aerospace industry’s effort to reduce supply costs are analogous to the transformational supply-base changes spearheaded in the automotive industry over the past 30 years. Manufacturers have a host of strategies at their disposal including: supply base consolidation under mega Tier 1s, long-term supply agreements offering 1% or more of annual price reductions, out-sourcing major design elements, and Tier 1’s driving a culture of cost-sharing ideas to reduce overall supply costs.
The automotive industry’s transformation was at times bumpy, but those efforts have become a way of doing business and have led to failures in the supply base. The push to improve supplier performance, eliminate waste, and improve quality has resulted in billions of dollars of savings to automotive manufacturers.
What did the automotive manufacturers do when a critical supplier was failing, near failure, or pushed to the brink by these changes? The auto OEMs rolled out complementary agreements to supply agreements called the accommodation agreement and access and security agreement. These agreements are tailored to each supplier situation and are negotiated to ensure near-term supplier performance and continuity of supply to the customer. The primary goal is to avoid the immediate shut-down of the OEM production lines but also to provide time and capital to the supplier to address the supplier’s circumstance or achieve a desired outcome for the constituents.
The aerospace OEMs have commandeered those agreements and are rolling them out in their supply base. Over the past couple years, our firm has been engaged in several aerospace supplier matters in which these agreements were offered up by the aerospace OEM to form a new basis on how the supplier and OEM will work together in the near term. These agreements are carbon copies of the automotive agreements established over the course of the past 30 years.
What are these agreements and what do they mean? Should the supplier and other interested parties of the supplier, like the secured lender and equity owner, participate in those agreements? Below we explore the general terms of the agreements used in the automotive industry and analogous to the terms now being negotiated in the aerospace industry agreements. Each accommodation agreement and access and security agreement is unique and tailored to the particular supplier’s circumstances and, as such, one agreement will not fit all situations.
Overview
These agreements are the cornerstone approach that assist distressed-supplier constituents – supplier, lender, customer, management, and ownership – in controlling and potentially resolving supplier distress in which dominant customers are unable to secure immediate, near-term supply, or if supply shutdowns would cause significant damages to the OEM.
These agreements are typically entered into by the distressed supplier, its lenders and its major customers, which could be OEMs or Tier 1 suppliers. The purpose is to provide protections to the supplier and its lenders on certain collateral, while ensuring access to production facilities for customers to allow for continued supply of production while a recovery plan is developed or implemented. Protected collateral may include accounts receivable and inventory that may be the collateral underpinning of the secured loans between the supplier and lender.
The customer’s motivation to enter into an accommodation agreement is typically driven by the associated risk presented by the supplier’s and the customer’s ability to mitigate those risks. For example, if a customer is presented with an immediate supply risk, but such risk can be easily and inexpensively mitigated through re-sourcing efforts, its desire to participate in an accommodation agreement may be limited. However, if supply risk is not easily mitigated, such as in situations where a supplier is sole-sourced, or in situations where resourcing presents a significant cost and time table for execution, an OEM will have significant motivation to participate. This dynamic provides certain leverage for lenders and borrowers to secure enhancements to the commercial relationship and time to provide a runway to fix the business or resolve its distressing circumstances.
These automotive supply-industry agreements have transitioned to aerospace, heavy truck, and other industries that mirror oligopoly-type market structures; environments where there are few OEMs and large supply bases.
There are many factors that must be considered when assessing the leverage that exists in a particular supplier situation. Generally speaking, those situations include:
- Single-source supplier of at least one component part for at least one customer
- Technical-service provider to the OEM or otherwise key-service provider
- Ease at which customer owned tooling can be moved and the location of the tooling
- Nature of the complexity of the products the supplier produces, including the amount of time necessary to approve a new supplier of the parts and, in the case of aerospace, FAA and other requisite certifications
- OEMs’ specific supply-base strategies that may include maintaining industry capacity or other considerations
- Customer concentration and the interrelationship of the supplier to other suppliers and customers whose operations would be impacted by a supplier failure, often in a just in time delivery environment
- Specific intellectual property owned by the supplier
Due to the collateral protections afforded to lenders and suppliers by accommodation agreements, it is typically best for key constituents to secure an accommodation agreement as soon as possible. As an example, collateral protections could include an expressed obligation of the customer to purchase from the supplier the usable and merchantable inventory. The longer the negotiations, the more options a customer will typically identify for re-sourcing alternatives and the less leverage the supplier and lender have.
Key provisions of these agreements may include the following:
Accommodation agreement
Customer accommodations
- Expedited payment terms and “bulletproofing” of accounts receivable
- No re-sourcing of purchase orders
- Inventory purchase obligations
- Limitation of setoffs against supplier accounts receivable
- Re-pricing or orderly re-sourcing of underperforming or loss contracts
- Potential source of funding in event of cash short falls
Lender accommodations
- Lender increases its lending to the supplier via borrowing-base advance rate enhancements on accounts receivable and inventory or deem certain accounts or inventory eligible based upon strength of the customer collateral protections or accommodations
- Agree to revolve the credit absent future defaults and continued customer accommodations
- Provide time for the borrower to execute the recovery plan or other initiatives to resolve its circumstances
Supplier accommodations
- Supplier builds excess finished goods inventory (parts-bank build) to protect customer’s production demand
- Tooling acknowledgement as customer owned property, if applicable
- On-going production to support customer demand
- Allowing lenders and customers open access to the supplier’s facilities
- Provide financial information, reporting of production, etc.
- Agreement to execute the agreed-to plan which may include refinance of the debt, sale of the business, orderly closure, or other strategies
- Require the borrower to seek other customers participation in the accommodation agreements
- Right of access and security agreement
Access and security agreement
The access and security agreements typically go hand-in-hand with the accommodation agreement. While the accommodation agreement benefits the supplier by providing enhancements to the standard terms and conditions of an OEM agreement, the access agreement provides benefit to the OEM as a fail-safe in the event that a supplier failure results in a disorderly shut-down.
For the benefit of the customers and to provide an ability to maintain supply upon a supplier’s default, customers secure the right to access the supplier’s facility and run the production, often by providing adequate protection payments or access fees to the lender. This is a worst-case scenario, in which the supplier completely fails. This agreement provides the customers a back-stop to supplier failure allowing them to access the facility, use the supplier’s equipment to run production, and preserve near-term supply. General terms of the agreement are:
- Grant of continuing security interest in the real estate and operating assets for the express purpose of utilizing them to run production – security interest is junior to the liens of the lender
- Occupancy period is defined (typically 12 months)
- Operating costs including direct materials and labor; 100% funded by customer including all other costs of occupancy, overhead costs including taxes, utilities – corporate charges, lease payments in lieu of the purchase order price
- Access fee to the lender – a monthly fee the customers pay to use the assets
- Customers provide certain indemnifications for cause of actions based upon direct result of customer actions during the occupancy period post
As a result of these agreements, and subject to diligent monitoring post close, the lender and suppliers enjoy significant value enhancements on the collateral. These enhancements may include protection against customer set-offs, secure inventory buy-back, potential pay-down of supplier loans based upon expedited payment terms, and opportunity to sell other collateral such as equipment at greater than liquidation values.
Further, the parties enjoy a controlled process to monitor the supplier but also allow time for the supplier to execute its business plan and, hopefully, improve its value proposition. In other words, through this process and related agreements, the parties to the supplier potentially avoid catastrophic failure damaging all the parties to the supplier. Suppliers may be able to effectively resolve their distressing challenges and improve to a stable, reliable supplier.
Conway MacKenzie
www.conwaymackenzie.com
About the author: Joseph M. Geraghty is senior managing director, Conway MacKenzie. He can be reached at jgeraghty@conwaymackenzie.com or 937.222.7317.
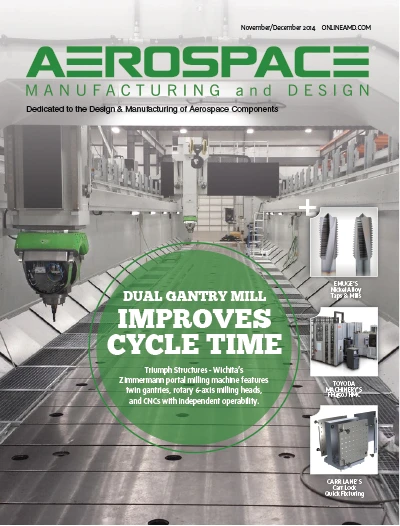
Explore the November December 2014 Issue
Check out more from this issue and find your next story to read.
Latest from Aerospace Manufacturing and Design
- Trelleborg acquires Aero-Plastics
- Industrial automation products, enclosed encoders
- #61 - Manufacturing Matters: CMMC roll out: When do I need to comply?
- AIX shows aircraft interiors are a strategic priority for global airlines
- Machine Tool Builders Roundtable: Turn equipment into expertise
- No time to waste: How to machine MedTech parts more efficiently
- The 5 Best and Fastest Spindle Repair Services
- Mill smarter, not harder: How collaboration optimizes production