When Fori Automation’s leaders began consulting with experts about working with the aerospace industry around 2006, several people offered the same advice.
“We were told very early on, don’t use the A-word. Don’t use the word automotive,” says Paul Meloche, vice president of sales for the Shelby Township, Michigan-based automation company. “Whatever you do, when you walk up to an aerospace customer, do not tell them that you’re an automotive supplier.”
Both industries make products that move people and cargo, face strict regulations, and use a lot of metal. But the similarities don’t go far beyond that. Automotive production, despite some recent trends, is still focused on high volume, and getting the best return on investment from fast line speeds. Aerospace, despite increasing productivity, is still focused on lower volumes and no margins of error for defects.
Don’t talk about your automotive customers? Kind of tough when your best references come from Ford, Volkswagen, and Kia, Meloche says.
Thankfully, he adds, attitudes are changing. In recent years, Fori has won work from Lockheed Martin, Bombardier, Brown Aerospace, and Spirit Aerosystems. The company expects much of its future growth to come from the ongoing aerospace boom as manufacturers step up production rates to whittle down the more than $1 trillion backlog for commercial aircraft.
Sharing automotive lessons
That need to step up production has several aerospace OEMs looking to industries that manufacture products more quickly. While aerospace companies aren’t looking at the 100 units per hour that high-volume auto plants achieve, they are looking for processes, automation advances, and equipment that will improve assembly times.
Meloche says Fori has won its biggest contracts by rejecting the old advice it received and has instead talked about applying automotive expertise to plane building.
“Aerospace companies really started studying the processes much more than the actual equipment,” Meloche explains. “They wanted to understand how companies moved parts and equipment around so quickly, how they did it consistently even when switching products or cycling between different shifts. We’re very process oriented because of working with auto producers on those manufacturing processes. That was attractive to aerospace.”
Fori’s main aerospace offerings are automated guided vehicles (AGVs) – electrically powered vehicles that move workpieces or machine tools around a plant, a function traditionally performed by conveyer belts. The company was able to redesign products developed for automakers for aerospace functions, Meloche explains.
There are five basic systems on an AGV – power, navigation, communications, propulsion/steering, and the chassis. To convert automotive AGVs for aerospace use, Fori engineers only had to redesign the chassis. Fori’s aerospace systems are often larger and have to carry and lift much heavier weights than the automotive ones.
“The chassis is custom designed in aerospace to the application – the size, the length, the width, the height, lifting capacities, the types of lifters, and any customization they may need to move their aerospace part or tooling down the assembly line,” Meloche states. “In physical dimensions, they’re not necessarily larger, because in the automotive applications, they’re as large as the car and can support four people riding on the carts. But from a capacity perspective, from being able to load and lift components, they’re much larger than automotive ones.”
He adds that because Fori was able to bring so much of the engineering and design work for the AGVs from its automotive business, it was able to price its products very competitively when it began seeking aerospace work.
Different worlds
In some ways, the auto and aerospace worlds are becoming more similar. Because of increased competition and changing customer tastes, automakers rarely sell more than 200,000 versions of any one vehicle. So in recent years they’ve adopted slower, more flexible assembly systems that let them switch between different vehicles quickly. At the same time, aerospace companies have embraced automation of some functions and have increased production rates. But Meloche says Fori quickly realized that the gulf between the two is still massive.
Siemens partnership leads to Lockheed work Despite hearing that aerospace customers didn’t like the word “automotive,” Paul Meloche, Fori Automation vice president of sales, says he was able to get in front of decision makers at Lockheed Martin because of one key relationship. Fori engineers had worked closely with Siemens to develop the control systems for its automated guided vehicles (AGVs), and Siemens was working with Lockheed. “Siemens brought us to them and said they should take a look at what we had,” Meloche says. “Lockheed quickly realized that the technology we were offering was really new to their industry. That, combined with the endorsement of Siemens, who was the primary supplier of controls at their plant in Marietta, Georgia, really solidified us as the choice for Lockheed Martin.” He adds that it helps that high-speed production goals had made Lockheed Martin more open to new production concepts. From that Siemens introduction to the first order took only about three months. “We were fortunate that we had a technology that really had a lot of advantages to their specific application,” Meloche says. Lockheed began using Fori AGVs for assembly of F-35 fighter planes in 2010. |
The biggest differences are scale and cost. The smallest planes tend to dwarf even the largest sport utility vehicles. And in an automotive plant, time is a more valuable resource than components. If workers or equipment damage a car engine, technicians can take it offline and repair that part without losing much production time. As long as the assembly line continues to hum, certain levels of part losses are acceptable. In aerospace, a single part can be worth tens of millions of dollars, so part safety has to be a much higher priority.
“Our first aerospace order was from a drilling supplier. They wanted an 18ft tall, 25,000 lb drill fixture with curved rails that mirrored the shape of a fuselage fixture,” Meloche says. “They wanted to put that rig on an automated platform that would drive the drill up and down the 400ft assembly line, drive into position, lock itself to the floor to have positional accuracy of 0.005", then level the platform corner-to-corner to 0.005°, to set up a drill machine for drilling these panels.”
That led to one of the most complex AGVs Fori engineers have built. The functionality was very different from the automotive AGVs that tend to repeat the same basic routes hundreds of times per day, often while carrying employees. Aerospace customers rarely moved parts or tools more than a few times per day, but when the systems moved, they needed pinpoint precision.
Fori representatives altered their selling points a bit. Instead of talking about the ability to constantly repeat tasks, not as big a selling point to aerospace manufacturers as automotive ones, they focused on flexibility.
“The AGVs can be multitaskers. You can use one to tow a plane into position for work, then have it pick up a machine tool for work in a different location. Or you could have it move somewhere else in the plant to move parts from station to station,” Meloche says. “Generally, we’re picking up a piece of tooling. It could be a wing, it could be a fuselage, or it could be an engine on top of that tooling fixture. As long as it’s on a piece of tooling that I can slide underneath, I don’t really care.”
Growth in automation
In recent months, Meloche says Fori and other automation companies have seen more interest from aerospace companies for automation systems. Instead of being asked to take over simple material handling or work-moving functions, requests for proposals have begun encompassing major assembly steps.
“Robotic drilling is getting much bigger. There’s a lot of drilling that takes place on an aircraft, and automation promises precision and repeatability. They used to manually set up each drill fixture. Now, they’re using gantry-mounted robots or mounting robots to AGVs,” Meloche explains. “Twenty years ago, robots were not used much in aerospace, but we’re seeing them now for drilling, for sealing, for part handling, for positioning, and even for painting. We’re seeing applications where they’re looking at putting robots on different types of AGVs to move around the vehicle and paint the plane.”
As those requests come in, he says it’s getting easier to mention work with Chrysler, Ford, and other automakers – partly because Fori is starting to see a lot of familiar faces in aerospace industry engineering departments.
“During the downturn of the economy, a lot of these automotive engineers started filtering out into aerospace companies,” Meloche notes. He adds that companies are a bit more receptive to learn from automotive suppliers because many aerospace engineers have seen automotive automation in action, and “we offer them a different view on things.”
Fori Automation
www.foriauto.com
About the author: Robert Schoenberger is an editor at Aerospace Manufacturing and Design and can be reached at 216.393.0271 or rschoenberger@gie.net.
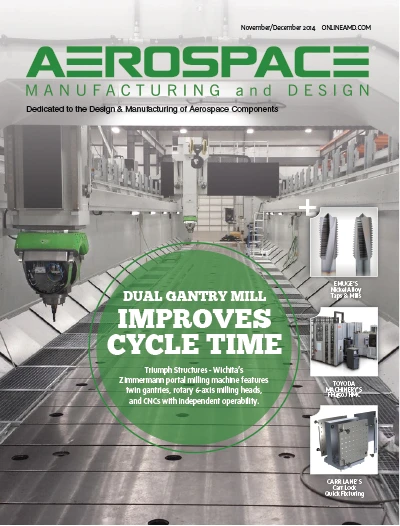
Explore the November December 2014 Issue
Check out more from this issue and find your next story to read.
Latest from Aerospace Manufacturing and Design
- Electra raises $115M to pioneer Ultra Short aircraft
- Walter’s WT26 partial- and full-profile thread turning inserts
- April Manufacturing Lunch + Learn with Iscar
- April Manufacturing Lunch + Learn with Insaco
- Archer unveils vision for New York air taxi network
- Siemens launches its machine tool digitalization software portfolio MACHINUM in the US
- #58 - Manufacturing Matters - 2024 Metrology's Latest Advancements with Starrett
- Strategies to improve milling and turning for medical components