One of the largest combination abrasive waterjet cutting and CNC milling platforms in the world made its debut in early 2013 at the Advanced Manufacturing Research Center (AMRC) with Boeing in northwest England.
A partnership between the private sector and the University of Sheffield’s faculty of engineering, AMRC’s focus is to investigate new techniques to make machining processes more environmentally friendly, energy-efficient, and cost effective. Toward this end, the AMRC was seeking 5-axis waterjet cutting and 5-axis machining where both processes needed to be on the same cross-beam of a machine and the part not to be moved.
The winner of the competitive bid to design and create this machine was WARDJet, based in Tallmadge, Ohio. Designed to AMRC specs, the GCM model waterjet installed at the research center is based on the company’s existing G Series, which features a 20ft crossbeam and 5ft Z-axis travel. In the GCM (composite manufacturing) version, the cutting envelope is split, with one section having a standard waterjet tank, leaving the remainder of the cutting envelope open to allow very large parts to be mounted onto the floor.
A Strategic Decision
Being chosen to provide the large waterjet cutting equipment to the AMRC gave Richard Ward, the American company’s founder and owner, the impetus to develop large-scale waterjet capability for commercial customers as well as for research. Ward’s reason for bidding on the AMRC project originated, in part, from the desire to gain credibility with large corporations. “We needed something to help us understand the market, gain an accelerated path to knowledge and documentation as well as safety and certifications,” Ward says.
“Joining AMRC was a strategic decision to help us leap-frog to this position, and that it has,” Ward explains.
Since WARDJet was chosen to provide the large waterjet, Ward has been appointed to AMRC’s board of directors, joining representatives from other partners including Boeing, BAE Systems, Messier-Bugatti-Dowty, Rolls Royce, Mori Seiki, Haas, Carpenter, and Sandvik.
Commercial Benefits
The combination of capabilities on a large scale demonstrated on the AMRC machine has proven to be appealing with WARDJet’s commercial customers as well. The company’s latest order for a GCM from a Pennsylvania-based manufacturer has a footprint of 60ft x 40ft, 26ft high and 5ft vertical travel, offering a cutting envelope of 48ft x 16.5ft. This particular machine is designed to take multiple crossbeams with combinations of waterjets or waterjet and milling. “The ability to put a large part under the machine and use the ideal process, be it milling or waterjet cutting, is appealing,” Ward explains.
“Waterjet cutting does not impart the huge forces experienced when milling, so it is not necessary to hold the part as securely as milling,” Ward continues. “Finding a mix of fixtures that allow both to be done efficiently is important.”
One of the keys to building custom machines is to use as many tried-and-proven modular components. “Even though a machine may look completely different to another, most of the parts are modular, making the design, build, installation, tech support, service, and warranty easier,” Ward adds.
Combined Capabilities
Ward is especially enthusiastic about how waterjet technology benefits the aerospace market, particularly in working with composites. “Waterjet cutting and milling both have their place in composites, each excelling in specific areas,” Ward says. “By having a combination system, the best of both worlds can be achieved.”
Options for additional tool heads expand the capabilities available, namely drilling, reaming, tapping, thread milling, inkjet printing including bar codes, logos, and part numbers, dot-peen marking, and 5-axis height/crash sensors for continuous adjustment while bevel cutting.
Ward sees another trend that involves metrology and the ability to use the machine’s CNC gantry as a giant CMM. “This will revolutionize how parts are programmed, signed off, and accepted into the aerospace world, reducing costs and time,” he says.
“Waterjet cutting can be very accurate – we have customers claiming to hold ±0.001" on their parts,” Ward says. “Even though the machines are built to very high placement and repeatability accuracies, the waterjet process itself adds variance to the finished part,” he notes. “We typically recommend tolerances of ±0.003" to ±0.005" be considered as relatively easy to attain, but this again depends on material, thickness, etc.”
Virtually every material can be eroded away by abrasive waterjet, and various options exist on how to increase cutting capacity, speed, quality, and accuracy. “Waterjet is by no means the ideal solution to every situation,” Ward allows. “But, waterjet is amazing in composites, high-nickel alloys, and some of the unpronounceable aerospace and nuclear materials being developed,” he adds. “Testing is a quick and easy way to establish if waterjet cutting is the process of choice.”
As further proof of waterjet’s applicability to manufacturing precision components is needed, it is worth noting that WARDJet uses its own waterjets to cut parts made in the company’s own machines. “Without waterjets, we wouldn’t be in business,” Ward stresses. “We just couldn’t do it.”
An American Success Story When Richard Ward, a native of Rhodesia (now known as Zimbabwe), graduated with a civil engineering degree from the University of Cape Town in South Africa, he returned to a homeland wracked by civil war. The government was printing money so quickly, the resulting hyper-inflation wiped off 30 zeroes of value from incomes and pension funds. Ward was fortunate to find a 2-year position in the United States, where he set to work designing a waterjet for cutting stone. Ward recounts, “I realized I’d like to stay in America, and if I wanted a chance to get ahead it was unlikely as a civil engineer.” With only $600, he sold his car to raise capital, and set up business in his garage. His first desk was a bedroom door taken off its hinges and propped up on upended plastic garbage cans. His wife, Helen, sat across from him to answer the one phone. Almost two decades later, he remains the sole owner of the company he founded, WARDJet, which now has 60 employees. |
WARDJet Inc.
Tallmadge, Ohio
www.wardjet.com
About the author: Eric Brothers, senior editor, can be reached at ebrothers@gie.net or 330.523.5341.
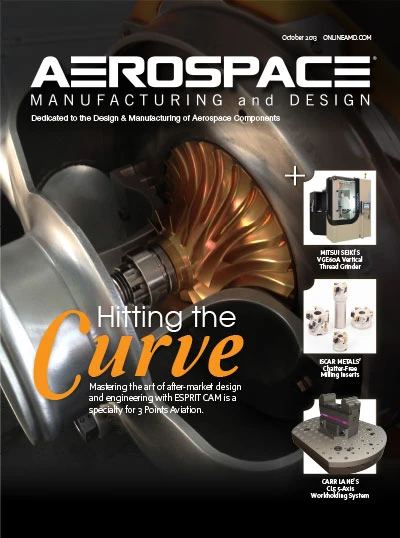
Explore the October 2013 Issue
Check out more from this issue and find your next story to read.
Latest from Aerospace Manufacturing and Design
- Trelleborg acquires Aero-Plastics
- Industrial automation products, enclosed encoders
- #61 - Manufacturing Matters: CMMC roll out: When do I need to comply?
- AIX shows aircraft interiors are a strategic priority for global airlines
- Machine Tool Builders Roundtable: Turn equipment into expertise
- No time to waste: How to machine MedTech parts more efficiently
- The 5 Best and Fastest Spindle Repair Services
- Mill smarter, not harder: How collaboration optimizes production