Rapid market growth outside North America and Europe is driving globalization of the aerospace industry. To grow market share and remain competitive, manufacturers must deliver a quality product to their customers at minimum cost. This requires companies to constantly innovate and embrace technological advances.
The ability to provide a sustainable combination of technological progression and cost maintenance has allowed companies with a history of precision manufacturing to set themselves apart in a growing crowd. Weatherford Aerospace, which specializes in chemical treatment and material machining for the aerospace industry, has embraced technological evolution while remaining true to the methods that have driven the company to success.
Founded in 1973, Weatherford Aerospace began as one of just a handful of independent companies that employed chemical milling of airplane components. In the years since, the company’s expansion into fabrication, anodizing, and painting aircraft parts drove steady growth. Today, the company operates two production facilities with 160,000ft2 of manufacturing space and is in the process of expanding one of the facilities by another 23,000ft2. Its production processes are focused on increasing throughput and maximizing equipment efficiency to ensure on-time deliveries and competitive prices without compromising quality.
Stringent Requirements
Chemical milling, though a simple process, is encumbered with subtle control requirements that require constant attention. Weatherford Aerospace staff’s years of experience, coupled with advanced machinery and tools, has rendered this process to standard practice. By aligning this experience and technology, the employees at Weatherford can produce high-quality parts that meet strict industry standards and governmental requirements, such as ITAR and REACH compliance, DFARS regulations, and RoHS requirements – all within tight schedule constraints.
According to Iona Tull, who oversees quality assurance technical data at Weatherford, two Ohaus triple beam balances operate among the equipment used in the milling process. Although less complex than the high-tech milling machines, the balances are used to regularly assess the concentration of each chemical etchant. This guarantees process engineers meet the design specifications and industry requirements for every individual part. Each type of metal requires a different chemical etchant, and achieving the proper solution content is critical to consistent performance as it controls the speed, amount of undercut, or sideways etch. Simultaneously, an inaccurate batch of etchant can lead to costly rework, requiring additional blanks to be etched, alongside additional production time.
“Incorporating the Ohaus balances into our production process has allowed us to quickly and accurately measure the tank constituents, providing us with the confidence to continuously run parts without worrying about any inconsistencies,” Tull says. “Their ability to measure minute quantities of material and provide fast stable readings, as well as their rugged construction – which withstands rigorous daily use – makes them an invaluable part of our production process.”
In an environment of declining spending, it is critical that aerospace companies routinely analyze the overall efficiency of equipment being used to boost throughput. The utilization of precision equipment such as the Ohaus triple beam balances can help to increase performance and user productivity on the manufacturing floor by reducing the risk of errors and minimizing operation time. By helping to ensure that the end products meet quality requirements, these tools also increase revenue and reduce operational costs.
The mechanical triple beam balance, which provides unwavering accuracy and stability that cannot be replaced or replicated by high-technology machinery, continues to be the backbone of operations. A combination of technological innovation in milling, tried-and-true traditional equipment such as the Ohaus triple beam balance, and years of experience, will continue to allow Weatherford Aerospace to serve its customers and grow its market share.
Ohaus Corp.
Parsippany, N.J.
www.Ohaus.com
Weatherford Aerospace
Weatherford, Texas
www.weatherfordaerospace.com
About the author: Carl Joslyn is channel marketing manager for Ohaus and can be reached at carl.joslyn@ohaus.com.
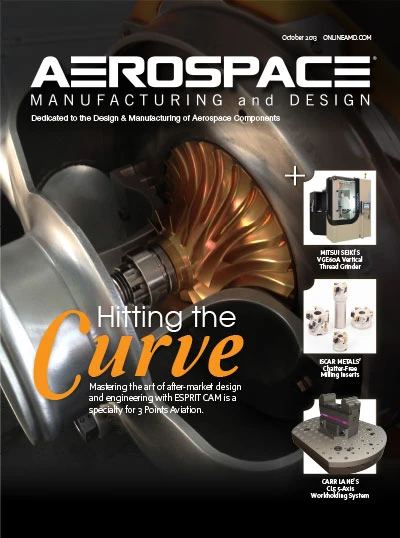
Explore the October 2013 Issue
Check out more from this issue and find your next story to read.
Latest from Aerospace Manufacturing and Design
- Cyient Group, Deutsche Aircraft finalize multi-year contract
- High surface quality at high speed
- #57 - Manufacturing Matters - Agile & Robust Supply Chain Management with Lisa Anderson
- Take control of your manufacturing business despite supply chain turmoil
- Strengthening the defense maritime industrial base for national security, economic resilience
- Register now to learn solutions for high-temperature aerospace machining challenges
- Expertise on machining, joining offered in April’s Manufacturing Lunch + Learn
- NASA offers free high school engineering program this summer