According to the Manufacturers Alliance for Productivity and Innovation (MAPI), the U.S. industrial outlook for 2013 will show modest growth throughout the year. However, it might not be until midway through 2014 that the economy will start to grow at a moderate rate. Ultimately, this is good news. With only slight growth predicted for the immediate future, industrial manufacturers must look for ways to increase productivity and throughput to support that anticipated growth while maximizing overall efficiency to keep operating costs down. The question is: How can industrial manufacturers meet higher demand without increasing overhead?
Common industrial processes, such as surface finishing, are a good place to start. Surface finishing uses various non-woven abrasive products to change or improve the surface of a manufactured product to achieve a desired property. For example, surface conditioning discs can remove marks, burrs, and other surface imperfections that occur during machining. These products can also be used to enhance performance, increasing adhesion, solderability, and durability, as well as resistance to corrosion, tarnish, and industrial chemicals.
Across key manufacturing processes of various industries, from aerospace and transportation, to energy and maintenance repair operations (MRO), and metal fabrication, recent advances in surface conditioning technology now allow for additional manufacturer benefits. Using enhanced non-woven abrasives technology, industrial manufacturers can improve overall operational efficiency to achieve desired higher productivity and throughput, while also reducing time and labor requirements.
Next-Gen Non-Wovens
Materials science expertise and innovations in product design have combined to yield improved abrasives technology, including surface conditioning discs that feature a non-woven substrate impregnated with an aluminum oxide aggregate grain, patent-pending smear-resistant resin chemistry, and three-dimensional construction. These unique features provide high abrasive content for continuous cutting on soft and hard metals alike for excellent surface finishing of steel, nickel, alloys, and other materials, while an open web structure resists loading on softer metals like aluminum. This technological breakthrough provides upwards of four times the performance in cut rate and surface coverage. Comparisons show a longer useful life, consistent cut rate, and superior finish from beginning to end (Chart 1). This enables industrial operations to reduce or eliminate steps in a surface improvement process for more throughput without additional resources and for better cost positioning.
For more challenging applications, such as heavy scale removal and stone or granite cleanup, other technological advances within quick-change stripping and blending discs that feature a ceramic alumina long-lasting grain and advanced resin bond provide twice the life of conventional surface conditioning products. This durable design results in a high-performance product that will not shed on rust-covered pieces. Extremely versatile, this allows for multiple operations using one disc, from medium grit surface conditioning to more challenging strip and clean jobs. The innovative disc material is not only stiff enough for challenging applications, but also soft enough to prevent gouging that can necessitate rework. An open web structure does not load on coatings, adhesives, or softer metals and, when used to deburr, the discs will not snag or shed like lantuck or fiber discs. This new technology allows for improved cycle times, abrasive life, and overall cost-per-part savings compared to traditional aluminum oxide removal products.
Performance in the Field
Aerospace
For aerospace manufacturing, advanced surface conditioning products can be extremely useful for blending and deburring applications involving airframes and investment-cast parts. By simplifying the process, aerospace manufacturers are now able to reduce cycle times, enhancing productivity and efficiency.
MRO/Metal Fabrication
Finally, MRO and metal fabricators can use these recent innovations in surface conditioning for various applications, including blending, deburring, and weld blending, surface preparation prior to painting, rust and paint removal, and surface prep prior to blending. As a rule, MRO and metal fabricators are under steady pressure to reduce downtime and costs. With new options offering enhanced performance, they can effectively increase productivity while reducing labor requirements.
While analysts are predicting a slight increase in industrial manufacturing in the year ahead, that growth is said to be sluggish, which means that manufacturers need to prepare themselves for best- and worst-case scenarios, allowing themselves to meet increased demand while keeping a close eye on overall operational costs. Key industries, such as aerospace, transportation, energy production, MRO, and metal fabrication all have one thing in common – they all use surface conditioning during the manufacturing process. Recent advances in surface conditioning technology have made this is a great area to cost-effectively increase productivity. Innovative design and materials science have combined to yield a new generation of high-performance surface conditioning products that are durable, flexible, and easy-to-use. As the economic landscape begins to show signs of improving, industrial manufacturers need to utilize this new surface conditioning technology to help meet increased growth, while streamlining their manufacturing operations in order to remain competitive in unstable economic times.
Watervliet, N.Y.
www.nortonbeartex.com
About the author: Paul Krupa is a senior product manager – technical non-woven abrasives at Saint-Gobain Abrasives and can be reached at paul.a.krupa@saint-gobain.com. Krupa is an abrasives industry expert with extensive product experience in non-woven materials, conventional light- and heavy-weight papers, abrasive grains and resins, and sanding sponges.
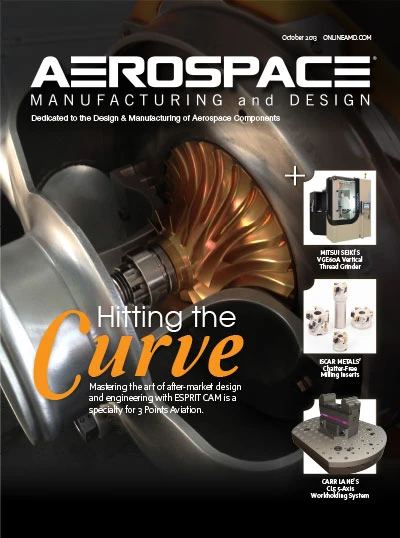
Explore the October 2013 Issue
Check out more from this issue and find your next story to read.
Latest from Aerospace Manufacturing and Design
- Cyient Group, Deutsche Aircraft finalize multi-year contract
- High surface quality at high speed
- #57 - Manufacturing Matters - Agile & Robust Supply Chain Management with Lisa Anderson
- Take control of your manufacturing business despite supply chain turmoil
- Strengthening the defense maritime industrial base for national security, economic resilience
- Register now to learn solutions for high-temperature aerospace machining challenges
- Expertise on machining, joining offered in April’s Manufacturing Lunch + Learn
- NASA offers free high school engineering program this summer