Crane Aerospace’s mission-critical products protect the safety of millions of airplane passengers. Because of this, the company must meet stringent government safety regulations that help to guarantee that these products will perform as expected under a broad range of real-world conditions.
Crane is an industry leader in aircraft braking systems, with 65% of the commercial market and 85% of the Western military market. The company has more than 25,000 systems in service worldwide today. These braking systems are critical in ensuring passenger safety during routine landings, as well as during rejected (or aborted) takeoffs, which pose special challenges because a plane has a higher speed and heavier weight at takeoff than during landing; furthermore, it has already used up much of the available runway. Braking systems designed and manufactured by Crane include a number of mechanical and hydraulic parts, such as control valves, pumps, and actuators. However, the most complex component is an invisible one: the thousands of lines of software code that deliver efficient, reliable brake control when required.
To support reliable software performance, the United States Federal Aviation Administration (FAA) has drafted a set of rules under its Federal Aviation Regulations requiring proof that software “performs intended functions under any foreseeable condition.” A means of compliance with this law – that is, a way to show the system meets this requirement – is a standard called DO-178B, Software Considerations in Airborne Systems and Equipment Certification. This document aims to assure software performance by defining a set of verification, requirements management, and quality assurance tasks aimed at instilling rigor into the software development process.
Essentially, DO-178B requires developers to test and verify the performance of control software under a broad range of operating conditions – a challenging engineering task. Since 2010, Crane Aerospace has relied on SCADE Suite software from Esterel – now a part of ANSYS – to manage software development, as well as the critical FAA certification process, for its braking control systems.
New Complexity, New Challenges
Since Crane introduced its first Hydro-Aire antiskid braking system to the aerospace industry, braking controls have become increasingly complex. Wheel speed transducers measure high-resolution wheel speeds, enabling modulation and control of brake pressure across all surfaces. Adaptive controls have increased the responsiveness of brakes to wet or dry conditions. Microprocessors have applied sophisticated control algorithms to automate braking and achieve performance in excess of 90% across all operating conditions. Brake-by-wire systems, which control brakes digitally, have become industry standard since Crane engineers developed them for the U.S. Space Shuttle program in 1973.
Today, while the basic mechanics of braking have not changed, brake control systems have grown into an incredibly complex blend of control software, electronically controlled actuators, and digital interfaces with other onboard systems. Based on human signals and other inputs, advanced software controls the application of antiskid technologies for braking systems. In the event of an electrical short or other unexpected event, the software not only ensures continuing brake performance, but also sends an automatic alert to maintenance staff so that they can address the problem upon landing. Obviously, the underlying code is mission critical, because the consequences for brake failure are truly catastrophic.
This new complexity has created exceptional challenges for software developers, who must test for each input to the brake control software – as well as for a broad range of operating events. This dictates extremely rigorous, broad-scope testing and verification tasks, even as customers are working against very aggressive development schedules.
Prior to 2010, the company’s software engineers managed the requirements of DO-178B via a time- and labor-intensive process, which had some evident drawbacks. Because of the process’ manual nature, the finest details of functionality were hidden in the underlying code until the software was plugged in and running. The impacts of customer requirements and system updates were not fully visible – and thus could not be verified by the engineering team – until the software was fully developed and implemented.
There were often surprises when software was run in an in-house testing facility or customer lab replicating actual aircraft configuration, which meant that Crane’s engineers had to go back to the drawing board and rewrite the code. This was an expensive and time-consuming proposition at such a late stage of software development, especially after hundreds of development hours had been invested.
The resulting high costs, large amount of rework, and scheduling issues negatively affected the company’s customer satisfaction levels. In addition, the engineering team had to assemble a wealth of documentation at every stage to satisfy FAA requirements. To accelerate and streamline the software development process – without sacrificing ultimate product integrity or regulatory compliance – engineers realized that they needed to identify an advanced technology solution that would model and predict real-world performance of these smart systems at a much earlier stage.
Putting the Brakes on Manual Work
Crane engineers evaluated a number of model-based development environments before choosing SCADE Suite. They selected it because it is a purpose-built software development tool qualified to meet the standards of DO-178B up to Level A, the highest safety tier for the aerospace industry. In addition, engineers were impressed by the level of support that they would receive from Esterel while installing and running SCADE solutions.
Since implementing SCADE Suite in 2010, Crane Aerospace has realized significant cost, speed, and efficiency benefits in its safety-critical software development, verification, and validation processes. From the earliest stages of code development, the SCADE Suite tool enables software engineers to simulate and confidently predict real-world results, eliminating surprises and rework at later stages. SCADE Suite automates the code-generation process and enables testing embedded software code against thousands of inputs. This significantly reduces the need for manual work involved in code generation as well as related software development, verification, and validation tasks.
During software simulations, SCADE Suite allows the engineering team to subject their design to thousands of inputs and events – such as electrical shorts, system overloads, and unexpected human commands – to make sure that the software will function exactly as expected when installed in an actual plane.
SCADE Suite allows customers to build customized libraries of common code types and general-utility operators, which makes code generation even faster. Functional libraries bring primary and ancillary brake functions, as well as system interfaces, directly into the software development process. SCADE Suite generates much of the process documentation automatically, eliminating hours of work that once were invested in meeting stringent government requirements for record keeping.
Take Off
With the incredible pressures that aircraft framers face today, SCADE Suite has enabled Crane Aerospace to help its customers to meet tight budgets and schedules. Shortly after implementing SCADE Suite, Crane successfully used the software’s intuitive libraries and graphical models to meet a two-week turnaround for a scaled-down customer demo of a new control system.
Today, Crane is able to deliver on customer requirements, as well as meet the stringent demands of the FAA’s DO-178B guidelines, via a compressed development schedule. Day-to-day engineering work is much faster and efficient, and errors are detected at a much earlier stage.
In some cases, Crane’s customers have actually used SCADE Suite’s systems-level models and what-if simulations to consider enhancements to overall braking system prototypes during iron-bird testing, a dimensionally accurate structure specially fabricated to replicate the aircraft. In two short years, Crane has moved from a reactive stance to helping its customers lead the industry with forward-looking braking system technologies.
Finding Use from Nose to Tail In addition to safety and mission-critical software, simulation is used in the design of almost all the physical aspects of an aircraft. These include the engine, external aerodynamics, the passenger cabin environment, mechanical, electrical, and hydraulic systems, and the overall structural integrity of the airframe. Let’s take the aircraft wing as an example. Not only is the design of the wing critical for the aircraft to achieve its requirements (safety, range, passenger capacity, airport characteristics, etc.) but its aerodynamic performance contributes significantly to the fuel efficiency of the aircraft. Even small reductions in drag can mean significant fuel cost savings over a long lifecycle of a commercial aircraft. With fuel costs now making up a significant portion of an airline’s expenses, the aircraft design community is looking closely at wing optimization like the introduction of winglets on aircraft.
In addition, the structural integrity of the wing must be maintained. For example, can the wing structure safely withstand the loading experienced within the flight envelope and with the appropriate safety factors? How does this change with new materials such as composites? Finite element analysis is used extensively to optimize designs at a stage where the cost of making changes is minimal. A specific simulation tool called ANSYS Composite PrepPost is used for the rapid setup and assessment of complex composite material configurations. However, the aerodynamics and structural design do not happen in isolation. Coupling both aerodynamics and structural analyses together for a multiphysics simulation provides engineers with a deeper and more accurate view into wing performance. Phenomena such as buffeting and aeroelastic effects analysis (think of looking out the window at the wing and watching it flutter up and down during flight), where the aerodynamic characteristics are mapped to the structural model, help determine the total system response. As always in aircraft design, safety is the number-one priority. Icing on the wing and lightning strike are two environmental phenomena that can compromise the safety and performance of the aircraft. Despite the complexity of the physics involved, simulation has a role to play. CFD that includes multi-phase analysis is used to assess water and ice impact on the wing, and ensures that the de-icing or anti-icing system is designed so that any ice formation can be removed. Simulations are also used to study the thermal and electromagnetic impact of lightning strikes on aircraft, including the wing, to ensure that the appropriate mitigation technologies are designed. |
ANSYS Inc.
Canonsburg, Pa.
www.ansys.com
Crane Aerospace & Electronics
Burbank, Calif.
www.craneae.com
About the authors: Gregory Mooney (gregory.mooney@craneae.com) is a systems software engineering lead for landing systems at Crane Aerospace & Electronics, Burbank, Calif. Robert Harwood (robert.harwood@ansys.com) is an aerospace and defense industry director for ANSYS Inc.
WANT MORE?
Enter your email to receive our newsletters.
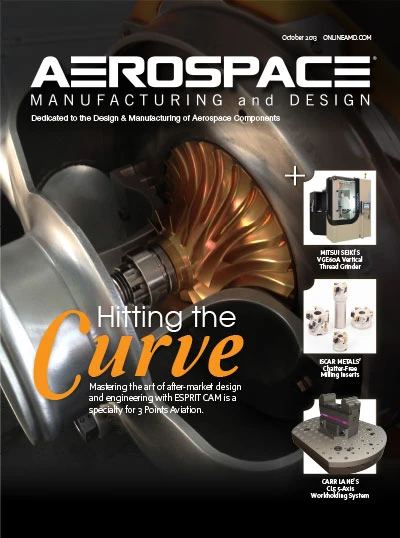
Explore the October 2013 Issue
Check out more from this issue and find your next story to read.
Latest from Aerospace Manufacturing and Design
- Cyient Group, Deutsche Aircraft finalize multi-year contract
- High surface quality at high speed
- #57 - Manufacturing Matters - Agile & Robust Supply Chain Management with Lisa Anderson
- Take control of your manufacturing business despite supply chain turmoil
- Strengthening the defense maritime industrial base for national security, economic resilience
- Register now to learn solutions for high-temperature aerospace machining challenges
- Expertise on machining, joining offered in April’s Manufacturing Lunch + Learn
- NASA offers free high school engineering program this summer