Precision grinding applications are an effective way to meet the challenging requirements – such as tight tolerances, intricate geometries, and high-quality surface finish demands – of today’s aerospace and defense industry. With difficult-to-grind materials such as titanium, Inconel, and stainless steel 316, and with part sizes varying widely, grinding machine and wheel manufacturers are stepping up with new technology and solutions.
Vitrified grinding wheels are the primary products for these precision grinding applications and have two major components: abrasives and bond. Norton Abrasives invented the process of firing precision wheels in the 1880s and while process improvements and materials have evolved to improve performance and consistency, the basic technology has not changed. The abrasive portion of the wheel cuts, while the vitrified or glass bond is the material that holds the abrasive grain together. A hard wheel has a heavier bond-to-grain ratio and requires more pressure to break down the bond to release new abrasive grain for cutting. The right balance of bond-to-grain will provide enough holding power for the grain to perform the stops, cutting, and starts without burning or damaging the work.
An All-New Bond Platform
Grain adhesion science is the chemistry of holding the abrasive grain in the bond matrix for the precise amount of time. Norton Abrasives has developed Norton Vitirum3, an entirely new abrasives platform that features an innovative bond technology, which promotes excellent grain adhesion. This bond features an exclusive chemistry that uses less bond to provide the same holding power, resulting in improved product versatility across a wide range of applications.
Cooler Cutting
The wheel’s low bond-to-abrasive ratio allows increased exposure of the abrasive grains for an improved cut rate and minimizes or eliminates the chance for burn, while reducing power consumption and grinding forces on the part. An increased porosity improves coolant flow and chip clearance to eliminate burn or other part damage, especially on tough-to-grind materials.
For example, at an MRR index of 200, Vitirum3 requires 15% less power to remove the same amount of material. This means less heat is generated on the workpiece, minimizing the chance for metallurgical damage. At a power consumption index of 3, Vitirum3 removes 20% more.
Precise Profile Holding
Wheel retention and radius accuracy is significantly improved with the stronger bond’s superior grain holding property. In aerospace applications requiring intricate part profiles, this precise profile holding offers better part geometry and integrity, less downtime for dressing, increased productivity, lower abrasive cost, and reduced dresser wear and dresser replacement cost.
Higher Speeds and Feeds
Many of today’s precision machines offer higher operating speeds to improve productivity, which requires manufacturers to provide wheels that are tested and rated for these higher speeds. A Norton Vitrium3 wheel is 20% stronger than a wheel made with a conventional bond, which allows softer grades to operate at higher speeds for faster stock removal, increased feed rates, and significantly increased production.
Reduced Grinding Forces and Energy Savings
The increased exposure of abrasive grains provided by Norton Vitirum3 reduces grinding force by up to 25%, lowering energy costs while decreasing workpiece deflection. In addition, working with higher feed rates, speed, and pressure significantly increases production while reducing wheel consumption. Norton Vitrium3 technology also requires a lower firing temperature than standard vitrified bonds, which reduces energy use.
Savings in Total Grinding Investment
Aerospace manufactures are concerned with reducing costs without sacrificing performance. While on average, abrasives consumables only account for about 3%, machinery and labor account for 58% of total manufacturing budgets. Vitirum3 technology provides a 20% or more decrease in cycle time per part, which will reduce the total machining, labor, and abrasives cost per part by more than 15%.
Norton / Saint-Gobain Abrasives
www.nortonabrasives.com
About the author: Jim Krause is with Norton / Saint-Gobain Abrasives and can be reached at jim.t.krause@saint-gobain.com.
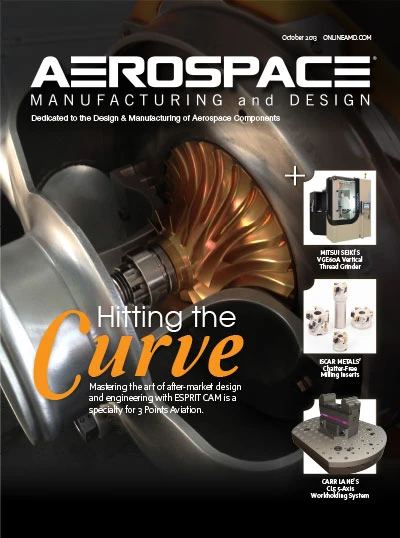
Explore the October 2013 Issue
Check out more from this issue and find your next story to read.
Latest from Aerospace Manufacturing and Design
- AIX showcases the future of air travel
- Sunnen Products' PGE-6000 gage
- #41 Lunch + Learn Podcast - SMW Autoblok
- Revolutionizing aircraft design without sacrificing sustainability
- GE Aerospace awarded subcontract for FLRAA next phase
- KYOCERA Precision Tools publishes 2025-2026 Indexable Cutting Tools Catalog
- BOC Aviation orders 120 Airbus, Boeing jetliners
- Mazak’s INTEGREX j-Series NEO