Metal removal rate (MRR) in metalcutting is a volume of chips removed in 1 minute, and it is measured in a three-dimensional quantity.
MRR is also a measure of productivity of metalcutting (milling, turning, and drilling). The accuracy in calculating MRR is very important.
Current formula (1) for metal removal rate (Q) when turning is based on the cutting speed (Vc), depth of cut (ap), and feed rate (f):
(Formula 1) Q = 12 Vc • ap • f (in3 / min)
There is another approach that defines volume of the chips to be removed. Such volume is based on the area of a circular ring of a cylinder and its length of cut.
Assume that a workpiece (cylinder with diameter D) is being turned at the depth of cut ap. After first pass, the diameter of this workpiece is D1 = D – 2 • ap. The formula for calculating the area of a circular ring or annulus is:
A = π (D2 / 4 – D12 / 4) (in2)
The length of the cut is a distance passed by the cutting tool in 1 minute, a.k.a. feed rate (L):
L = f • n (inches)
Where n is a spindle speed:
n = 12 Vc / πD (rpm)
The volume of chips removed (Q1) can be calculated by the formula (2):
(Formula 2) Q1 = π (D2 / 4 – D12 / 4) • f • n (in3 / min)
We performed various calculations and analyzed how the workpiece diameter, depth of cut, feed rate, and cutting speed affects the volume of chips.
As an example, the calculations were performed at the following constant parameters: depth of cut, feed rate, and cutting speed:
Depth of cut: ap = 0.20"
Feed rate: f = 0.020ipr
Cutting speed: Vc = 500sfm
Workpiece diameters (D) were: 1.0", 2.0", 3.0", 4.0", and 5.0". Metal removal rate (Q) was calculated by the currently used formula. Related parameters such as length of cut (L) and spindle speed (n) were calculated for each of selected workpiece diameters. The results of calculation are shown in Table 1.
Calculated volume of chips removed (Q1), the area of a circular ring or annulus (A), the length of the cut, a.k.a. feed speed (L), and the spindle speed (n) are shown in Table 2.
As can be seen from the tables, the difference between Q and Q1 decreases when diameter of the workpiece increases. The maximum difference in the volume of chips removed is 25.0% and the minimum difference is 4.3%.
The author asks all readers to join the discussion on Formula 1 and Formula 2 for calculating the metal removal rate. If Formula 2 provides accurate data of MRR, it will replace Formula 1. That change will increase manufacturers’ productivity of cutting. Feedback on this discussion can be directed to edmundisakov9701@comcast.net
About the author: Dr. Edmund Isakov is known for his work in research, development, and applications of the cutting tools for milling, turning, and boring. During 18 years at Kennametal Inc. and 12 years of consulting work, he became a noted authority on cutting tool performance and analysis. Isakov is the author of three books, several calculators, and numerous articles.
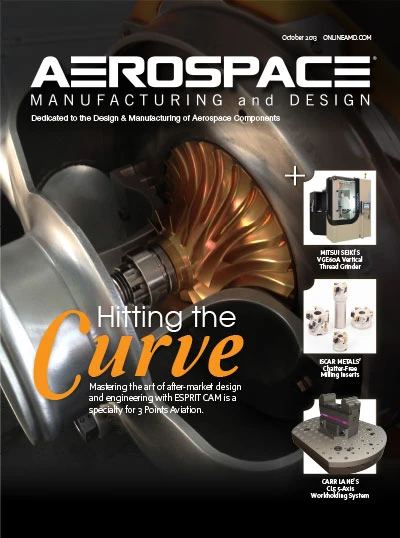
Explore the October 2013 Issue
Check out more from this issue and find your next story to read.
Latest from Aerospace Manufacturing and Design
- JetZero all-wing airplane demonstrator achieves milestones
- Cermet indexable inserts for medium turning operations
- Trelleborg acquires Aero-Plastics
- Industrial automation products, enclosed encoders
- #61 - Manufacturing Matters: CMMC roll out: When do I need to comply?
- AIX shows aircraft interiors are a strategic priority for global airlines
- Machine Tool Builders Roundtable: Turn equipment into expertise
- No time to waste: How to machine MedTech parts more efficiently