Sensors with increased capability enable manufacturers to drive significant improvements in process and plant efficiency, product quality, and safety. But, while an increasing number of organizations are recognizing the need to implement more sensors – or more capable sensors – within their processes and facilities, deployment often proves challenging.
There are several potential challenges to increased sensor deployment. Most facilities have an existing process and physical layout, where modifications to add additional sensor capabilities could have significant impacts to safety, time, and cost – all of which can negatively affect both production and the projected return on investment from the sensor program.
It is often difficult to deploy sensors without shutting down an existing process. Practical considerations include availability of power to operate the sensor, as well as how to transmit the signal from the sensor back to a local or plant-wide monitoring system. Installing new power supply points and signal cabling to support sensor implementation can also be a significant and costly undertaking.
The Wireless Connection
Wireless sensors – and wireless sensor networks in particular – are seeing rapid uptake in manufacturing and industrial facilities. According to analysts at MarketsandMarkets, the global industrial wireless sensor networks market will grow by almost 16% annually to reach $3.8 billion by 2017, with WirelessHART, ISA100.11a, and 6LoWPAN being the major technologies employed, as well as IEEE 802.11, ZigBee, Bluetooth, and cellular (GPRS, GSM, and CDMA).
A wireless sensor network consists of nodes, which can range from a few to several hundreds or even thousands, with each node connected to one or several sensors. This model provides a practical solution for bridging information systems and the physical world. One of the major potential benefits is that a large number of individual wireless sensors often can be monitored using a single display device, or with a wide variety of fixed base stations and hand-held readers that are already available.
Wireless solutions are shown to reduce installation costs and sensor installation times dramatically. They also increase safety levels because they often can be configured remotely or prior to installation, and swapped out easily for calibration, cleaning, and maintenance. Conversely, the more permanent a sensor installation, the more costly the maintenance requirement tends to be.
Since a variety of wireless solutions using different communication protocols are now available, it is worth noting that mixed installations can be more difficult to manage, where these different standards are employed. A solution based on an open format, license-free wavelength is preferred, to ensure that it does not compromise other systems using wireless standards such as WiFi and Zigbee. These standards are often found within manufacturing and industrial facilities and are employed to reduce the challenges and costs of implementing proprietary solutions. Moreover, a solution that combines both wireless data transmission and battery operation with low power consumption is preferable, as this eliminates many of the potentially disruptive aspects of sensor installation and operation commonly associated with wired solutions.
One example is the wireless radio telemetry inclinometer, which is seeing growing adoption in the manufacturing sector as it is ideal for permanent angle measurement installations. It is also well suited for troubleshooting or checking the accuracy of angle measurements and alignments occurring across the production environment.
Similarly, wireless sensors measuring flow, pressure, or temperature are proving ideal for process troubleshooting, in scenarios where manufacturers wish to monitor performance of a process in a specific area for a short time and then move on to another location until the problem is identified. Here, the mounting scheme for the sensor is a consideration, since a temporary mounting scheme (where the sensor can be used and then removed easily) ensures a fast, efficient, and robust install.
Continuous Improvement
One of the most vital roles for sensor technology is in providing the data necessary to enable manufacturers to realize a new level of production capability. Data acquisition and analysis has become central to enabling the culture of continuous improvement and lean manufacturing to which the majority of companies now aspire. Continuous improvement not only allows them to enhance productivity and free up capacity, but also serves as a foundation for driving innovation and growth.
The aircraft industry, for example, is continually looking to develop new composite materials offering viable alternatives to aluminium, titanium, and steel. This requires raw-material production methods and manufacturing processes at different conditions to those used traditionally, which is driving adoption of more capable sensors and instrumentation throughout the production process – and also in areas where they were not employed previously.
In another example, metal processing, particularly the steel industry, is becoming more capital-intensive, driven by concerns regarding energy consumption, emissions, and new standards and regulation. Increased use of sensors allows a manufacturer to better control and analyze emissions, improve operational efficiency, and adhere to best practices, standards, and regulations.
About Sherborne Sensors Sherborne Sensors designs, develops, manufactures, and supplies of high-precision inclinometers, accelerometers, force transducers and load cells, instrumentation, and accessories for civil engineering, industrial, military, and aerospace customers. Products are supplied under the AS9100C Quality Accreditation and are intended for high reliability and long life. Sherborne Sensors’ acquisition of synergistic technologies within its product portfolio expanded the company’s product lines, adding the benefits of engineering support; global sales presence; repair, refurbishment, and calibration services; stocking programs; and continuous product improvement. |
Analysts at Frost & Sullivan valued the market for sensors in the metals industry at $600 million to $650 million in 2011 and noted that the market was growing rapidly, with advancements in sensing and instrumentation and the agility with which steel makers adopt and implement these improvements expected to have a significant positive impact on their operations.
Even sensor manufacturers themselves can benefit from advances in sensor technology to improve their processes and realize new levels of production capability. Sherborne Sensors, for example, has a highly capable calibration system that has been in commercial operation for many years. It was upgraded recently using several types of sensors in order to deliver new levels of precision required by increasingly demanding customer applications.
Enhancing Old and New
Acquiring data about processes and equipment is relatively straightforward using a well-implemented program of sensors. Programs of continuous improvement and initiatives to reduce power and carbon footprints are key drivers for sensor adoption. The opportunity to consider extending the commercial life of fully depreciated plant and machinery by retro-fitting them with sensors can be significantly less costly than building a new facility, which may not even be viable commercially in today’s restrictive regulatory environment.
Manufacturers might also be able to lower operating costs through sensor implementation and upgrade. For example, by closely monitoring the performance of plant equipment and product specifications, manufacturers can implement predictive maintenance activities that ensure these costly procedures are conducted only when necessary. They may also be able to identify and address potential issues before they occur. Such an approach helps to avoid costly unscheduled downtime, as well as excessively proactive maintenance schedules.
Similarly, for a relatively modest investment in equipment and retrofit of more capable sensing devices, manufacturers can:
- Efficiently use raw materials to increase production volume;
- Reduce lead times;
- Improve product quality; and
- Expand the range of products they are able to produce.
The implementation of more capable sensors and wireless solutions can also be of benefit at greenfield sites. The initial capital outlay for the sensors would be offset by lowered future operational and maintenance costs, while the plant operator would have greater production flexibility as the plant ages and production requirements change.
The use of wireless sensors almost always enhances the benefits of an expanded sensor program, due to the reduced costs associated with the installation and ongoing maintenance of the sensors themselves.
As sensors that are more capable are deployed, the opportunity exists for manufacturers to find even more efficient and effective ways to acquire data, analyze the vast volumes being stored, identify areas for improvement, and most importantly, act on the intelligence they provide.
Sherborne Sensors
Wyckoff, N.J.
www.sherbornesensors.com
About the author: Jesse Bonfeld is VP of Business Development with Sherborne Sensors and can be reached at info@sherbornesensors.com.
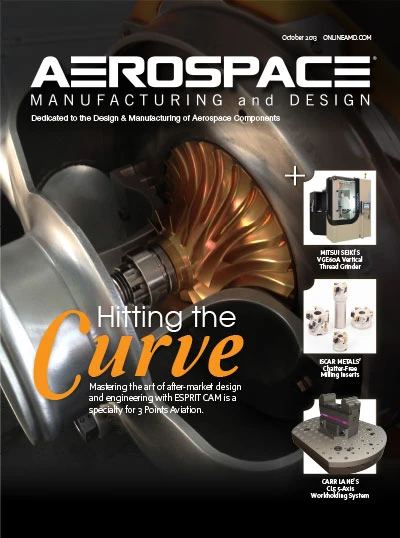
Explore the October 2013 Issue
Check out more from this issue and find your next story to read.
Latest from Aerospace Manufacturing and Design
- Cyient Group, Deutsche Aircraft finalize multi-year contract
- High surface quality at high speed
- #57 - Manufacturing Matters - Agile & Robust Supply Chain Management with Lisa Anderson
- Take control of your manufacturing business despite supply chain turmoil
- Strengthening the defense maritime industrial base for national security, economic resilience
- Register now to learn solutions for high-temperature aerospace machining challenges
- Expertise on machining, joining offered in April’s Manufacturing Lunch + Learn
- NASA offers free high school engineering program this summer