“Say it, do it, prove it” – the motto of Advanced Materials Technologies LLC, Phoenix, Ariz. – has been demonstrated time and again as the company grew from a four-person machine shop in 1983 to a business of 150 employees in 1996, was sold, renamed, and ultimately reinvented in 2011. Originally specializing in cold section repairs on small gas turbine engines, the company’s revitalization is largely due to the efforts of Jay Donkersloot, AMT’s owner. Of course, he’s had help along the way, from dedicated employees, customers, and machine-tool suppliers that have allowed AMT to continue to expand its capabilities reliably and so quickly.
Donkersloot, who had worked in a machine shop while in high school and for more than 20 years afterward, was pursuing unrelated business interests in 2009 when a friend asked him for help at a local aerospace machine shop. The experience made Donkersloot realize that he was missing an opportunity, so he rebooted his former company, Advanced Materials Technologies, using a nearly identical name, changing only the final “Inc.” to “LLC.”
Starting over with two people and a few machines in 2011, Donkersloot expanded the operation to its current 34 people and 15 CNC machines. Within one year, the company was ISO9001:2008/AS9100 Rev. C registered for machining aerospace components, and shortly thereafter, certified as a Federal Aviation Administration repair station for engines and accessories.
Core Work
AMT’s principal business, according to Donkersloot, is CNC machining, CNC wire and sinker electrical discharge machine (EDM) work, electron beam welding, vacuum furnace heat treating, brazing, TiG welding, and airflow measuring of turbine engine components.
The reasons for incorporating EDMs were straightforward. “We had the workload and the demand, and in order to control deliveries, we brought the process in house,” Donkersloot says. He’s since added a CNC hole popper to the EDM equipment roster.
A Brief History of Advanced Materials Technology LLC 1983: AMT Inc. starts with four employees; does cold-section turbine repairs 1984: Jay Donkersloot joins the firm as a CNC machinist 1986: Jay is named GM; AMT adds hot-section component repair 1992: Jay buys company from owner; employees number 30 1996: Company grows to 150 employees; includes full metallurgical lab 1996: Triumph Group buys firm, renames it Triumph Engines Tempe 2002: Jay leaves Triumph 2011: Jay opens AMT LLC with 2 employees 2012: AMT registered AS9100 Rev C 2013: AMT certified as FAA Repair Station; has 34 employees |
The EDMs are used for manufacture or repair of turbine disks, shroud segments, turbine blades, and turbine nozzle vane segments. Due to accuracy and finish requirements, AMT purchased the Sodick AG60L CNC Sinker EDM and AG600L Wire EDM, and then added a Sodick AQ750LH Wire EDM last spring.
Donkersloot explains there was more to the decision to choose the Sodick EDMs. “After looking at other brands, we liked the Sodick control system and their 10-year guarantee on positioning accuracy.” He says of his experience dealing with Sodick: “They have been fantastic, from the service and installation, through engineering support and trouble shooting, helping with complex programming.”
These are reassuring words to Kevin Savage, owner of Savage Machine Tools, Gilbert, Ariz., and the regional Sodick dealer.
“Jay and I have been working in the industry for more than 25 years,” Savage says. “He made an inquiry after hearing positive feedback about Sodick from various sources.” Before Donkersloot purchased his first EDM, the Sodick AG60L, the two visited a well-respected local shop that had a similar model. Savage adds that in the process, Donkersloot also learned about additional business opportunities available by obtaining EDM equipment.
“After a short time, we repeated this process for the AG600L – linear motor driven wire EDM,” Savage continues. “Again, he heard first hand from another end-user about the ease of control, accuracies, and minimal re-cast layer – the microscopic fracturing that can occur during the wire machining process.” Savage notes that achieving minimal re-cast layers is extremely important for aerospace companies due to engine components moving at very high RPMs, and has always been a primary goal for all EDM builders.
Smooth Transition
From the time Donkersloot ordered the machines until they were installed, and AMT employees were fully trained, less than three weeks had passed. Speaking of the Sodick service support team, Donkersloot says, “They were very prompt and attentive to our urgent requirements and needs.”
About the training Sodick provides, Donkersloot adds, “The schools they offer have really helped my programmers and operators.”
“[AMT's] programmer was a novice to EDM, but after a short time he grasped the technology and ran with it,” Savage points out. After the programmer and main operator both had time on the machines, they attended a Sodick operator and programming class that brought everything together. Donkersloot recounts his programmer said the three-day class “was one of the best he has ever attended.”
Since installing the EDMs, Donkersloot reports the benefits the company has received are reduced costs, shorter lead times, and better quality.
The initial EDM purchases have continued to open up more opportunities, Savage says, thus the reason for his latest purchase, a Sodick AQ750LH (24" Z-axis) wire EDM. He notes this machine allows for very large workpieces for AMT’s current and future requirements.
With revenue of $2 million in the first quarter of 2013, the business is still growing. AMT is housed in a 26,000ft2 facilitythat is filling up rapidly.
According to Savage, Donkersloot realized the active aerospace sector, combined with his knowledge and enthusiasm, made the timing for AMT’s return to business excellent.
“His previous customers were eager to get him back as a vendor again,” Savage says.
Advanced Materials Technologies LLC
Phoenix, Ariz.
www.amt-america.com
Sodick Corp.
Schaumburg, Ill.
www.sodick.com
About the author: Eric Brothers, senior editor, can be reached at ebrothers@gie.net or 330.523.5341.
View now: Watch a Sinker EDM Demo: http://bit.ly/17TaoMh
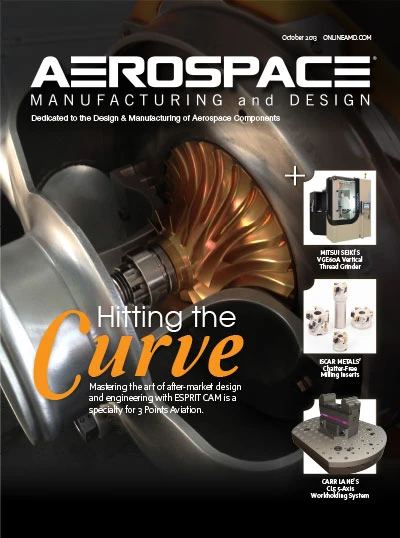
Explore the October 2013 Issue
Check out more from this issue and find your next story to read.
Latest from Aerospace Manufacturing and Design
- Revitalizing the Defense Maritime Industrial Base with Blue Forge Alliance
- Safran Defense & Space opens US defense HQ
- Two miniature absolute encoders join US Digital’s lineup
- Lockheed Martin completes Orion for Artemis II
- Cylinder CMMs for complex symmetrical workpieces
- University of Oklahoma research fuels UAS development
- Motorized vision measuring system
- Everyone's talking tariffs