When it comes to business at 3 Points Aviation, “One-of-a-Kind” is a phrase at the tip of the iceberg.
Subtract the fact that the company is nestled quietly in picturesque Charlottetown on Canada’s Prince Edward Island and even without the scenic locale, business behind shop doors is beyond the ordinary.
“There are really not a lot of companies out there that do what we do,” says Spencer Burns, lead programmer for 3 Points Aviation, which offers full engineering, manufacturing, and repair and overhaul services to the aerospace industry.
Even saving the day isn’t an uncommon item on the to-do list for the crew at 3 Points, where making repair parts for grounded aircraft – and making them in a hurry – is all in a day’s work.
In a nutshell, business at 3 Points Aviation is niche manufacturing layered in complexity.
Among the capabilities of the company are the reverse engineering, repair and overhaul, and manufacturing of components for the Dash-8 and other aircraft. The Dash-8 is a series of turboprop medium-range regional aircraft with twin engines. Although the aircraft and others like it remain in service, many of the original equipment manufacturers (OEM) have ceased making parts. With the feedback provided from in-house manufacturing, 3 Points Aviation’s engineers are able to make innovative design changes to OEM products that can reduce part price as well as improve quality and function.
And even if OEMs continue to supply parts, it often takes as many as 180 days for customers to receive them.
“We can handle those situations where there is an aircraft on the ground waiting for a component,” Burns says. “We’ve become very fast at processing parts. We can receive an AOG (Aircraft on Ground) manufacturing request from a customer, where a 20-plus-year-old drawing is usually provided, and have their one-off part to them in as little as one to two days.”
Machinery, Software Capabilities
Handling those curves requires machinery that can get the job done in a hurry, as well as computer-aided-manufacturing (CAM) software that can efficiently drive a wide range of machine tools.
ESPRIT CAM by DP Technology was chosen by 3 Points Aviation to program its seven CNC machine tools – including mills, lathes, mill-turns, and wire EDM machines. A 3-axis lathe, 4-axis wire EDM, B-axis mill-turn, 3- and 5-axis mills, and a 4ft x 8ft waterjet machine are among the extensive lineup. “The machines we have are capable of doing a broad range of machining,” says Burns, who adds that the company also builds its own fixtures and tooling.
While parts made at 3 Points Aviation vary in range from the simple to the complex, the average job lies somewhere in the range of medium complexity.
“Even if the parts are relatively simple in shape, the tolerances are tight,” Burns notes.
Unsurprisingly, the company manufactures parts primarily in aluminum and stainless steel, though it also specializes in cutting the more exotic materials, like Inconel.
Manufacturing Skill-Set
As a one-stop shop, the company manages design, programming, and production and, due to the unique nature of its skill-set, manufactures a great deal of prototype and one-off components. It’s also able to paint and coat the newly machined parts, as the facility is equipped with a painting booth and heat-treating area.
“It’s a very, very broad scope of daily activities,” Burns says. “It’s very challenging and also very gratifying. You have to almost be able to thrive on getting a curve ball here and there.”
At 3 Points Aviation, however, a facet of hitting that curveball out of the park is taking advantage of the timesaving features of ESPRIT. By identifying and setting standards for repeat parts, as well as standardizing manufacturing parameters for specific part families, each of its three programmers has access to the same timesaving information.
Software Advantage
Though the shop doesn’t do much repetitive work, 3 Points uses the ESPRIT KnowlegdeBase to free programmers from its small share of repetitive programming tasks, as well as to document vital data. Revision control is critical, and being able to quickly swap tools, speeds, feeds, and processes from the KnowledgeBase drastically reduces the time and error that goes into controlling multiple part revisions through the manufacturing chain.
“I’ve standardized a lot of the programming and done my best to capture the best practices and programming data,” Burns says. “With the KnowledgeBase, the knowledge doesn’t remain inside my head, and I’m able to capture and preserve what works best for us. I don’t even have to think of speeds and feeds. I just tell it if I’m roughing or finishing and I’m set.
“Also, with the intelligence of the default technology and process technology, I can teach ESPRIT to program features how I want them programmed. These tools within the KnowledgeBase allow the user to forget about the mundane tasks when programming and gives him or her the time needed to focus on the intricacies of the part.”
3 Points Aviation also takes advantage of ESPRIT’s report generator feature, which is an effective way to increase efficiency and reduce errors on the shop floor with little cost. The ESPRIT Report Generator automatically generates reports that provide the machining details an operator needs to correctly set up a machine and perform the required machining operations.
The combined strength of saving best practices and generating reports that detail specific manufacturing data has been a significant time saver at 3 Points, which has to deal with copious amounts of regulatory paperwork as a byproduct of working within the aerospace industry. The paperwork alone, Burns says, can take twice as long as the job in question.
“Once you get that stuff going, your output becomes exponential,” Burns says of the ESPRIT Report Generator and KnowledgeBase. “Your errors are significantly reduced and the repeatability is there.”
DP Technology Corp.
Camarillo, Calif.
www.dptechnology.com
Elizabeth Engler Modic, managing editor, can be reached at emodic@gie.net or 330.523.5344.
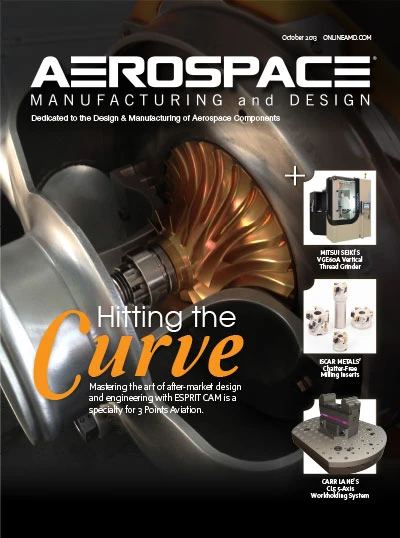
Explore the October 2013 Issue
Check out more from this issue and find your next story to read.
Latest from Aerospace Manufacturing and Design
- Cyient Group, Deutsche Aircraft finalize multi-year contract
- High surface quality at high speed
- #57 - Manufacturing Matters - Agile & Robust Supply Chain Management with Lisa Anderson
- Take control of your manufacturing business despite supply chain turmoil
- Strengthening the defense maritime industrial base for national security, economic resilience
- Register now to learn solutions for high-temperature aerospace machining challenges
- Expertise on machining, joining offered in April’s Manufacturing Lunch + Learn
- NASA offers free high school engineering program this summer