Precise machining of aircraft components is critical for both safety and long operating life. For example, landing gear strut tubes need to have an inside surface that is perfectly smooth. The smoothness is accomplished by passing a grinding wheel through the tube and grinding off any rough spots. Positioning the grinding wheel correctly so as to avoid excess wear on either the tube or the wheel has been challenging.
Traditionally, positioning of the grinding wheels in machining applications has been accomplished manually by watching and listening for the wheel to contact the part. In this application, however, it’s impossible to visually locate the wheel inside the tube. The machine operator must listen for sounds of contact between the grinding wheel and the workpiece in order to know when the two are in contact. To avoid the grinding of too much material off the inside diameter of the tube, the operator would need to detect the slightest sound of contact between the wheel and the tube. In the old days, this would require the machine guard to be left open, exposing the operator to potential flying material hazards in addition to the stress of a noisy work environment. Now, with safety regulations in force, machine guards must be closed, making it impossible to hear clearly when contact has been made (Photo 1). There’s another problem, too: If a human operator moves slowly in positioning the grinding wheel to avoid striking the workpiece too hard, then time can be wasted while the wheel is grinding air, reducing machine productivity.
Similar problem issues occur when the grinding wheel is being dressed. It’s important for the dressing operation not to grind too much material off the wheel, and it’s important with grinding quality in mind not to let the wheel deteriorate to the point where it’s not working correctly. If done manually, the dressing process can remove too much or too little material, and it can miss identifying emerging structural problems with the wheel.
Plant operators have looked for a better solution to these problems that doesn’t involve close human involvement. Clearly an automated system is indicated, but solutions that have worked in other industries, using a machine vision system, for example, won’t work in a dirty environment where the gap between the grinding wheel and the workpiece is obscured by cooling fluid. As an alternative, it’s possible to electronically monitor the load on the grinding wheel, but force sensors such as load cells are not extremely sensitive and may produce imprecise results, requiring that the grinding wheel move very slowly. Another alternative would be to monitor the power produced by the grinding motor as an indicator of when the wheel comes under load; however, the power increase happens relatively slowly with a lag time so it is difficult to identify a precise touch point.
For one manufacturer of landing gear components, the solution came through creative application of a sensing technology that was initially developed for dry grinding applications: acoustic emission (AE) sensing. AE sensing relies on the fact that when a grinding wheel touches a workpiece or a dressing wheel, even the slightest contact produces a sound that can be detected by sensitive instrumentation.
Traditionally, AE sensors have relied on vibration transmitted through the frame of the grinding machine, but it turns out that the coolant flow itself can be used to transmit the sound of the grinding wheel and workpiece coming together. This technique has been proven out in a grinding machine retrofit designed and installed by CNC North Inc. of Claremont, N.H., at the UTC Aerospace plant in Oakville, Ontario, Canada.
The CNC North solution uses acoustic emission sensors provided by Schmitt Industries’ (Portland, Ore.) SBS division. Sensors (Photo 2) are mounted on the coolant lines going to the grinder and the wheel dresser. In operation, acoustic signals coming from the workpiece travel up the coolant stream to the sensor module, which is otherwise isolated from its mounting attachment to the machine via rubber O rings that surround it. As long as the coolant stream is uninterrupted, the sensors can pick up even the slightest noise from contact with the grinding wheel. By incorporating AE sensors that are supported by automated controls, a CNC machine can automatically perform functions such as grind detection, crash protection, gap elimination, and dress control.
One of the benefits of the automated system is the ability for operators to precisely regulate the speed of the wheel positioning and grinding process and thereby optimize the productivity of the machine. The monitor screen that’s provided with the SBS system (shown at the top of the operator workstation in Photo 1) shows exactly when the grinding wheel comes into contact with the workpiece. When the sensor detects the initial contact with the part, software on the CNC machine is given a command to change the grinding wheel positioning from a rapid rate of motion to a slower rate for grinding.
“We program our gap positioning rate at four or five times faster than the grinding rate,” says Pat Harrington, president of CNC North. “This saves substantial cycle time from part to part – as much as 10% to 20% of the processing time.”
The SBS sensors are also used for wheel dress verification. Software developed by CNC North uses the AE sensor to monitor breakdown of the grinding wheel and instruct the CNC to repeat doing dress passes until the wheel is dressed correctly. Operator control software developed by CNC North provides a conversational interface that’s easy for operators to use by simply filling in the blanks (Photo 3).
Speed of response and sensitivity are the primary advantages of AE, which solves the problem of how to automate the grinding wheel positioning and dressing process. The creative new wrinkle is to rely on the machine’s coolant stream to carry the sound to the sensor. As a result of CNC North’s design using sensor technology from Schmitt Industries, UTC Aerospace saves time and cost. The speed of processing is increased, grinding wheel life is extended by not dressing off too much, and the quality of the end products is kept high.
Schmitt Industries Inc.
Portland, Ore.
www.schmitt-ind.com
CNC North Inc.
Claremont, N.H.
www.cncnorth.com
About the author: Mark Astor is applications engineer for Schmitt Industries Inc. and can be reached at mastor@schmitt-ind.com
Get curated news on YOUR industry.
Enter your email to receive our newsletters.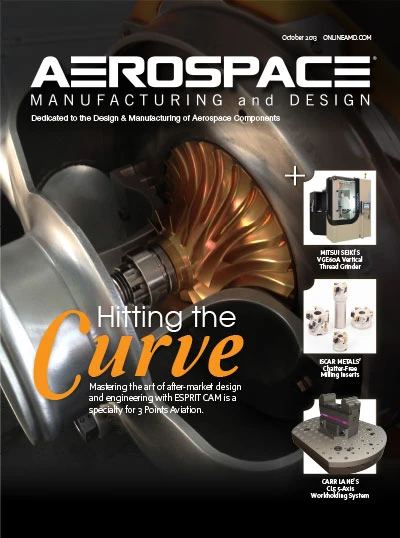
Explore the October 2013 Issue
Check out more from this issue and find your next story to read.
Latest from Aerospace Manufacturing and Design
- AIX showcases the future of air travel
- Sunnen Products' PGE-6000 gage
- #41 Lunch + Learn Podcast - SMW Autoblok
- Revolutionizing aircraft design without sacrificing sustainability
- GE Aerospace awarded subcontract for FLRAA next phase
- KYOCERA Precision Tools publishes 2025-2026 Indexable Cutting Tools Catalog
- BOC Aviation orders 120 Airbus, Boeing jetliners
- Mazak’s INTEGREX j-Series NEO