One could say that both the aerospace and medical industries pushed hardest for the development of in-process gaging on wire electrical discharge machines (EDMs). The reason is that shops within these industries operate under stringent process verification requirements, and in doing so, they must document their manufacturing/machining processes – wire EDMing included.
For medical shops, wire EDM allows them to accurately process workpieces that continue to shrink in size and involve geometries that are ever more intricate. Conversely, aerospace shops use wire EDM to cut large, heavy, highly-complex parts. However, having to remove either of these types of workpieces from machines to check and verify them significantly increases the risk of errors and adds to overall part cycle times.
With in-process gaging on their wire EDMs, shops can check and verify parts before and after the EDM process and without having to remove them from machines. Equally beneficial are recently developed wire-EDM in-process touch-probe gaging systems that allow the machines to read the probe data and understand logic statements. This means a machine can measure a table full of components after cutting and indicate which are within tolerance and can be removed. Alternatively, it can return to those needing re-cut and bring them into tolerance. In addition, with the future incorporation of pneumatic chucks to hold touch probes, the whole process could be performed without operator intervention.
It should be noted that wire EDMs have always been capable of in-process probing, per se, using the electrical pulse of their wire electrode material. However, when probing with a machine’s wire, shops are limited to running only a few measurement cycles such as center finds, edge finds, and corner finds. The process is unable to indicate wall straightness or gage other part contours.
Also with wire probing, there always has to be a gap between the probe (wire) and the workpiece for generating the electrical spark that indicates when contact has been made. The accuracy of this probing method is fairly good (within ±0.0001"), but there are variables that can skew the results. These variables include burrs on the parts, dirt, and other particles that might happen to fall between the wire and workpiece and generate false readings.
For precision industry work, shops require in-process wire-EDM gaging mainly to verify that parts were cut correctly and according to key part-shape reference points. Unfortunately, this level of probing/gaging was impossible using EDM wire as the probe – mainly because the wire can only measure the highest points of a part shape.
In addition, even if such advanced probing could be accomplished using the wire as a probe, doing so would be an unaccepted practice within both the aerospace and medical industries. A key reason is that when gaging critical parts, the electrical pulses/sparks from the EDM wire could actually create marks on components that could jeopardize their overall integrity.
Conventional probes, on the other hand, use round sapphire balls that provide very fine points of contact without damaging workpieces in any way. Additionally, the chances are very slim of touching exactly where there are debris or obstructions because of the tiny pinpointed area of contact.
Besides strong demand from the aerospace and medical industries, the natural limitations of probing with an EDM’s wire also drove many EDM builders, GF AgieCharmilles included, toward the incorporation of actual touch probes into the wire EDM process. Moreover, while in-process touch probing is nothing new with conventional machine tools or even sinker-type EDMs, the capability is new for wire EDMs. All the individual technological components necessary to accomplish the task were available, but years of R&D were required to figure out exactly how to integrate them into a wire EDM for effective in-process touch probing.
EDM OEMs had to overcome two main hurdles. On the mechanical side, the challenge was how to mount a chuck for holding the probe onto the head of the EDM, while on the control side, the probe function had to be integrated with the machine’s CNC.
Mechanical Challenges
Most EDM heads are not designed to support a lot of weight, and mounting an actual tool chuck onto one side of them would create an imbalance and affect the wire EDMing process. Fortunately, a few brands of wire EDMs, such as those from GF AgieCharmilles, feature heads that are robust and strong enough to handle the chucks without machine performance being compromised.
Another challenge on the mechanical side was the need for servo-driven Z-axis capability – one that is typically unnecessary for wire EDMing. In-process touch probing requires that machines have a servo-driven Z-axis so that probes can be moved down to workpieces, then up and out of the way when probing is finished. However, most importantly, the capability allows measurements to be taken and recorded at any number of points along the Z-axis, which is how wall straightness can be checked.
Most EDM OEMs, GF AgieCharmilles included, easily overcame the challenge of incorporating the necessary Z-axis capability. This is because many of them already had such existing servo-driven systems developed for use on their sinker-style EDMs and had an extensive understanding of these Z-axis systems as well as using a probe with them. Additionally, this existing knowledge helped with integrating conventional probing into the CNCs of wire EDMs.
Control Challenges
In-process touch probing requires that wire EDM CNCs have offsetting capabilities to compensate for the two different centerline locations of the touch probe and those of the machine’s head. Most machines in the industry have variables that allow them to accomplish such offsetting, so this wasn’t as significant a problem.
What GF AgieCharmilles developed to overcome this problem was an offset correction function. Basically, the machine’s control knows exactly the distance between the machine’s wire centerline and that of the probe in X- and Y-axis after calibration. The control then compensates for that distance when moving the probe into position for a measurement.
What proved to be a significant challenge on the control side for wire-EDM in-process probing was a lack of specific cycles needed for the machine to measure key points on a part’s shape.
For GF AgieCharmilles, the solution proved to be macro-B programming within the machine’s control. This type of programming commands the machine to move to desired positions and probe in the X-, Y-, and Z-axis, thus enabling key point measurements to be taken that were previously unrelated to the wire EDM process.
With data from probing, machines then generate reports that use mathematical equations to verify that parts were in fact positioned correctly in the machine prior to cutting. The reports also show that after cutting, the part is to size or within tolerance according to key points indicated for measurement.
Did you know? EDM can be used to machine conductive materials of any hardness to an accuracy of up to 0.001mm with no mechanical action. By virtue of these properties, EDM is one of the key technologies in mold and tool making. |
When macro-B programming incorporates the use of logic statements, wire EDM machine CNCs can read “if-then” program statements. For instance, if a particular workpiece geometry is not yet to specified size, the CNC commands the machine to return to that portion and re-cut it to the correct size.
This high level of logic within the system not only tells users that parts are to size and ready to be removed, but also allows the machine to perform self-corrections on parts based on probing data. This machine capability is probably the most significant accomplishment, and one that will have the most impact on lights-out production, as well as continue to drive the demand for in-process gaging on wire EDMs.
Automatic Touch Probing
Currently, mechanical chucks are manually loaded to hold probes for wire-EDM in-process gaging. But, with the incorporation of pneumatic chucks, robot tool changing can be used to automatically load and unload probes on wire EDMs.
Today, most shops have operators perform part verification. A machine operator will load the probe, measure the part, remove the probe, and push the start button to continue cutting. After cutting, the probe is reloaded, a macro-B program is run, and key points on the part are measured. The machine then indicates which parts are within specifications and those that need recutting.
As far as technology is concerned, all the required components exist for making complete lights-out wire-EDM operations that include automatic in-process probing routines a reality. However, at this time, few industries are requesting the capability be advanced to that level.
Optical: Another Approach
There are other methods used for in-process gaging besides touch probes. An example is optical systems that, instead of “touching” a part, record images of it for verification purposes. Such systems are especially beneficial for gaging those detailed parts found in precision manufacturing.
With GF AgieCharmilles’ optical system, manufacturing shops can quickly and easily gage those parts. Prior to optical systems, extremely intricate, complex, and involved fixturing was required to hold the piece for accurate gaging. Plus, the part location still had to be determined, and using the EDM’s wire for this would take more time than did the actual part cutting operation. To illustrate, cutting time might be 3 hours, but measuring took 10 hours. With the optical system, a split second image would indicate part orientation, center, and the start point for cutting.
Both optical and mechanical systems have their individual benefits. Optical systems can quickly measure (300 points within seconds) part shapes that were cut. Probes, on the other hand, would have to physically move to and touch each of those points. However, probes can measure top, middle, and bottoms of part cavities. Optical systems can record part shapes only as 2D images and would be unable to measure, for instance, an angled sidewall.
GF AgieCharmilles
Lincolnshire, Ill.
us.gfac.com/
About the author: Eric Ostini is a product manager at GF AgieCharmilles and can be reached at info@us.gfac.com.
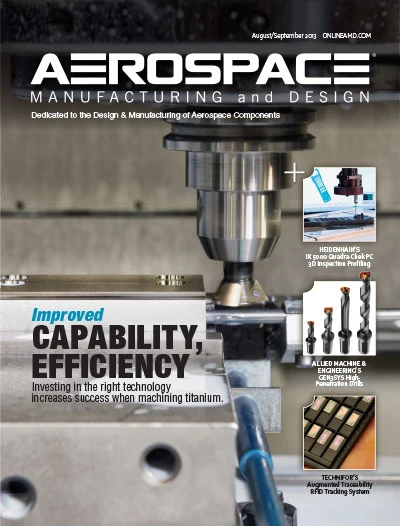
Explore the August September 2013 Issue
Check out more from this issue and find your next story to read.
Latest from Aerospace Manufacturing and Design
- Embraer tests wing for new technologies demonstrator
- Mitutoyo America’s SJ-220 portable surface roughness tester
- #55 - Manufacturing Matters - A Primer on Defense Contract Manufacturing
- Registration is open for April’s Manufacturing Lunch + Learn!
- Natilus begins search for new home to build world's most efficient commercial aircraft
- Aerospace Industry Outlook webinar is back by popular demand
- Automation Webinar with Visual Components
- PrecisionX Group expands manufacturing operations