Vapor degreasing has a long and storied past as the cleaning process of choice for providing parts free of contamination. Within the aerospace industry, it is a commonly used cleaning method because it is both simple and effective.
Vapor degreasing is both extremely effective and convenient for removing metalworking fluids, cutting oils, corrosion inhibitors, and waxes – soils that commonly remain after parts manufacturing at OEM and MRO (maintenance, repair, and overhaul) facilities. The vapor degreasing process requires minimal floor space because the cleaning and drying of parts can be done within the same cleaning chamber. Conversely, a typical aqueous immersion cleaning process, comprised of one or more heated “soap” washing stages followed by multiple heated rinsing and drying stages, could require three or more times the floor space. Another advantage of the vapor degreasing process is significantly lower energy costs compared to the aqueous cleaning process alternative.
For many years, the solvent of choice for vapor degreasing was 1,1,1-trichloroethane (TCA). However, the Montreal Protocol restricted the use of TCA as a vapor degreasing solvent because it was considered a major contributor to ozone depletion, along with many chlorofluorocarbons (CFCs). This protocol severely limited the number of viable vapor degreasing solvents available to process operators. Subsequently, the U.S. Environmental Protection Agency (EPA) launched the Significant New Alternatives Program (SNAP). One of the solvents approved as a viable alternative to CFCs for the vapor degreasing process under the SNAP program was trichloroethylene (TCE). Soon after the approval of TCE, many vapor-degreasing operators converted their solvent to TCE. Over the course of time, concerns associated with the use of TCE have arisen regarding its potential carcinogenicity and its classification as a hazardous air pollutant (HAP), so other alternatives have been sought. In 2007, one such alternative, n-propyl bromide (nPB), was also approved under the SNAP program. nPB offered similar cleaning performance as TCE, but it was given a non-regulated status because it was not classified as a HAP, nor was it considered potentially carcinogenic.
Recently, TCE has been deemed a human carcinogen by the EPA. In addition, the American Conference of Governmental Industrial Hygienists (ACGIH) has raised concerns over the potential health risks of exposure to nPB. The combination of the change in the classification of TCE and the concerns of ACGIH with respect to nPB have given many OEM and MRO facilities reason to strongly consider alternative vapor degreasing solvents to TCE and nPB.
All of these concerns have led to the following reasonable questions: “Why do companies continue to use the vapor degreasing processes?” and “Why do they view vapor degreasing as the preferred cleaning process?”
Patrick Oliver, sales manager with vapor degreasing equipment manufacturer Baron Blakeslee, offers his insight into this matter: “Our customers use vapor degreasing as the preferred cleaning process because it works better than any other cleaning method. Our company offers aqueous cleaning equipment too, so I do not want to denigrate that technology, as it does have its place. In my opinion, the only reasons to use an aqueous process are: if you are removing a soil that is only soluble in water; materials compatibility (although there are solvent formulations that offer a tremendously wide range of materials compatibility); or if you are performing some type of surface conversion process such as phosphating, etching, oxidizing, etc.”1
Case Study
The customer, a major U.S.-based commercial airline, employs a vapor degreasing process in a traditional open-top vapor degreaser to clean landing gear components from each aircraft during the FAA mandated “D Checks.” The customer had reached a decision to replace both TCE and nPB, the vapor degreasing solvents currently in use, due to environmental and employee exposure concerns. Numerous requirements for the alternative solvent were identified, including:
- Broad compatibility with metallic alloys
- Non-flammable classification
- Non-carcinogenic
- Not considered a HAP
- SNAP approval as a vapor degreasing solvent
- Reduced worker exposure concerns typically demonstrated by higher permissible exposure limits (PELs)
- Boeing BAC 5408 approval
- Equivalent or enhanced soil removal capabilities
Cleaning Product Evaluation
LENIUM FHD, a hydrofluorocarbon-based vapor-degreasing solvent designed to be used in open-top or vacuum-vapor degreasing systems, was introduced to the customer as a potential alternative to both TCE and nPB2. The customer was keenly interested in evaluating the cleaning effectiveness of LENIUM FHD based on the following features:
- Known compatibility with a wide range of metallic alloys
- Boeing BAC 5408 approved
- Is a blend of SNAP approved components that is non-flammable, non-carcinogenic, and it is not considered a HAP
- The recommended exposure limit of 200ppm for LENIUM FHD is considerably higher than both TCE and nPB
Test Protocol, Component Preparation
The large size of the components and sensitivity of the parts to be handled made it impractical to use them for the screening tests. Instead, a testing protocol was designed that made use of 1.5"-diameter 2024 aluminum alloy coupons as the metal substrate. The soils selected for the testing protocol were a number of commonly used aerospace oils. Each coupon was coated with an oil sample and allowed to air dry for a minimum of 24 hours at room temperature to “harden” the soil prior to cleaning.
The cleaning tests were performed in an open-top vapor degreaser using either nPB or LENIUM FHD as the solvent (Table 1). The soiled coupons were suspended in the solvent vapor blanket for 5 minutes, then removed. Since all of the aerospace oils selected for the tests were known to fluoresce under ultraviolet light, it would be possible to detect trace amounts of residual oil on the coupons after cleaning.
Results and Conclusion
The results of the cleaning tests comparing the effectiveness of LENIUM FHD to nPB can be found in Table 2. In all cases, equivalent cleanliness between LENIUM FHD and nPB was achieved. These results gave the customer confidence to install LENIUM FHD in its current vapor degreasing process (Tables 1 & 2 above). The LENIUM FHD process has exceeded the expectations of all stakeholders at the customer’s location, and the project has been viewed as a success.
Petroferm Inc.
Gurnee, Ill.
www.petroferm.com
About the author: Jeffrey J. Beard, sales manager North America, Petroferm Inc., Gurnee, Ill., has served the specialty chemical business for 24 years. During that time, he has worked extensively with aerospace, automotive, electronics, and medical customers worldwide to assist them in replacing hazardous chemicals used in their cleaning processes or to improve their existing vapor degreasing, aqueous, or solvent cleaning processes. Beard can be reached at 800.432.7187, 847.249.6366, or jbeard@petroferm.com
1Patrick Oliver, Baron Blakeslee, http://www.baronblakeslee.net/
2LENIUM FHD is a drop-in replacement for TCE and nPB as well as HCFC-141b, HCFC-225 and perchloroethylene (Perc).
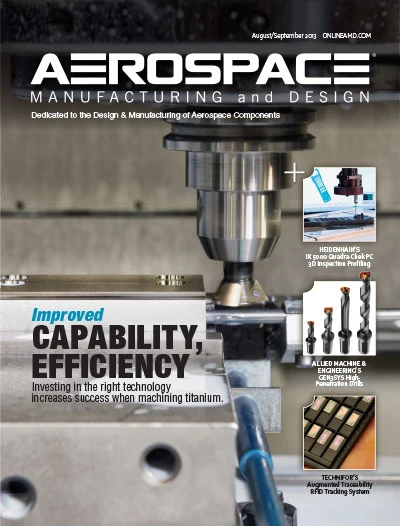
Explore the August September 2013 Issue
Check out more from this issue and find your next story to read.
Latest from Aerospace Manufacturing and Design
- Taiwan’s China Airlines orders Boeing 777X passenger, freighter jets
- Reamer re-tipping extends life of legacy tooling
- Revitalizing the Defense Maritime Industrial Base with Blue Forge Alliance
- Safran Defense & Space opens US defense HQ
- Two miniature absolute encoders join US Digital’s lineup
- Lockheed Martin completes Orion for Artemis II
- Cylinder CMMs for complex symmetrical workpieces
- University of Oklahoma research fuels UAS development