![]() |
Five machining centers occupied a portion of N.M. Hansen’s facility in Toledo, Ohio, in 2011: Two old ones could not hold tolerances less than 0.005". Another had a small working envelop and an ill-integrated control. None of them could machine the company’s small lot orders efficiently.
Roger Burditt, president and CEO of N.M. Hansen, had a choice to make. His company could either machine the small-quantity parts using a bed mill, or it could stop producing the parts altogether. Neither choice was optimal, but Burditt decided on using a TRAK DPM CNC bed mill.
N.M. Hansen’s small-lot production consists of parts that require significant tool changes. However, the bed mill features a manual tool changer, which forced N.M. Hansen’s operators to waste excessive amounts of time changing tools.
“It did its job, but we had to have a lot more operator input,” Burditt says. “It didn’t have an automatic tool changer, so the guy had to physically change all the tools all the time. I’d say we probably wasted an hour a day tool changing.”
N.M. Hansen manufactures precision-machined parts for the aerospace sector. The company operates out of a small, 36,000ft2 facility, but has worked with big players in the industry: GE Unison, Champion Aerospace, Williams Int’l. Filling timely orders for these companies was almost impossible with the bed mill, Burditt says. “We wanted to get into the newer generation of machining centers with tool changers.”
In 2011, Burditt and N.M. Hansen’s shop supervisor, Jesse Linenkugel, shopped for a replacement machine. The requirements: an automatic tool changer to terminate the oscillation ritual operators practiced with the bed mill, and a CNC system that would reduce changeover and programming times enough to make small-lot processing economically worthwhile.
N.M. Hansen owned five other machines from Rancho Dominguez, Calif.-based Southwestern Industries at that time, Burditt says. During the decade the two companies worked together, Burditt says Southwestern provided reliable products and services. If a machine shut down, a representative responded quickly, he explains. It made sense to him to see Southwestern’s selection, and the California company’s TRAK LPM fit his and Linenkugel’s qualifications.
The small-lot quantity production, 3-axis LPM adds considerable advantages to N.M. Hansen’s machine arsenal. In addition to its 16-position, automatic tool changer, the machine features an easy-to-learn and easy-to-use programming language, and its Ball-Lock and Tool-Setting systems reduce changeover times.
Conversational Coding
The LPM uses simple, ProtoTRAK conversational programming language, which reduces a company’s reliance on CAD/CAM and G-code specialists.
![]() |
“This means that, although the machine is G-code and CAM-file compatible, you don’t need to know G-code or CAM to program it,” says Bruce Meredith, marketing manager for Southwestern. “This is important for shops that run high-mix, low-volume jobs where highly specialized CAM programmers can become a bottleneck.”
The ability to switch between G-code and simpler language makes N.M. Hansen more versatile, Meredith explains.
“They program their simple jobs at the LPM,” he says. “If they have a more complex job, they generate a CAM program and send it over their network to the LPM, where it can be opened as either a .CAM or .GCD file. If opened as a .CAM file, the program will be automatically converted into a ProtoTRAK conversational language program that can then be edited and/or run as desired.”
However, Burditt says N.M. Hansen prefers to open the program as a .GCD file. He says the company’s operators then use the LPM’s G-code editor, if necessary, and run the program directly as a G-code file.
Linenkugel adds that the conversational programming feature has provided some of the biggest benefits for operators.
“The CNC is one of the easiest CNCs out there to operate… [the operators] like the simplicity of the programming,” he says. “You can take anybody that has hardly any experience, and they can be producing parts within a relatively short amount of time.”
Fast Changeovers
The LPM’s workholding system, combined with the automatic tool changer, has slashed N.M. Hansen’s processing time from nearly an hour down to 10 to 15 minutes. Much of the decrease is due to the Jergens Ball Lock workholding system, which eliminates the need to find part zeros whenever a part is loaded into the machine.
LPM Features
ProtoTRAK Specifications
|
The LPM features preprogrammed Jergens Ball Lock receivers built into its worktable. “When a job is run, the operator clamps down a fixture plate with vise, fence, and stop into the ball locks, loads a part into the vise, and establishes part zero,” Meredith explains. “Once part zero is set, the LPM memorizes it so that it doesn’t have to be re-established for the remaining parts in the lot. In addition, part zero does not have to be re-established if the job is run again at some time in the future (using the same fixture plates with standard vise, fence, and stop or equivalent fixturing) because the LPM already knows where part zero is.”
The LPM also offers the option to generate a program for a future job, while the machine performs a different job. Operators can measure and enter tool offsets during “stage mode” while the LPM simultaneously machines a part on the table.
Time and Money
Ron Clark, chairman for N.M. Hansen, succinctly summarizes his production philosophy: “Time is money.”
N.M. Hansen’s aerospace customers would probably agree with him. When a company like GE Unison orders a product, it expects it “right now. Yesterday,” Clark says. “They want their product ASAP.”
The TRAK LPM provides the flexibility and capability for N.M. Hansen to deliver its orders quickly – if not yesterday.
“It’s a lot faster and easier to set up,” Linenkugel says. “It definitely reduces our time.”
Clark agrees, adding that the company used to quote four weeks for a delivery. That quoted time has been cut nearly in half since the LPM’s installation.
In late 2012, a technician for Southwestern added a fourth axis to N.M. Hansen’s machine. The extra axis initially acted as an indexer. However, Burditt says the company has begun using it as a true fourth axis. Most of N.M. Hansen’s jobs do not require the additional axis, but he says more opportunities are available with it, and he can now bid on jobs that need the fourth axis – something he couldn’t have done two years ago.
N.M. Hansen Machine & Tool Co.
Toledo, Ohio
www.rogarinternational.com
Southwestern Industries Inc.
Rancho Dominguez, Calif.
www.southwesternindustries.com
About the author: Danny English is an associate editor for AMD and can be reached at denglish@gie.net.
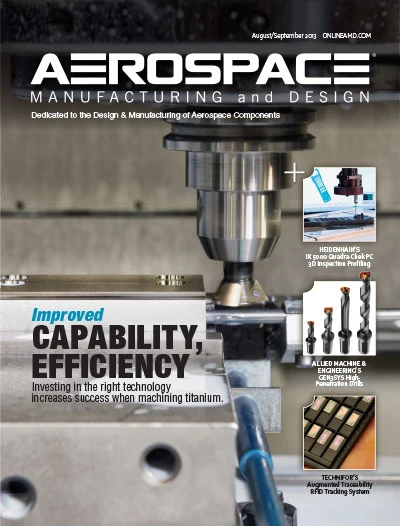
Explore the August September 2013 Issue
Check out more from this issue and find your next story to read.
Latest from Aerospace Manufacturing and Design
- The Partner Companies acquires Precision Eforming
- Hall Effect angle sensors
- July is for learning – so drop in for this month’s second Manufacturing Lunch + Learn
- Essential strategies to protect your data
- NASA selects instruments for Artemis lunar terrain vehicle
- Twin-cutter boring head
- Bell awarded funding for X-plane build phase of SPRINT program
- Shaft coupling clamps