Imagine developing a new aircraft component that is significantly lighter, is simpler to install, and provides excellent mechanical properties to meet rigorous qualification requirements. Aerospace engineers no longer have to dream about such benefits. Metal replacement has become an imperative as engineers search for any possible ways to take weight out with high-strength polymers such as PEEK. This thermoplastic polymer has been specified on commercial and military aircraft platforms for more than 25 years, giving it the proven track record engineers need when making critical material selections. Not only is PEEK a lightweight solution, it also provides the opportunity to consolidate and simplify part designs through the injection molding process. The replacement of heavy metals aboard an aircraft can ultimately lead to greater fuel efficiency as well as improved assembly and manufacturing speeds for modern and next-generation platforms.
According to industry averages and studies, removing as little as 100 lb (45kg) of weight from one airplane can result in up to $10,000 in fuel savings1 and 34 tons of CO2 emission reductions2 per year. With fleets typically employing several hundred aircraft, these figures can add up to millions of dollars saved and a significantly smaller carbon footprint. A major benefit of making the switch from metal to PEEK is the substantial weight savings that are possible. When reinforced with glass or carbon fibers, PEEK polymers can offer up to 70% weight savings compared to stainless steel, up to 55% weight savings compared to titanium, and up to 40% weight savings compared to aluminum while maintaining equivalent stiffness to the metals they are replacing (Figure 1).
Designing with thermoplastics like PEEK allows engineers to take a current metal component, re-visit the design, and simplify it. This makes it easier to install – an improvement for both the installation and manufacturing teams at the tier and OEM level. The injection molding process lets designers get creative, with the goal being to generate one highly functional component. The beauty of the injection molding process is that it can be optimized for faster processing cycles and easy part-to-part repeatability, which means lower overall costs compared to metals. Even thermoplastic PEEK composites take advantage of processing times measured in minutes whereas traditional thermosets can take hours – not to mention they are not recyclable like PEEK. These benefits have led to qualifications from industry-leading aerospace companies, government agencies, and military organizations.
PEEK exhibits an unparalleled combination of performance characteristics that other polymers and metals do not. For instance, PEEK offers excellent resistance to standard aerospace chemicals such as jet fuel, hydraulic fluid, insecticides, de-icing solutions, cleaning agents, and fire extinguishing compounds. PEEK components also do not require anti-corrosion treatments, which can add to metal part manufacturing costs. The polymer also provides strength across a broad temperature spectrum. In fact, PEEK shows no performance loss after heat aging at 260°C (500°F) for more than 5,000 hours. PEEK also has a very low fire, smoke, and toxicity (FST) rating making it a reliable material to use on the interior of the aircraft (Figure 2). These attributes, among many others, are the reason behind PEEK being labeled a viable metal replacement solution.
Over the past three decades, the use of PEEK has expanded beyond molding to semi-finished products such as extruded film and pipe. This versatile thermoplastic polymer has even found its way into composite forms including woven fabric and unidirectional tape. The ability to make thinner and lighter parts, with increased part service life and reduced assembly times, has played an important role in PEEK being specified as a proven solution for the following metal replacement applications.
As airplanes become even more complex, securing the wiring and hydraulic tubing that control the aircraft’s systems can require thousands upon thousands of system attachments including clamps and connectors. One of the world’s leading suppliers of interconnect products has worked to replace aluminum and stainless steel in these applications in order to offer a differentiated product that improves performance and fuel efficiency. One electrical wire bundle clamp made out of PEEK is 20% lighter than the aluminum clamp it replaced. There are approximately 15,000 clamps used to secure the wiring and cables on a given plane, which results in substantial weight savings. This translates into $23,000 per year in fuel savings as well as a CO2 emission reduction of 80 tons for each plane using this technology.
Not only can this application help save airlines money and reduce air travel’s effect on the environment, but the clamps are much easier to install. The switch from metal to plastic allowed for a re-design that led to the integration of a new locking hinge that helped reduce installation times by 30%. This feature of the clamp provides manufacturers with the opportunity to install the clamps with one hand leaving the other free for other tasks. This simplification was made possible through a sleek design and the ability of PEEK to be injection molded.
The same parts supplier has also developed a PEEK electrical connector used on various aircraft platforms. Stainless steel was the material up for replacement in this application, which helped in the realization of a 9% weight reduction. With hundreds of these connectors employed on each plane, the fuel and CO2 emission savings potential is again a significant benefit for making the switch from metal to plastic. The weight savings are actually achieved through the consolidation of several stainless steel parts into a one-piece PEEK component, which, in turn, also makes installation easier.
Recently, PEEK tubing was qualified as an alternative to metal in the cargo drainage system on a next-generation aircraft. The PEEK drainage system offers a 33% weight reduction compared to the incumbent metal. While the length of tubing used remains undisclosed, estimates have shown that replacing 100m of metal piping with PEEK can save up to $3,300 in annual fuel costs and 12 tons of CO2 emissions per plane. PEEK pipe is highly workable, as one company has developed the ability to bend, form, and flare the tubing to fit within the plane’s structure. The lightweight nature of the PEEK thermoplastic makes it much easier to install than heavier metal systems, which can help speed up the manufacturing process up considerably.
Thermoplastic composites with a PEEK matrix continue to become more popular when the highest strength and stiffness at lighter weights is needed, or when thermoset cycle times slow down the rest of the supply chain. A long-time molder for the aerospace industry has invested in composite manufacturing equipment to begin producing thermoplastic composite structural brackets. Typically, PEEK composites can deliver up to 70% weight reductions compared to traditional metals but with vastly higher mechanical properties. For example, a PEEK composite can provide up to five times higher specific strength with four times higher fatigue strength and specific stiffness when compared to aluminum. This strength-to-weight ratio is unmatched by metals.
As the industry continues to seek out all avenues to improve fuel efficiency, PEEK will continue to provide solutions to some of the toughest metal replacement challenges as it has for the past three decades. From injection-molded components and thin films to durable tubing and high strength composites, PEEK is a major contributor to help aerospace engineers reduce aircraft weight, assemble them faster, and improve the service life of their valuable vehicles.
Victrex Polymer Solutions
W. Conshohocken, Pa.
www.victrex.com
About the author: Richard Leibfried, technical sales and marketing manager with Victrex Polymer Solutions, can be reached at rleibfried@victrex.com.
1“An Airbus goes on a diet,” December 2012,
“Fuel Smart Celebrates its 5th Anniversary,” 2010,
2“Carbon Independent Aviation Sources,” August 2007,
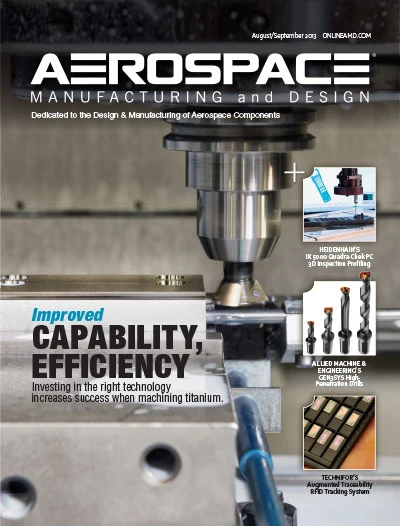
Explore the August September 2013 Issue
Check out more from this issue and find your next story to read.
Latest from Aerospace Manufacturing and Design
- NASA selects instruments for Artemis lunar terrain vehicle
- Twin-cutter boring head
- Bell awarded funding for X-plane build phase of SPRINT program
- Shaft coupling clamps
- #46 Lunch + Learn Podcast with SMW Autoblok
- Gleason Corp. acquires the Intra Group of Companies
- Thread milling cutter reduces cutting pressure, vibration
- Malaysia Aviation Group orders 20 more Airbus A330neo widebodies