Three Flute End Mills
A new series of high-performance 3-flute end mills for difficult materials and challenging applications are now available. With a corner radius, the Series 33 end mills are designed for aggressive ramping, pocketing, and slotting of materials such as stainless steel, titanium, and Inconel. The open structure at the axial end accommodates material flow and load reduction during machining operations involving aerospace structure components.
The tool series is available exclusively with an abrasive-resistant coating for wear resistance, avoiding built-up edge.
- Stepped Core Design: Optimal chip control and rigidity
- Unique Variable Geometry: Offers chatter and vibration suppression
- Symmetrical End Gashing: Better balance, high level of strength and ramping capabilities
SGS Tool Co.
Munroe Falls, Ohio
www.sgstool.com
Speed, Efficiency, Automation
Mastercam X7 Mill software offers expanded machining flexibility and an increased emphasis on speed and automation. The new simulator, probing, and tool manager combine with dozens of additional new enhancements in a package intended to improve shop floor productivity.
Highlights
Simulator – The backplot and verify utilities that you use to check all your Mastercam tool motion have been combined to offer a more efficient workflow, better analysis tools, and more comprehensive toolpath support. You still access Backplot and Verify from buttons at the top of the Operations Manager, but these utilities now display their results in a separate window. This allows you to keep making adjustments to your toolpaths even as your tool motion display continues.
Probing – Renishaw’s Productivity+ is used for in-process gaging via a measuring probe on a machine tool to determine fixture offsets, orientation, and critical dimensions. Probing eliminates the need for tool presetters, expensive fixtures, and manual settings with dial indicators. It allows for machine offsets to be automatically adjusted during machining.
Tool Manager – This application has been designed as a flexible and efficient way to manage tools and tool-holding components and to create tool assemblies that can be used in Mastercam.
Additional Tools:
- Dynamic and OptiRough toolpaths with more efficient tool motion
- Multi-threading support extended to most 2D high speed toolpaths
- Oscillate motion for Curve and Swarf 5-axis toolpaths
- 3D HST Hybrid toolpath improvements
CNC Software Inc. (Mastercam)
Tolland, Conn.
www.mastercammill.com
Upgraded Parts Washer
The model RW6072 industrial parts washer has been enhanced with upgrades to improve washing efficiency. It features a 20hp pump – a curve reservoir-mounted vertical centrifugal pump – giving approximately 200gpm pump capacity at approximately 65psi. Its pump has no bearings, seals, or gaskets to replace. The rotating workbasket measures 60" diameter and has a work clearing height of 72". Weight load capacity is approximately 2,500 lb. The table being mounted in off-center cabinet position provides loading access to the basket, which is rotated by a 1/2hp rotary basket gear-motor that is sprocket and chain driven.
This unit is equipped with an industrial, natural gas burner with electronic ignition, electronic flame sensor, fresh air blower motor, and adjustable air intake. It heats wash water between 160°F to 180°F and also features dual belt-type oil skimmers.
The cabinet is constructed out of 7-gage steel, structurally reinforced steel with rod, and a carrier bearing hinge system for the door.
Viking Blast & Wash Systems
Rose Hill, Kan.
www.vikingcorporation.com
Automatic Magazine Bar Feeders
Alpha 552 is designed for fixed headstock turning machines with diameters from 0.20" to 1.85" (5mm to 47mm) and up to maximum 2.047" (52mm) diameter with bar preparation. The bar feeder uses hydrodynamic or hydrostatic oil guiding technology to safely support bar stock and reduce vibration transference. Exclusive Quick-Change round guiding elements and pusher enable partial changeovers in less than 3 minutes and complete changeovers in less than 8 minutes.
Other Standard Features:
- High-capacity self-contained magazine tray
- Easily accessible and simple centralized bar selection adjustment
- Two-position hydrostatic outboard stabilizer with quick-change bushing system
- Automatic torque and speed adjustment
- An 18.5” Z-axis retraction system
LNS America
Cincinnati, Ohio
www.lns-america.com
Press Brake Control Upgrade
The productivity advantages of touchscreen control and bend simulation software are available to customers with popular vintage model press brakes. The control and advanced software, which enable 3D rotational viewing of part shape and gage fingers, can be retrofitted to the company’s Autoform, Formaster, Formaster II, CB, CBII, and AutoShape press brakes. The control aids operators with automatic bend simulations, graphic displays of parts before and after the bend, part orientation, setup notes, and a tool library. It can access jobs from its high-capacity internal flash drive, USB, or Ethernet. New part programs are easily created on the control or by using the optional offline Bend Simulation software.
User-friendly controls reduce programming and setup time through fast data entry via the touchscreen interface with large target buttons. Job setup pages display tool names and locations, segment lengths, and operator notes to further reduce setup time and ensure important instructions are displayed each time a job is recalled. After selecting the bend sequence and tools from the graphical tool library, part programs are created with one touch. Automatic Gage Allowance calculation reduces trial and error at the machine.
Cincinnati Inc.
Cincinnati, Ohio
www.e-ci.com
5-Axis Waterjet System
The EDGE X-5 5-axis waterjet system cuts complex taper-free and 3D parts from virtually any material. Featuring Permalign EDGE technology, the X-5 is capable of cutting chamfers, weld bevels, and sophisticated 3D parts such as impeller blades. It also features an industrial PC controller designed specifically for 5-axis waterjet cutting. The AquaVision Di Controller’s open architecture design gives operators the freedom to fine-tune programs from any CAD/CAM/nesting software, utilizing standard G&M code. The system's Intelligent Work Envelope automatically adjusts, depending on the angle of the cut, to protect the operator, material, and system components.
The unit’s solid design separates the motion system from the catcher tank, eliminating vibration and ensuring maximum part quality. It is ball-screw driven for optimal precision and features direct-couple AC brushless digital servo motors and single or double carriages. Critical bearing components are protected by heavy, metal covers with brush seals and positive air pressure.
Options
- Sizes from 5ft × 5ft (1,525mm × 1,525mm) to 24ft ×13ft (7,515mm × 3,365mm).
- Pumps from 30hp-200hp (22kW-149kW), 60,000psi-90,000psi (4,100 bar-6,200 bar); hydraulic intensifier and direct drive pumps are available.
Jet Edge Inc.
St. Michael, Minn.
www.jetedge.com
Compact, Self-Contained Grips
Split insert tensile grips for high-volume production testing of shoulder-end or button-head machined specimens are a preferred solution for testing high-strength materials that may damage or excessively wear traditional grip arrangements, and these grips promote effective testing on a variety of metals and alloys.
The grips conform to ASTM E8, A370, A48, and GOST 1497 (type III specimen), while also improving the operator’s ability to meet alignment standards ASTM E1012 and Nadcap AC7101. The automatic positioning of the inserts ensures uniform specimen support and loading for standard specimens.
Designed as a compact, self-contained assembly, the split insert tensile grips: eliminate risk of specimen ejection at failure, reduce loose parts to ensure operator safety when inserting and removing specimens, minimize the test area required for installation, and maximize the grip separation for testing with an extensometer.
Instron
Norwood, Mass.
www.instrom.com
Rigid, Stable Heavy-Duty CNC
The LV1100RM high production vertical CNC turning center features a rigid and stable platform for heavy-duty cutting, and a single piece and a square type column that offers robust stability. Its vertical configuration offers superior chip flow and is ideal for in-line production applications with automation.
A traveling column maintains accuracy when turning larger workpieces. Each axis is directly connected to a reliable digital servo motor to provide high rigidity and minimal thermal distortion. All axes are driven by large diameter, high-precision double-nut ball screws. The double pretension design provides accurate positioning and repeatability with virtually no thermal growth. All ball screws are connected directly to the servo drive motors without gears or belts, eliminating backlash.
A large, 12-station BMT turret is standard, and is driven by a high-torque servo motor with a 0.4 second indexing time in either direction. Machining capabilities have been increased with the addition of a straight milling head, which can remove material from the side of the workpiece, and angular milling head, which can perform ID operations.
It also features the latest generation Fanuc i CNC control. Networking capabilities allow programs to be loaded directly to the shop floor from the CAM workstation.
Bed & Column
- Maximum swing: 1,355mm
- Maximum cutting diameter: 1,160mm
- X-axis travel: 620mm
- Z-axis travel: 1,000mm
- X-axis rapid travel: 24m/min.
- Z-axis rapid travel: 24m/min.
Hyundai WIA Machine Corp.
Carlstadt, N.J.
www.hyundai-wiamachine.com
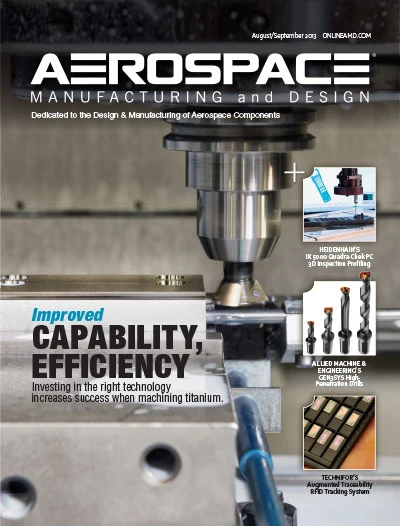
Explore the August September 2013 Issue
Check out more from this issue and find your next story to read.
Latest from Aerospace Manufacturing and Design
- Embraer tests wing for new technologies demonstrator
- Mitutoyo America’s SJ-220 portable surface roughness tester
- #55 - Manufacturing Matters - A Primer on Defense Contract Manufacturing
- Registration is open for April’s Manufacturing Lunch + Learn!
- Natilus begins search for new home to build world's most efficient commercial aircraft
- Aerospace Industry Outlook webinar is back by popular demand
- Automation Webinar with Visual Components
- PrecisionX Group expands manufacturing operations