Cleaning is usually the first task in maintenance, repair, and overhaul (MRO) processes – and it’s mostly very expensive. Industry offers a variety of cleaning procedures to achieve the required cleanliness for the subsequent work, focusing on speed, efficiency, safety at work, and concern for the environment. Another goal is to permit cleaning without the need to dismantle. Reliable removal of impurities is necessary to facilitate the real work of repair, maintenance, refurbishment, or inspection of plant, machinery, assemblies, and components. Cleaning thus has a decisive impact on quality and costs in MRO processes – and just how cleaning achieves cost-effectiveness and eco-efficiency depends on using the appropriate technology.
Renewable Resources
Manual cleaning is part of the daily routine in virtually every maintenance shop or department, using cleaning agents that meet the demands for safety at work and environmental protection, in addition to the required quality of cleaning, user-friendliness, and efficiency. Innovative cleaning agents are now available, with constituents based on renewable resources, having the potential to replace VOC-based and/or irritant solvents such as petroleum. Depending on their composition, these cleaning agents can even deal with heavy contamination such as rubber marks, bitumen and wax residues, grease, oil carbon deposits, rust, cracking, and adhesive residue.
Scoured Clean
Spray-jet procedures such as waterjets, shot blasting with solid media or steam, dry-ice blasting, and laser beaming provide efficient, cost-effective, and rapid cleaning processes for maintenance tasks. Mobile cleaning units are available for these processes, as well as fixed cleaning systems.
A new steam-blasting procedure bases its cleaning effect on the combination of saturated steam and a high-speed air-stream. Steam is generated by heating water as it flows through, so that there is always a constant amount of steam for cleaning, with consistent properties. The steam throughput rate, and its temperature and fluid content, are determined by the items to be cleaned and the impurities to be cleaned away. The system can reliably remove even heavy contaminants such as dried oil without using chemical cleaning agents.
Dry-ice jet cleaning is being used for more and more maintenance tasks. This is due partly to the technical advantages of the process; and also to its low environmental impact. The odorless, colorless, non-flammable, and non-toxic CO2 for the jet-spray process is produced and prepared as a byproduct of chemical and industrial processes. Its cleaning power comes from a combination of thermal, mechanical, and sublimation effects. Among other applications, this dry process is used for cleaning spray injectors and molds, in the food and aerospace industries, and for removing paint and coatings. Dry ice is a non-conductor, so it can also be used to clean live plant and equipment.
Laser beams are used to vaporize away layers of grime using focused light. Their applications are in such areas as removal of organic and inorganic coatings, and cleaning functional surfaces in preparation for subsequent processing.
Water or Solvent
In so-called wet chemical cleaning, the process operates under semi-automatic or full automatic control, in single or multi-chamber plants. The cleaning effect is mainly determined by the solvent properties of the cleaning agent used. Popular current choices include both aqueous cleaners, available in alkaline, neutral, and acid forms, and solvents – the solvents being broadly sub-divided into non-halogenated hydrocarbons (HCs), modified alcohols, and chlorinated hydrocarbons (CHCs). The cleaning effect of the medium is also aided by a variety of powerful physical processes, including spray-jet and ultrasonic cleaning.
Spray-cleaning is used for such applications as maintenance of automobile and machine drive components, gearboxes, casting and blanking tools, claddings and housings, and fixed assemblies. Using a spray arrangement tailored to the component geometry, together with high spray pressure and volume, enables rapid and reliable removal of adhesive contaminants such as oil, grease, and dust. In the new Puls-Clean process, a pulsed jet is created and “shot” at the surface to be cleaned. This results in greater effectiveness and also reduces water consumption by up to 20%.
parts2clean International Trade Fair for Industrial Parts and Surface Cleaning What procedures will reduce the cost and downtime of servicing and maintenance for machines and plant? Which cleaning agents are suited to what tasks? How can maintenance-related cleaning be optimized in terms of economy, the environment, and safety at work? Get the answers to these and many other questions connected with cleaning components and surfaces at parts2clean, Oct. 22 - 24, 2013 at the exhibition center in Stuttgart, Germany. With its comprehensive coverage, parts2clean provides complete details on various systems, process technologies, cleaning agents, alternative cleaning technologies, workpiece holders and part cleaning baskets, media treatment and disposal, cleanliness control, corrosion prevention, protection, and packaging. The three-day parts2clean technical forum, with simultaneous German-English/English-German translation of lectures, offers additional knowledge about cleaning. www.parts2clean.com |
With ultrasonic cleaning, whole items of equipment and complete assemblies such as motors, drives, and molds can mostly be cleaned without dismantling the components. This type of cleaning process is also effective in achieving the required cleanliness for workpieces with inaccessible cavities, such as blind holes, knurls, crannies, and undercuts. The cleaning effect of ultrasonics is based on cavitation: An ultrasonic generator generates electrical signals at a specified frequency, and these are transmitted as sound waves into a fluid bath by an ultrasonic oscillator. The high intensity of the sound pressure produces an interaction of positive and negative pressures. In the negative pressure phase, microscopic cavities are formed, and these bubbles implode during the subsequent positive pressure phase, creating shock waves with high energy density. This creates micro-streaming in the fluid, and the particles and films of contaminant are effectively blasted off and washed away. The ultrasonic frequency has a significant effect on the degree of cleaning. In general, the lower the frequency, the larger the cavitation bubbles and the greater the energy released from them.
Good Access
In wet-chemical cleaning, it’s not just the cleaning agent and the process technology that influences the results – the cleaning container also has a marked effect on duration, quality, and costs. For rapid and reliable removal of contaminants, good access to the parts in the container is essential – only then will the cleaning agent be able to get to all parts of the workpiece equally, so that the washing mechanism can be fully effective in flushing away contaminant films and particles. Consistent use of round-wire containers makes this possible; cleaning containers of this material are significantly less liable to drip than closed or perforated-plate containers, resulting in much lower scattering of the contaminants and the cleaning agent. Where assemblies are stripped down before cleaning, the maintenance process can be optimized by using cleaning baskets. These cleaning and transport containers are designed to accept all the individual components of an assembly, allowing the various parts of the dismantled product to be kept together as they pass through the maintenance process. This eliminates the time and cost wasted in collecting the parts together again, and avoids mixing up individual components.
About the author: Doris Schulz is a technical writer in Korntal, Germany, and can be reached at doris.schulz@pressetextschulz.de.
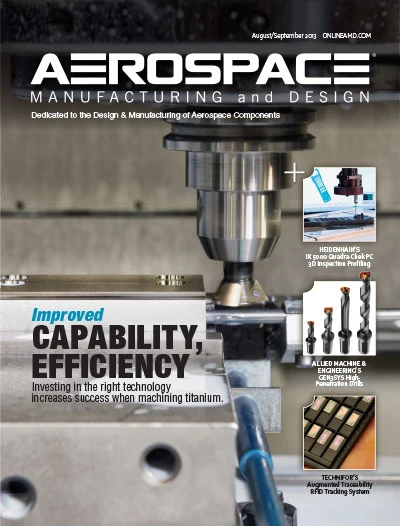
Explore the August September 2013 Issue
Check out more from this issue and find your next story to read.
Latest from Aerospace Manufacturing and Design
- Taiwan’s China Airlines orders Boeing 777X passenger, freighter jets
- Reamer re-tipping extends life of legacy tooling
- Revitalizing the Defense Maritime Industrial Base with Blue Forge Alliance
- Safran Defense & Space opens US defense HQ
- Two miniature absolute encoders join US Digital’s lineup
- Lockheed Martin completes Orion for Artemis II
- Cylinder CMMs for complex symmetrical workpieces
- University of Oklahoma research fuels UAS development