In the aerospace industry, whether machining hard metals or aluminum, it takes the right equipment to achieve the productivity and cycle times that make a company globally competitive. One company that can attest to this is JWD Machine Inc. of Fife, Wash. For the past three decades, JWD has honed its skills in the machining of complex parts and assemblies composed of composites and hard metals, such as titanium, high-nickel alloys, and high-heat-treated steels. Its capabilities have turned heads at some of the world’s largest aerospace, defense, and transportation manufacturers – including Boeing, Goodrich Landing Gear, and GE Aviation. The company has been recognized as a Boeing Supplier of the Year award winner, and others know it outside of the aerospace industry for its development of the widely used Techni-Grip fixturing system. With their long and growing list of accomplishments, the folks at JWD understand that the company has a reputation to uphold in the face of relentless competition, which is why it embraces and leads with high-performance machining technology.
“The competitive nature of the aerospace market has a trickle-down effect on the supply chain that places ever-increasing pressure on tier suppliers like us,” says Jason Mohon, manufacturing director at JWD. “With each order, parts are growing in complexity and materials are becoming increasingly more difficult to cut. Today, we are required to hold tight tolerances when cutting titanium. This kind of intense, competitive environment requires manufacturers to remain on the cutting edge of technology in order to keep part costs low.”
Hard-Milling Determination
When machining titanium and other hard metals, reasonable tool life coupled with high metal-removal rates is critical to offering a competitive and profitable cost per part. Manufacturers attempting to remove large volumes of titanium using standard machining centers often lose that competitive edge due to limited cutter life, which results in exorbitant tooling costs. As such, JWD recognized the need for a machining platform that offered an extra-rigid construction, high-power spindle design, and efficient cooling system that would enable the company to achieve the necessary metal-removal rates and tool life to efficiently perform long-reach and large-diameter boring operations in hard metals.
“A lot of shops don’t want to mess around with hard metals such as titanium, high-heat-treated alloy steels, and stainless steel. It is difficult and expensive work – a high-risk, high-reward scenario. One mistake or broken tool can cause the loss of profit margin in just one run. When machining hard metals, a purpose-built, hard-metal machining center is a must,” Mohon explains.
After months of market research and testing, JWD invested in two Makino a81M horizontal machining centers (HMCs). It found that the integral drive, high-torque spindle on the a81M machines provided the power and rigidity necessary for large-diameter boring and face-milling operations in JWD’s hard-metal applications.
“Due to the rigidity and thermal stability of the a81M machines, we are just as precise in the evening as in the morning,” Mohon says. “In an average hard-metal application, we’re expected to hold repeatability as tight as 0.0005", and in some boring processes the requirements can be as tight as 0.00025". The a81M machines provide the perfect cutting conditions to meet and even exceed these demands, all while taking out higher volumes of material to eliminate 80% of our previous boring operations.”
According to Mohon, the enhanced power and rigidity of the a81M machines are best complemented by their high-pressure (1,000psi), high-volume (20gal/min) through-spindle coolant technology. With this coolant system, JWD is capable of meeting throughput demands without the rapid tool degradation witnessed by many standard machine platforms.
“Heat and tool stress have not been an issue for us, and if there’s anyone else who can attest to this, it’s our tooling vendor,” Mohon notes. “On the a81M machines, we are able to apply feeds and speeds that would burn up tools and rattle most standard machine platforms. For instance, in a recent titanium application, we applied a 4" shoulder-cutting face mill with 18mm inserts at 80% radial engagement and 0.375" depth of cut. This level of performance has enabled us to increase our productivity by an average of about 25%, while simultaneously extending tool life anywhere from 17% to 23% for a total reduction in tool expenditures of approximately 15%.”
Tool management has been another benefit of the a81M. At JWD, the company manages up to 60 tools on 1 machine and 137 on the other. When purchasing the a81M, these features, along with the machine’s high-performance Professional 5 (Pro 5) control, were attractive selling points.
“There are many tool management and user functions built into the a81M platform that help our productivity,” Mohon states. “The ease of the control and the tool life monitoring feature were added benefits that have made our lives easier by allowing more unattended operation, improved repeatability, and fewer scrapped parts.”
Surprising Flexibility
To further increase throughput, JWD replaced several existing machines with a set of three Makino PS95 vertical machining centers (VMCs).
“We looked at many other manufacturers before selecting the PS95 machines, but no others offered even close to the same standard features – such as the high-speed, high-power spindle, exterior tool-change access door, through-spindle coolant, and lift-up chip conveyor. On competitive machines, those features added extra cost, increasing the price by tens of thousands of dollars,” Mohon explains.
The robust design and versatility of the PS95 machines also impacted the company’s production flexibility with an ability it had not expected – high-efficiency machining of titanium and other hard metals.
Techni-Grip Workholding Systems JWD’s Techni-Grip workholding system is designed to reduce tooling design requirements, standardize fixturing, and reduce machine setup and changeover time while improving dimensional repeatability. The Techni-Grip workholding system was borne directly from JWD’s efforts to solve a number of workholding challenges that all CNC millwork creates, and was patented in 2000. The workholding system has two proven concepts: pin and hole for consistent, positive location; and the dovetail cut for exceptional gripping strength. It was designed to solve the following difficulties:
The Techni-Grip system has been shown to reduce machine and setup time by as much as 50% while streamlining workflow and production, providing standardization among product lines, reducing scrap, boosting profitability, and increasing repeatability by running multiple parts on one fixture. The product has been sold internationally to customers such as Boeing, Agilent Technologies, and many others. It enables these companies to manufacture hundreds of different applications in just a single machining operation, reducing the number of fixtures required and demonstrating lean manufacturing at its best. Every Techni-Grip system is designed to increase efficiency, simplify manufacturing processes, and strengthen profits. www.technigrip.com |
“The Makino PS95 has proven to be an economical, cost-effective machine for several aspects of our operation,” Mohon says. “We knew it was more than capable of handling standard materials, but we were shocked by the level of power and rigidity it provided in hard-metal applications. The spindle is solid and capable of holding regularity even in tough materials, including titanium.”
For example, on a particular plunging operation into 4340 high-strength steel, JWD machined the alloy at a high tensile strength of 220ksi using a 3"-diameter tool that plunged 4" down along the Z-axis into the part.
“This type of operation was historically done on a 50-taper machine, but when we tried it on the PS95 40-taper machine, we got great results, and it reduced the cycle time by about 19%,” Mohon explains. “We thought we were buying a 40-taper machine with the PS95, but what we really got was the performance of a 50-taper machine in some machining applications. Not only are we seeing a decrease in cycle times compared to other machines on the shop floor, we are able to try out new cutting approaches that would never have been possible on our previous equipment.
“Technology investments are all about improving processes and adding new capabilities to your tool kit. This has become a standard practice at JWD that we look for in every investment.”
Expanding Reach through Accurate Machining
One capability that JWD recently identified as a gap in its operations was a true full 5-axis machining platform for more modern applications featuring complex, 3D contours. This led the company to invest in a Makino D500 5-axis vertical machining center. Unlike the 5-axis rotary tables that JWD has added to its other machines, the D500 features a dual-motor direct-drive table design that provides enhanced speed and torque for precise part positioning and reductions in out-of-cut time.
“With full five-face part access, the D500 allows us to machine more complex features with fewer setups,” Mohon notes. “In addition, the machine’s precise positioning and tool-tip control have enabled us to achieve circular interpolation results within plus or minus 0.0003".”
The D500 Pro 5 control software was already a familiar feature to JWD employees, who appreciated its improvements to 5-axis machining performance and operability. Likewise, the machine’s Tool Center Point control has led to accurate control and alignment of the tool tip for improved accuracy and surface quality.
“Typically, in a 4- or 5-axis machine, you need to program from the center line of rotation to do true multi-axis machining,” Mohon says. “With the D500, you pick just one local coordinate and the machine automatically tracks that point from the center line of rotation, substantially reducing setup time and setup complexity.”
Tooling Up for Aluminum
While JWD had successfully expanded its hard milling and 5-axis machining capabilities, the company recognized that in order to rapidly grow its overall revenue by 25% to 50%, it needed to broaden its market base. To accomplish this, JWD made aggressive investments in automated aluminum machining capabilities. Its solution was a flexible manufacturing system that included the Makino Machining Complex (MMC2) and two Makino a61nx HMCs.
“Competition is already well established in the aluminum aerospace manufacturing market, so we knew we had to hit the ground running with technologies that could have us out-producing many competitors early on,” Mohon says. “The Makino automated cell enables us to run lights out, which ultimately allows us to offer a lower cost per part than several of our competitors while maintaining a healthy profit margin. The flexibility and scheduling capabilities of the MMC2 is far superior to the other technologies we investigated – the machining performance and customer support sealed the deal.”
The folks at JWD liked the cell’s ease of use compared to competitive systems. The company used Makino’s Engineering Services and training as a resource to get the cell up and running in its shop.
“Makino’s assistance with the equipment setup and application engineering saved us a lot of time in getting the cell optimized and allowed us to quickly get the most out of the machines,” Mohon says.
The a61nx machines provide a 500mm work zone and a 14,000rpm HSK 63A motor with 240Nm of torque for heavy cutting. Their robust casting design and roller-type linear guides ensure that the entire work envelope can be used effectively.
“We transferred a job from our other automated systems to the a61nx and realized a 67% decrease in cycle time,” Mohon comments. “Additionally, we’ve been able to improve efficiency and throughput in other areas of the shop floor by reallocating employees who would have been stuck stationed at each machine. They are now able to take on more challenging growth opportunities.”
The cell manages a dynamic production schedule and builds a database of parts that is ready whenever repeat production orders come through, reducing setup time, downtime, and programming. Its unattended capabilities have enabled the company to run lights out for increased overall throughput.
As the company grows, it plans to add another machine to the cell to increase capacity and keep competition at bay.
Technology Improves Efficiency
JWD’s new equipment has increased the company’s capability, productivity, and efficiency. The machines have had a positive effect on the business’ competitiveness and bottom line, and they have attracted skilled employees who are eager to work with such advanced technology.
“So much has changed since we first began operating in 1978,” Mohon says. “What JWD is doing today is utilizing the latest technology in order to stay ahead of the times, expand our complex hard metal and aluminum capabilities, and remain globally competitive. In the next five years, we want to expand our industry reach even further – bringing a variety of large aluminum and structural parts to market. To do that, we plan to continue to explore our internal capabilities and constantly improve our processes.
“What matters most to JWD is creating the highest quality product in a timely manner. We want to be efficient so that we can pass that savings along to our customer. Makino makes it easier to employ all the technical aspects that we require to do that, and we intend to continue using their technology to achieve what we need.”
JWD Machine Inc.
Fife, Wash.
www.jwdmachine.net
Makino Inc.
Mason, Ohio
www.makino.com
Elizabeth Engler Modic is the managing editor of AMD and can be reached at emodic@gie.net
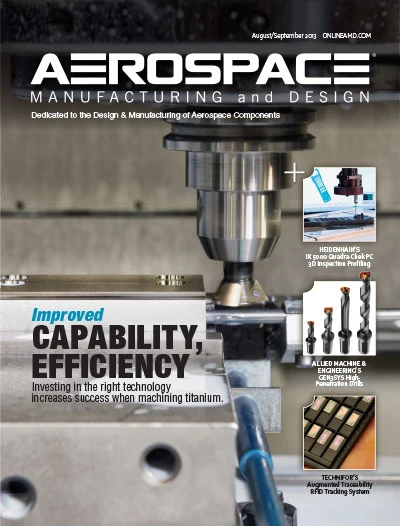
Explore the August September 2013 Issue
Check out more from this issue and find your next story to read.
Latest from Aerospace Manufacturing and Design
- GKN Aerospace accelerates additive fabrication for fan case mount ring
- Expanded offering of internal coolant live tools
- #47 Lunch + Learn Podcast with INSACO
- Doncasters’ Groton expansion reaches major milestone
- Hardware-encrypted drive with trusted supply chain
- Titanium drop bottom furnace installation underway
- Solid carbide taps for demanding materials
- The Partner Companies acquires Precision Eforming