The range of products made from composite materials like carbon fiber reinforced polymers (CFRPs), and their newer cousins, carbon nanotubes, is growing rapidly. While CFRPs are the elder statesmen of carbon manufacturing materials, they continue to find new applications as lightweight but strong materials, especially in aerospace and automotive component manufacturing fields. Meanwhile, applications involving carbon nanotubes have spiked as of late, and are expected to continue on an upward trajectory. Carbon nanotubes are primarily used as polymer reinforcements, i.e., in composites, but there is considerable potential for use with other applications.
In addition, nanoparticle properties may be substantially different from those of larger particles of the same material. In fact, parallels also have been drawn between the fiber-like shape of carbon nanotubes and asbestos.
There is a great deal of uncertainty around work environment issues when machining both CFRP and carbon nanotube, because instead of metallic chips that fall to the ground, machined composites emit dust. The general principle is that no employee should be exposed to this dust. If the dust particles are small enough, they can be inhaled into an operator’s lungs, and in the worst case, be hazardous to employee health.
When it comes to composite material, we know very little about how hazardous the dust can be. A Swedish study completed by Per Gustavsson, Maria Hedmer, and Jenny Rissler in 2011, “Carbon Nanotubes – Exposure, Toxicology and Protective Measures in the Work Environment,” states that in several studies conducted on laboratory animals, a clear correlation has been seen between the dose of carbon nanotubes and the biological effects that occur. Still, the study states, due to the lack of sufficient studies examining people, “the effects on humans after exposure to carbon nanotubes are more or less unknown.”
The potential for danger, especially in high dosage situations, or over the course of a long exposure, clearly exists. An initial priority in combating it ought to be organizing the work environment limit or eliminating potentially lingering dust. This can be achieved by installing a vacuum system to extract it. Handheld machines are perhaps too commonly used when drilling composite machining, and they make it difficult to eliminate the dust directly in the system. In such cases, personal protection equipment (i.e., protective gear, eyewear, etc.) is necessary.
Different Ways of Protection
A poll held in April of this year on http://compositemachining.org, a blog hosted by Sandvik Coromant and dedicated to new methods of machining composite materials, revealed mixed results on how operators protect themselves during CFRP machining. While some respondents use full personal protection plus a vacuum solution, others reported not using any protection at all. Using a vacuum system was the most commonly referenced solution, followed by coolant as a safety solution. Though research is scarce around this issue, Per Reinholdsson, Ph.D. and composites specialist at Exova in Linköping, Sweden, was able to shed some light on the subject.
“When machining any material, such as CFRP, emission of airborne dust will usually be formed. This dust can irritate the skin, eyes, and lungs in different ways. The smaller the size of the particles or fibers that form the dust, the higher the risk to enter the lung system,” Reinholdsson says. “The body can usually take care of the dust, but inflammatory reactions often leave scars on the lungs. So, we need to protect our eyes, skin, and lungs from the dust. Ventilation, vacuum system, dust-binding coolant, and personal protection can be used to avoid the dust from entering our bodies.”
The use of a vacuum system is the most efficient solution to eliminate dust. It’s also always recommended to measure the amount of dust to make sure that the selected solution is sufficient. According to the study, “For most work processes and handling operations the emission of carbon nanotubes into the air can probably be controlled through different types of safety and protection devices (enclosures, fume cupboards, drawbenches, local extraction, etc. One recommendation is that all processes that use nanoparticles should be enclosed and that these enclosures be designed to fit gaseous substances. Another recommendation is that safety and protection devices that are effective against dust in general are also suitable for the elimination of nanoparticles and ultrafine particles.”
Potentially Dangerous Materials
Composites may be comprised of different types of fiber reinforcements, – e.g., glass fiber, carbon fiber, and aramid fiber composites. Dust from fibers that are classified as “crystalline” is usually more hazardous to health because the fibers decompose into thinner fibers and can therefore enter into the alveoli in the lung system. Aramid fibers can be considered as crystalline but are softer and more flexible than other crystalline fibers, such as asbestos fibers. This makes it easier for the body to handle the aramid fibers. Generally, you can say that small and very hard dust that easily enters the body can irritate and give inflammatory reactions. However, the knowledge around the nature of composite dust is still very limited, Reinholdsson admits.
Carbon nanotubes are an even bigger question mark. Composite materials like CFRPs typically don’t break into the hazardous small, hard, crystalline fibers that characterize asbestos. For that reason, the limitations are not as strict for composite material as they are for asbestos-like materials. Nano-particle composite material, on the other hand, is an area of great interest for many industries due to its unique properties.
The material is not widely used yet, and knowledge in this area is still very limited when it comes to impact on health and environment. These materials represent an entire class of nanomaterials instead of one material, as there are many different diameters, lengths, chiral angles, chemical functionalizations, purities, and bulk densities (which are often related to dusting propensity).
According to the study, “a characteristic of a carbon nanotube is that its mass is small, but the number of nanoparticles is very large because of the low density. Most exposure measurements where carbon nanotubes are produced or used have been traditional dust measurements, determining mass concentration. The measured levels have typically been 0.1mg/m3 or less, but even higher concentrations have been reported. Results from this type of measurement are uncertain, because the method does not specifically measure the carbon nanotubes but also includes other airborne particulates in the determined mass dose. To date, the measurement methodologies that have been used have mainly provided exposure data for emissions and possible exposure to carbon nanotubes at workplaces and supporting documentation for the evaluation of safety and protection devices. Measurements have been made over short periods and of a few number of work operations/exposure situations. Furthermore, different types of sampling equipment have been used, making it difficult to compare the results.”
Don’t Cut Corners
Quite a few of the respondents to the composite machining poll referenced the use of coolants as a means to encapsulate dust particles and eliminate them from breathable air. Reinholdsson says that might be one solution, but be careful.
“Specific dust-binding coolant can in some cases be sufficient, but to be sure, you should make a risk analysis and measure both the amount of dust and the nature of it,” he says.
When it comes to dust, you can’t trust what you see or feel, as the particles and/or fibers aren’t visible. Measurements can be made through an instrument that gives you the dust density and through filters that can give you the exact characteristics of the dust.
“To avoid the dust, I know that it’s sometimes easier said than done. When you work all day with a hand-drill or similar where a vacuum system doesn’t apply, you probably don’t want to go overboard and wear a space suit. You need to be aware of the risks, though, and everyone machining composite material should definitely perform a risk analysis and measure. When you understand the risks, it is much easier to find an appropriate solution. That’s the most important message,” Reinholdsson says.
When working with composites, CFRPs, or carbon nanotubes/nanoparticles, the study agrees that a precautionary principle should prevail: “If working with carbon nanotubes, a high level of elimination controls should be used so that occupational exposure is reduced to the lowest possible level. Personal protective equipment in the form of respiratory protection equipment, gloves, and protective clothing may also need to be used when there are limited capabilities of measuring and assessing occupational exposure to carbon nanotubes.”
Watch it: Learn more about composite machining through a series of videos available at http://bit.ly/15Nku26.
Sandvik Coromant
Fair Lawn, N.J.
www.sandvik.coromant.com
About the author: Mats Hedberg holds the position of environment, health, and safety (EHS) at Sandvik Coromant and can be reached via email at mats.hedberg@sandvik.com.
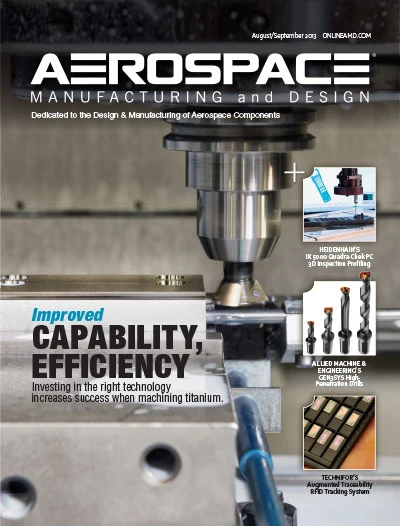
Explore the August September 2013 Issue
Check out more from this issue and find your next story to read.
Latest from Aerospace Manufacturing and Design
- Revitalizing the Defense Maritime Industrial Base with Blue Forge Alliance
- Safran Defense & Space opens US defense HQ
- Two miniature absolute encoders join US Digital’s lineup
- Lockheed Martin completes Orion for Artemis II
- Cylinder CMMs for complex symmetrical workpieces
- University of Oklahoma research fuels UAS development
- Motorized vision measuring system
- Everyone's talking tariffs