![]() |
For many people, the name Lufthansa is ?a password for safe, comfortable air travel. The Lufthansa Technik group of companies (LHT Group), which is responsible for carrying out aircraft servicing and maintenance, plays a significant role in maintaining that reputation. Lufthansa Technik is one of the few service companies allowed to overhaul aircraft and engines from a wide variety of manufacturers. For certain procedures and manufacturers, the Lufthansa Technik site in Hamburg, Germany, is the only qualified repair location in the world.
Sophisticated Engine Repairs
Repairs to engine housings represent a particularly difficult challenge. Engine housings are complex, heavily stressed components made of materials that are expensive to buy and process. In scheduled maintenance, it is sometimes possible to replace only those sections that show signs of mechanical and thermal stress – an alternative that is technically challenging, but financially, extremely interesting compared with using new parts. First, to do this, the component to be overhauled is measured precisely and a CAD model of its actual shape is created. Next, the worn sections from the engine components are replaced with new material, which is then reworked so that it exactly matches the previous structure in terms of shape, size, and accuracy of fit. The repair technology requires machining centers of a particular size and quality, as Andreas Tölle, project engineer at Lufthansa Technik in Hamburg, explains: “Our large vertical turning and grinding machines from Jungenthal, with their solid and reliable mechanics, are completely indispensable for this type of work.” They are regularly overhauled to reflect the state of the art in terms of both electrical engineering and CNC technology.
Simplifying Programming
Lufthansa Technik in Hamburg recently turned to Siemens to retrofit the drive technology and control system on its Jungenthal vertical turning and grinding machining center. “Everything we produce is a one-off and needs to be individually programmed and processed,” Tölle says. “Our staff also needs to be able to operate all of the machines easily. That’s why we are gradually converting all our machining centers to use CNCs with shop floor software from Siemens.”
![]() |
The electrical engineering part of the retrofit included all of the axis drives and the CNC system. The Sinumerik 840D sl, with its Sinumerik Operate graphical user interface and integrated ShopTurn shop floor software, made it possible to combine the turning and grinding processes that previously required two CNCs into a single control system, thus saving one entire control panel. With the turning and grinding processes now combined in a single control system, programming and program management have also been considerably simplified. The old CL800 cycles have been translated one-to-one into ISO cycles for the new control system. On the OP 015 control panel, more information can be visualized in a clear and transparent manner than ever before. For example, it is now already obvious during the simulation phase whether a tool can be used at a particular angle of approach. In ShopTurn, which is also integrated into Sinumerik Operate, contour sections can be easily cut out and inserted, using the copy-and-paste function. The panel is also extremely useful when operating in manual mode.
Efficient, Economical
To exploit the capabilities of the Sinumerik tool management system fully, Lufthansa Technik retrofitted the tool turret with Capto toolholders. This allows the Jungenthal machine to be specifically fitted with ready-made tools, simplifying in-process tool changes, eliminating the need for time-consuming scratching, and allowing entire production sequences to be combined into cycles and programmed processes. “More efficient tool and program management has increased our processing speeds on average between 10% and 20%,” Tölle explains.
Equipped with the new Sinumerik CNC, Simotics S-1FK7 servomotors, and the Sinamics S120 drive system, including actively regulated in-feed, the Jungenthal machine now has the flexibility to deliver the efficient production processes required for aircraft maintenance. Even without counting the work saved on foundations and infrastructure, the retrofit proved particularly economical when compared to the cost of buying a new machine.
This resilient machine will probably also last longer than a newer model built today, Tölle says, who is already thinking ahead to the next retrofit with Siemens as a partner.
Watch: View the video at http://bit.ly/18kRjUz to learn more about the Sinumerik 840D sl CNC.
Siemens Industry Inc. Drive Technologies – Motion Control (Machine Tool)
www.usa.siemens.com/cnc
Elizabeth Engler Modic is managing editor of AMD and can be reached at emodic@gie.net.
Get curated news on YOUR industry.
Enter your email to receive our newsletters.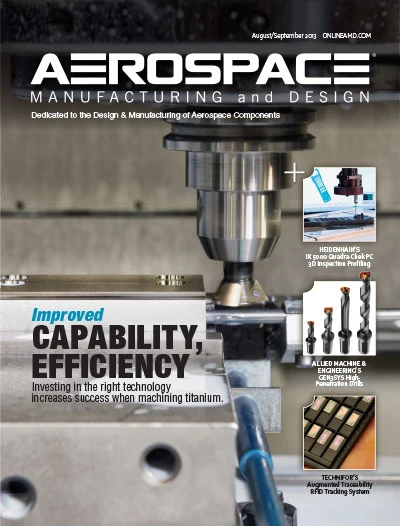
Explore the August September 2013 Issue
Check out more from this issue and find your next story to read.
Latest from Aerospace Manufacturing and Design
- Embraer tests wing for new technologies demonstrator
- Mitutoyo America’s SJ-220 portable surface roughness tester
- #55 - Manufacturing Matters - A Primer on Defense Contract Manufacturing
- Registration is open for April’s Manufacturing Lunch + Learn!
- Natilus begins search for new home to build world's most efficient commercial aircraft
- Aerospace Industry Outlook webinar is back by popular demand
- Automation Webinar with Visual Components
- PrecisionX Group expands manufacturing operations