Behind the brick walls of a seemingly quiet building on the campus of Wichita State University (WSU) in Wichita, Kan., research engineers from the National Institute for Aviation Research (NIAR) literally and virtually push, pull, blast, and crash airplane parts to understand when and how they fail.
On any given day, NIAR researchers can be found snapping composite material samples in load frames that deliver up to 500,000 lb of axial force; blasting aircraft models with winds up to 240mph; crashing airplane seats using up to 75Gs of force; and subjecting electronic devices to the effects of lightning, heat, humidity, and salt fog.
“We like to say we operate Disneyland for engineers,” says Tom Aldag, NIAR’s director of research and development. “If you want to know how an article is going to perform on an aircraft, we can tell you.”
Drawing on the diverse knowledge of a staff that includes everything from seasoned industry professionals and Ph.D.s to student assistants from WSU’s College of Engineering, the institute provides research, design, testing, and certification. Those offerings are available in the area of advanced coatings, aerodynamics, aging aircraft, composites and advanced materials, computational mechanics, crash dynamics, environmental effects, full-scale structural test, human factors, mechanical test, metrology, nondestructive test, reverse engineering, and virtual reality.
With accreditation from Nadcap, A2LA, and ANSI, NIAR’s institute’s client list spans a global database of more than 250 and includes manufacturers like Airbus, Boeing, Bombardier, Beechcraft, Cessna, General Atomics, Gulfstream, and Lockheed Martin, as well as government agencies like the FAA, EASA, NASA, U.S. Air Force, and U.S. Navy.
Innovative Partnerships
Like its aerospace clients, in recent years, the institute has developed innovative strategies to diversify its business model. Drawing on the strength of its Computational Mechanics Lab, the institute partners with manufacturers to form product design centers that employ design engineers who work for one client during product development. Upon completion of a project, engineers are assigned to a new team, allowing for a stable and skilled workforce. The Computational Mechanics Lab and design center capabilities include methodology in crashworthiness, injury biomechanics, structures, numerical optimization techniques, virtual product development, and certification. Projects are overseen by Dr. Gerardo Olivares, an expert in computational analysis and crashworthiness.
The institute’s location in the Air Capital of the World has given it the opportunity to foster strong relationships with manufacturers, such as Bombardier and Beechcraft.
In 2004, NIAR took over operations of the company’s full-scale structural test lab. The partnership worked so well for both parties that NIAR also took over operations of Beechcraft’s metrology and environmental test labs.
“The transfer allows Beechcraft to concentrate on product development and manufacturing,” says Paul Jonas, director of NIAR’s Environmental Test Labs. “And we fill in our test schedule with additional clients, allowing us to maintain a staff and facility that is well-equipped to handle virtually any test variation.”
Dynamic Testing
The Composites & Mechanical Test Labs can make and break materials all in a day’s work. The lab performs coupon-level lay-up, bonding, and static and fatigue testing for up to 34,000 articles per year. The lab’s newest addition is a 500kip axial and torsion load frame with an active working region of 8ft.
For items on a larger scale, clients visit NIAR’s Aircraft Structural Test and Evaluation Center, a new 120,000ft2 facility large enough to accommodate transport aircraft and modern airliners. Here, engineers in the Full-Scale Structural Test Lab assess the structural performance and durability of aerospace and related structures by performing full-scale and component testing (static, durability, and damage tolerance), pressure cyclic testing, hail strike testing, and material testing. Driven by the force of an MTS Systems model 888.20 accelerator sled system, the Crash Dynamics Lab performs impact testing for transportation seats and restraints systems under dynamic impact conditions up 75Gs. The lab is equipped with high-resolution, high-speed digital video, and test dummies.
The Environmental Test Labs meet environmental standards regulated by the FAA technical standard orders using RTCA DO-160 certification standards. The lab’s experienced staff can accommodate testing in temperature, humidity, shock, vibration, explosion proofness, salt fog, magnetic effects, power input, voltage spike, radio frequency (RF) susceptibility, RF emissions, lightning, and icing. The labs also work directly with manufacturers to develop methods for performing customized environmental tests.
Nondestructive Testing
NIAR’s Walter H. Beech Wind Tunnel is older than the institute itself. Established in 1948, the tunnel is now a modern state-of-the-art facility capable of generating wind speeds of up to 240mph.
The Aging Aircraft Lab supports the federal government and the aviation industry with investigations into the effects of age on commercial and military aircraft.
The Human Factors & Aviation Psychology Lab provides practical psychology to the needs of defense industries, government authorities, the U.S. military, and a variety of other institutions.
Training
The institute is also a partner in Wichita’s National Center for Aviation Training, an integrated aviation training facility that combines research and technical training to ensure a workforce skilled in the latest manufacturing technologies. At this facility, NIAR operates three laboratories that provide both research and training in advanced coatings, nondestructive test, and CAD/CAM.
The Advanced Coatings Lab performs research and development for paint and coatings including customized formulation of interior and exterior high-performance coatings; material/process evaluation and optimization; coatings application process improvement; and product testing to military, OEM, and industry specs.
The Nondestructive Test Lab specializes in testing and curriculum for penetrant inspection, magnetic particle, radiographic, eddy current, ultrasonic, visual inspection, and bond. Students of the NDT Lab are expected to master coursework from the American Society for Nondestructive Testing Level I and II certification.
The CAD/CAM Lab is home to some of the aviation industry’s finest CATIA design engineers. The lab develops and publishes its own course materials and offers CATIA and ENOVIA courses at a non-credit level, or for credit through WSU or Wichita Area Technical College. Courses can be tailored toward industry need and taught onsite across the country. The lab also provides design consultation and reverse engineering services. Within one lab, NIAR engineers can reverse engineer a part, make design modifications, and produce a prototype that can be used to test the new design.
National Institute for Aviation Research Wichita State University
Wichita, Kan.
www.niar.wichita.edu
About the author: Tracee Friess is the director of communication and special programs, for the National Institute for Aviation Research, Wichita State University, and can be reached at tfriess@niar.wichita.edu.
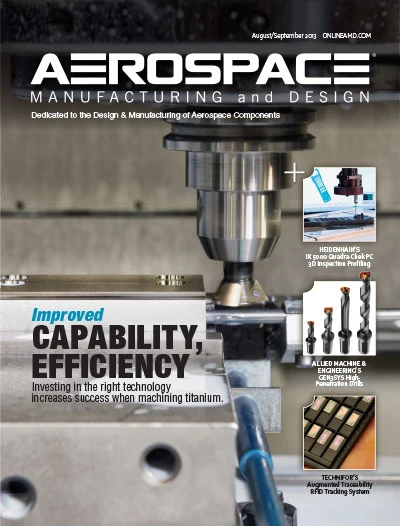
Explore the August September 2013 Issue
Check out more from this issue and find your next story to read.
Latest from Aerospace Manufacturing and Design
- Embraer tests wing for new technologies demonstrator
- Mitutoyo America’s SJ-220 portable surface roughness tester
- #55 - Manufacturing Matters - A Primer on Defense Contract Manufacturing
- Registration is open for April’s Manufacturing Lunch + Learn!
- Natilus begins search for new home to build world's most efficient commercial aircraft
- Aerospace Industry Outlook webinar is back by popular demand
- Automation Webinar with Visual Components
- PrecisionX Group expands manufacturing operations