GE Aviation R&D Center Receives Equipment, on Track for Opening
GE Aviation’s Electrical Power Integrated Systems Center (EPISCENTER) has received equipment that will enable the testing of an aircraft’s complete electrical power system.
The most recent equipment delivery includes drive stands, vibe tables, and a temperature altitude chamber. The drive stands include dynamic engine simulation. One drive stand pair is configurable for up to 3,000hp testing of very large generation equipment.
The center, located on the University of Dayton campus in Dayton, Ohio, is nearing completion for the official opening this fall. When finished, the $51 million center will include a four-story, 50,000ft2 office building connected to an 88,000ft2 world-class electrical power laboratory.
“Next-generation aircraft will demand up to four times more power than today for key functions and systems,” according to Vic Bonneau, president of Electrical Power Systems for GE Aviation. “This center will yield system-level advantages so that our customers can more rapidly benefit from this trend in energy management, climate control, radars and sensors, silicon carbide-based power conversion, and electric actuation, to name a few.”
The EPISCENTER potentially will employee 150 to 200 researchers in the next five years, depending on future research programs. www.ge.com/aviation
Bilz Tool Partners with Diebold Germany for North America
Bilz Tool USA is now partnering with Diebold Germany to serve as the importer for Diebold products for the North American market. Diebold is a manufacturer of ThermoGrip toolholders, high-precision spindles, and tooling gages. Diebold’s horizontal shrink-fit units and water chillers will complete the current vertical shrink-fit products offered by Bilz.
The expansion of the product offering will strengthen Bilz’s support of the die/mold, aerospace, and medical industries, and the firm will increase its national warehouse space so that products can be shipped from inventory in the U.S.
All technical and product application support will be handled by Bilz Tool USA, as will direct customer orders. www.bilzusa.com
Saint Jean Aero Opts for Starrag Technology
Executives from the Aerospace Competence Center at Saint Jean Industries SA, Geneva, Switzerland, have recently ordered an STC 1250 5-axis machining center from Starrag AG. Known as a producer of components in titanium and Inconel alloys, Saint Jean Aero (SJA) had received a Starrag STC 1000 5-axis machining center in 2011, with the acquisition of RUAG. The new STC 1250 5-axis machining center will enable SJA to cut very large and heavy structural components in titanium (maximum workpiece weight: 5,000kg). Since the second STC machine tool will not start production until the summer of 2014, Starrag is offering a special service during the transition period and will be manufacturing titanium structural components, to be deployed on the A380, for Saint Jean Aero. www.st-ji.com; www.starrag.com
Moves to Gold PTC Partner Status
Gibbs and Associates has moved from a Silver Tier Partner to a Gold Tier Partner within the PTC PartnerAdvantage Program. The upgrade to the Gold Tier, which provides enhanced access to a comprehensive suite of capabilities, followed an extensive review of GibbsCAM, its integration with PTC Creo design software, and GibbsCAM’s CNC programming capabilities.
The upgraded status arose, in part, from GibbsCAM’s increasing use of PTC GRANITE software to add automation features for PTC Creo users, and its integration with PTC Creo 2.0 with GibbsCAM 2013. PTC Creo users are assured compatibility with GibbsCAM since Gibbs incorporates the PTC GRANITE 3D library for CAD file interoperability. This GibbsCAM software integration provides PTC Creo users all the functionality required to program lathes, 2- to 5-axis mills, MTMs, and wire EDM machines. www.gibbscam.com; www.ptc.com
AI Teaches LearningGripper How to Grip
Festo engineers recently demonstrated an automated gripping system that used artificial intelligence (AI) to teach itself how to manipulate different shaped objects. The demonstration involved the pneumatically actuated LearningGripper teaching itself to handle a small ball and then orienting the Festo logo on the ball in a specific direction.
The LearningGripper is a four-fingered gripper that looks like an abstract form of the human hand. The four fingers of the gripper are actuated pneumatically by 12 bellows actuators with low-level pressurization. Learning algorithms take the place of highly complex programming. The LearningGripper picks up motion sequences through learning by reinforcement.
“Today an enormous amount of time and energy goes into programming machines to handle a range of products,” states Richard Huss, Festo president and CEO. “Setup and programing are major manufacturing cost components for machine builders. This LearningGripper demonstration is a forerunner of a time where these programming costs – setup and maintenance – will be diminished. These new generation machines will self-optimize their own performance.” www.festo.com/us
Get curated news on YOUR industry.
Enter your email to receive our newsletters.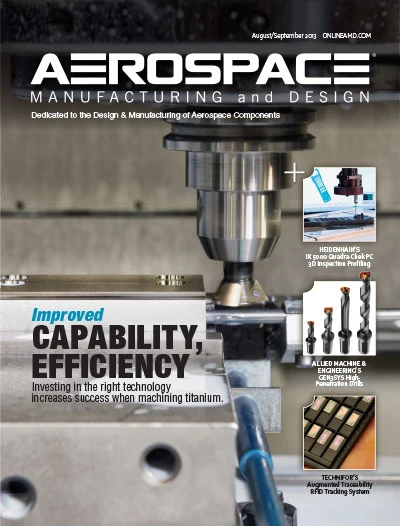
Explore the August September 2013 Issue
Check out more from this issue and find your next story to read.
Latest from Aerospace Manufacturing and Design
- Embraer tests wing for new technologies demonstrator
- Mitutoyo America’s SJ-220 portable surface roughness tester
- #55 - Manufacturing Matters - A Primer on Defense Contract Manufacturing
- Registration is open for April’s Manufacturing Lunch + Learn!
- Natilus begins search for new home to build world's most efficient commercial aircraft
- Aerospace Industry Outlook webinar is back by popular demand
- Automation Webinar with Visual Components
- PrecisionX Group expands manufacturing operations