As aerospace manufacturing continues to ramp up in North America, the need has arisen for a “right-sized” 5-axis horizontal machining center for complex aluminum aerospace parts.
The a61nx-5E offers an appropriately sized design for small components featuring 3D contours without compromising the highly productive spindle performance and 5-axis capabilities of larger aerospace machines.
Featuring the same robust design and proven reliability of the smaller nx-Series horizontal machining centers, but with the added speed and performance of larger MAG-Series machines, the a61nx-5E machine differentiates itself from similar 5-axis horizontal platforms with an innovative pallet-change system, advanced twin direct-drive rotary table design, and availability of a high-power 24,000rpm spindle. The result is a highly productive solution that can provide up to 310in3 of metal removal per minute.
Optional Spindle Configurations
|
Enhanced rigidity is provided through a three-point bed casting and tiered column structure, with X-, Y-, and Z-axis travels of 730mm (28.7"), 730mm (28.7"), and 680mm (26.8"), respectively. Linear acceleration is 1G on the X- and Y-axis, and 0.8" the Z-axis. The direct-drive rotary tables offer improved access to all sides of a part, especially when using shorter tools – yielding improved performance and accuracy. A closed-loop thermal management system ensures reliability and accuracy by removing heat generated by the large direct-drive rotary table motors. The a61nx-5E also uses the same proven tool magazines as the nx-Series of machines with a ring-style ATC60 as standard. Optional matrix magazines with capacities of 133, 218, or 313 are available options.
The unit comes equipped with a standard 14,000rpm spindle with 240Nm of duty-rated torque and 30kW of duty-rated output. This configuration is suited for the premium job shop needing a 5-axis platform to machine a wide variety of materials.
An optional 24,000rpm high-speed spindle offers the aluminum roughing and finishing capabilities that are typically associated with much larger MAG machines into a smaller platform, enabling cycle-time reductions of 45% to 50% in complex parts, when compared to a typical 20,000rpm high-speed spindle.
The pallet changer eliminates material-handling challenges by enabling operator-friendly part loading and unloading via a 45° pivot point that transfers pallets from a vertical to horizontal orientation. The loading height is 32" off of the floor to improve safety at the loading station. Workpiece limitations are 600mm × 385mm (23.62" × 15.15"), accommodating easy crane clearance through the doors. For customers wishing to add automation to their 5-axis machining, this pallet-change system is fully compatible with the manufacturer’s MMC-R robotic fixture plate distribution system.
Makino Inc.
Mason, Ohio
www.makino.com
Get curated news on YOUR industry.
Enter your email to receive our newsletters.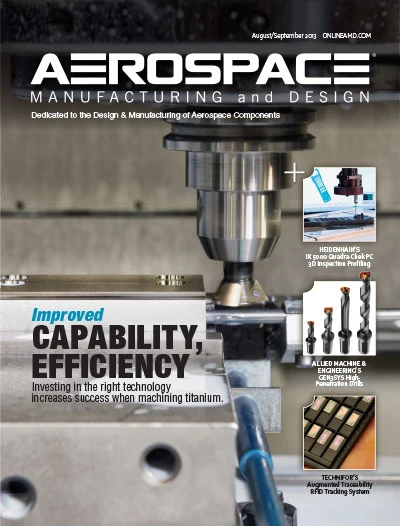
Explore the August September 2013 Issue
Check out more from this issue and find your next story to read.
Latest from Aerospace Manufacturing and Design
- Embraer tests wing for new technologies demonstrator
- Mitutoyo America’s SJ-220 portable surface roughness tester
- #55 - Manufacturing Matters - A Primer on Defense Contract Manufacturing
- Registration is open for April’s Manufacturing Lunch + Learn!
- Natilus begins search for new home to build world's most efficient commercial aircraft
- Aerospace Industry Outlook webinar is back by popular demand
- Automation Webinar with Visual Components
- PrecisionX Group expands manufacturing operations