With terms like micro, nano, and even pico increasingly in vogue, anything that can provide packaged products in the smallest possible sizes and meet all application requirements is welcome. Miniature motors plays a critical role in this aspect. With growing application demands, these motors now meet a wide range of capabilities.
Technologies overview
Frequently used miniature motor solutions include brushed DC motors, brushless DC motors (BLDC), and stepper motors with each solution having merits and limitations for specific applications. For applications that require higher acceleration, lower weight, better efficiency and power density, brushed DC coreless motors are usually preferred, while BLDC motors are mainly for moderate to high power densities and longer motor life at very high speeds.
Stepper motors play an important role for any aerospace and defense (A&D) application that requires precise positioning. A&D application requirements, such as criticality of weight and space, also limit input power since multiple applications typically are running with an aircraft. Temperatures may vary in extremes from -60°C to 150°C with around 95% related humidity (RH). Tolerance to noise, vibrations and shocks, and electromagnetic interference and capability (EMI-EMC) A&D application, require optimized miniature motion products. Each application is unique, and extra attention by designers in material systems, lubrication, and mechanical systems ensures meeting critical motion requirements. An optimal design enables the motor to operate at peak efficiencies in extreme environments, and more importantly, ensures that the motor operates safely and reliably under such conditions.
Aerospace applications
A&D applications often require innovative, reliable, safe, and high power density products. Applications such as valve actuators perform critical functions, from regulating the flow of engine fuel to controlling the air flow into environmental systems. Various types of motors with gearboxes need to be used, depending upon the load to be overcome in these applications. A gearbox with planetary arrangement provides high power density, compactness, lower noise, and better efficiencies. Compound gear trains are preferred for extreme low noise and higher efficiencies.
Flow control valves need very accurate positioning of movable parts, enabled via high resolution encoders. Aerospace designers typically choose encoders with greater than 256 lines of resolution. With magnetic encoders, resolution can go up to 4,096 pulse per revolution (PPR).
Limitations on current consumption require optimized design of motors needs to ensure solutions run efficiently. In order to withstand extreme temperatures, material systems and lubricants need to be properly selected.
To limit EMI-EMC when equipment running is in the vicinity that may affect the functionality of motion control equipment, a solution is to disengage the motor from the outer environment and use electronic filters to reduce emissions.
Portescap has developed a complete driveline solution with a motor, gearbox technology, an encoder, and electronic filters and magnetic brake. All stringent A&D requirements are met with using the smallest of sizes.
Conclusion
Precision motors for the specialized A&D market must be customized for each specific application. Due to unique requirements in this market, engineers must thoroughly understand how to optimize design criteria as dictated by industry requirements. Manufacturers offering a variety of motor technologies can analyze demands across technologies, understand design considerations, and offer multiple custom motion control solutions.
A&D applications continue to grow with advancements in technology. Refining design with material advancements to provide optimized motion control solutions will continue to be the challenge in this ever-evolving market. Size, efficiency, safety, reliability, and a complete driveline solution will be key to serve motion-critical applications.
Portescap
www.portescap.com
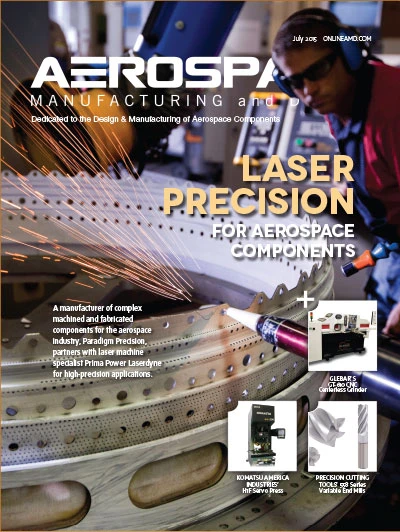
Explore the July 2015 Issue
Check out more from this issue and find your next story to read.
Latest from Aerospace Manufacturing and Design
- NASA selects instruments for Artemis lunar terrain vehicle
- Twin-cutter boring head
- Bell awarded funding for X-plane build phase of SPRINT program
- Shaft coupling clamps
- #46 Lunch + Learn Podcast with SMW Autoblok
- Gleason Corp. acquires the Intra Group of Companies
- Thread milling cutter reduces cutting pressure, vibration
- Malaysia Aviation Group orders 20 more Airbus A330neo widebodies